In the ever-evolving world of manufacturing and design, 3D printing emerges as a beacon of innovation, transforming ideas into tangible realities. Among the myriad of technologies powering this revolution, one stands out for its precision and efficiency: Digital Light Processing (DLP) 3D printing. This advanced method, often overshadowed by its more discussed counterparts, is the unsung hero of the 3D printing world, offering a unique blend of speed and detail that is reshaping industries.
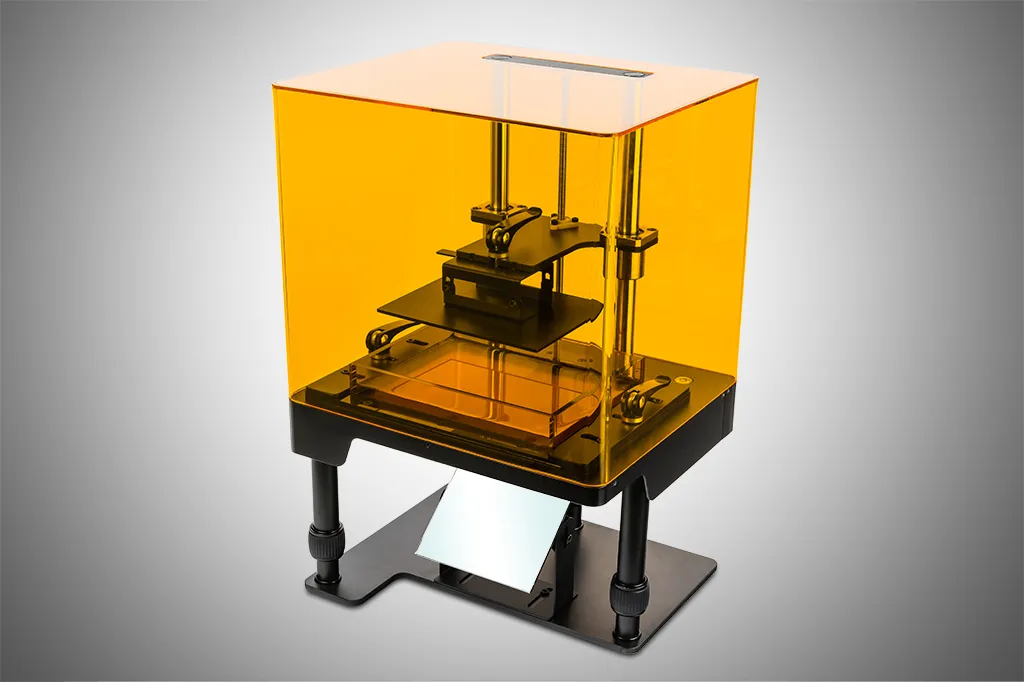
Imagine the possibility of creating intricate jewelry or detailed dental prosthetics with the finesse of a master craftsman, but at the speed of modern machinery. DLP 3D printing makes this a reality, leveraging light to turn liquid resin into solid, functional objects with an unprecedented level of detail. It’s a technology that’s not just for the future—it’s crafting the present, one layer at a time.
As we embark on this journey to unravel the intricacies of DLP 3D printing, we’ll delve into its mechanics, explore its applications, and understand how it compares to other 3D printing methods. Whether you’re a seasoned engineer, a curious hobbyist, or simply fascinated by the prospects of 3D printing, this article will illuminate the paths of creativity and innovation that DLP technology paves. So, prepare to be enlightened as we shine a light on the basics of DLP 3D printing technology—a tool that’s sculpting the future, one pixel at a time.
Understanding DLP 3D Printing
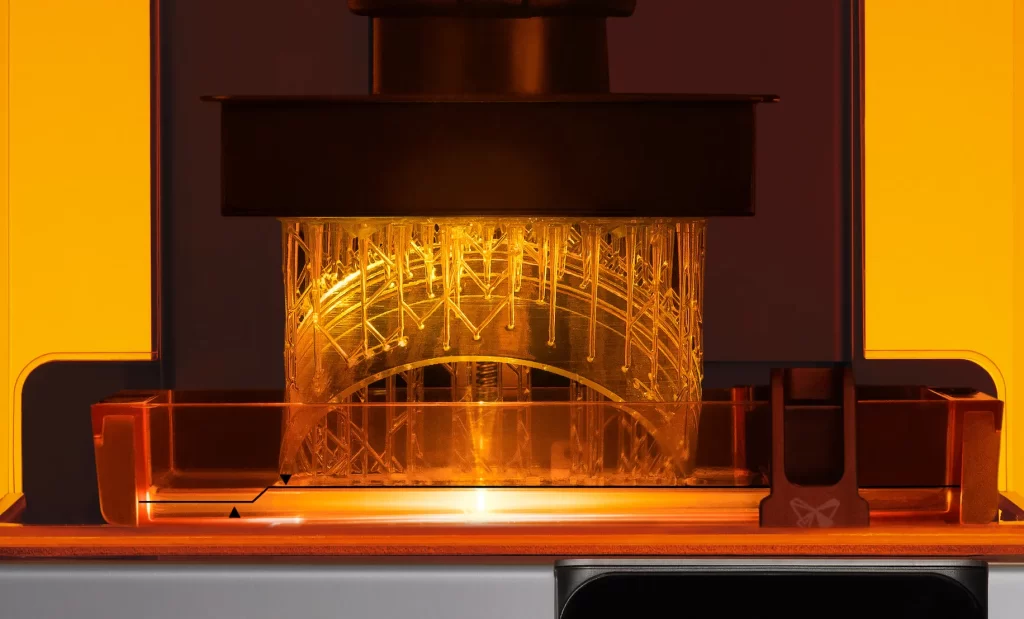
Digital Light Processing (DLP) is a type of vat polymerization 3D printing technology that uses light to cure photopolymer resin. But what sets it apart from other forms of 3D printing, and how exactly does it work? In this deep dive, we’ll explore the mechanics behind DLP 3D printing, its components, and the nuances that make it a preferred choice for professionals in various fields.
What is DLP 3D Printing?
DLP 3D printing, at its core, is a marvel of modern engineering that harnesses the power of light to transform liquid resin into solid objects. It’s akin to capturing the essence of a moment with a camera, but instead of a fleeting image, you get a physical object that you can hold in your hands.
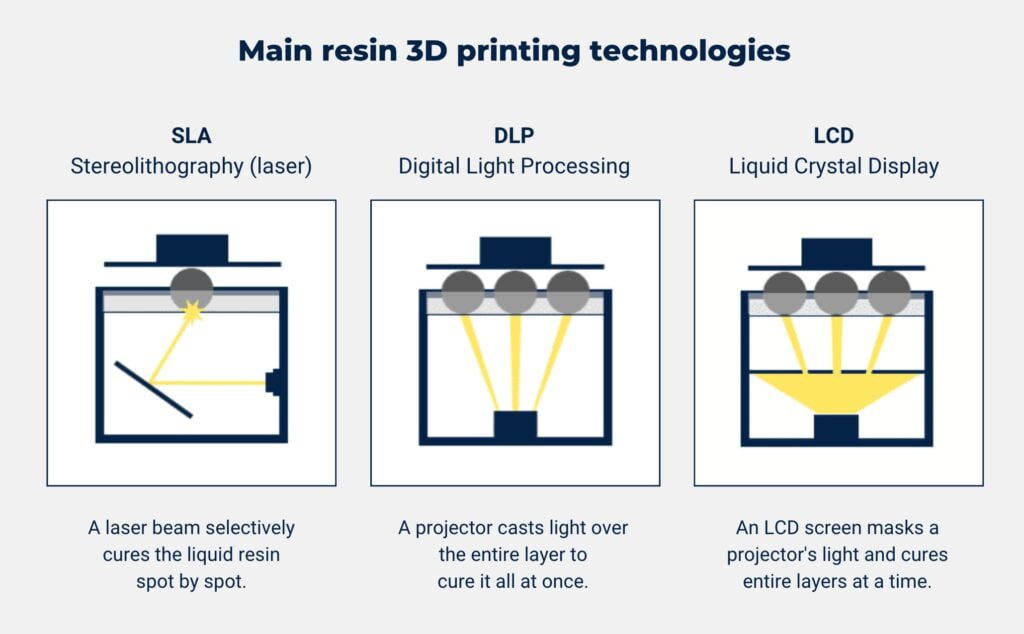
Key Characteristics of DLP 3D Printing:
- Precision: Capable of intricate details.
- Speed: Faster than some other 3D printing technologies.
- Efficiency: Uses light efficiently to cure resin.
How Does DLP 3D Printing Work?
The process begins with a vat of photopolymer resin. A digital light projector screen then projects an image of a layer onto the surface of the liquid resin, hardening it with pinpoint accuracy. This process repeats, layer by layer, until the object is fully formed.
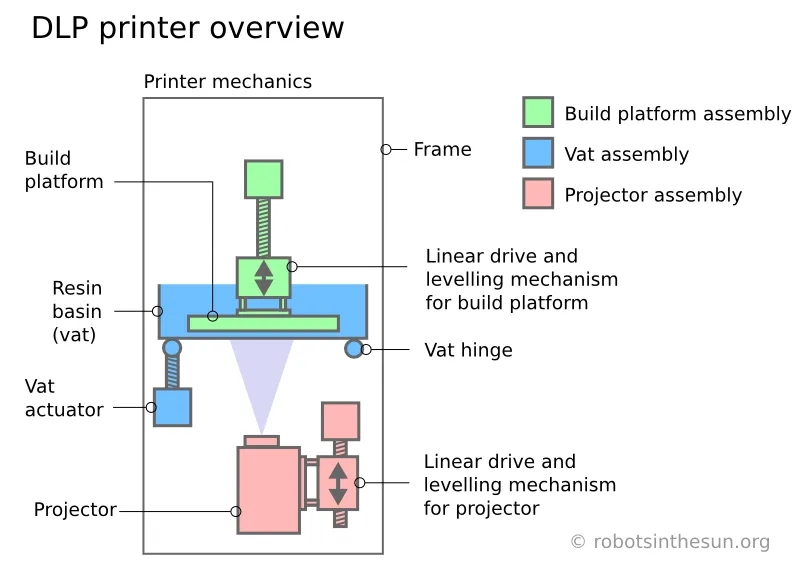
Step-by-Step Breakdown:
- Preparation: The build platform lowers into the resin vat, leaving a thin layer of resin above it.
- Exposure: A digital light projector exposes the resin to UV light, curing and solidifying the specific areas.
- Lift and Repeat: The build platform lifts, allowing more resin to flow beneath it, and the process repeats for the next layer.
- Completion: After the final layer is cured, the object is removed from the vat for cleaning and post-processing.
Comparison with SLA Printing:
- DLP uses a digital projector to flash a single image of each layer all at once.
- SLA uses a laser to draw out each layer, which can be more time-consuming.
Components of a DLP 3D Printer
Understanding the components of a DLP 3D printer is crucial to appreciate the technology’s capabilities fully.
- Light Source: The heart of the DLP printer, usually a UV light projector, which cures the resin.
- Build Platform: Where the object is formed, moving incrementally to allow new layers to be cured.
- Resin Tank: Holds the photopolymer resin, typically transparent to allow the passage of light.
Types of Resins Used:
- Standard Resins: General-purpose for prototyping and hobbyist projects.
- Castable Resins: Designed for creating molds for casting metals.
- Flexible Resins: Offer varying degrees of flexibility and strength.
The Role of Digital Light Projectors in DLP
The digital light projector is what distinguishes DLP from other 3D printing technologies. It’s not just any light source; it’s a sophisticated system that can project images with incredible detail, allowing for the creation of complex geometries and textures that were once thought impossible.
Advantages of Using Digital Light Projectors:
- Uniform Curing: Ensures each part of the layer cures uniformly, leading to consistent mechanical properties.
- High Resolution: Allows for finer details in the printed objects.
- Speed: Can cure entire layers at once, making it faster than point-to-point methods like SLA.
Materials and Applications of DLP 3D Printing
When we talk about the magic of DLP 3D printing, it’s not just the technology that’s captivating, but also the diverse materials that bring these creations to life. Each resin has its own set of properties, making it suitable for specific applications. In this exploration, we’ll delve into the various resins used in DLP 3D printing and the myriad of applications they empower.
Materials Used in DLP Printing
The choice of material in DLP 3D printing is pivotal as it dictates the physical properties and the potential use of the printed object. Here’s a guide to the most commonly used resins and their characteristics:
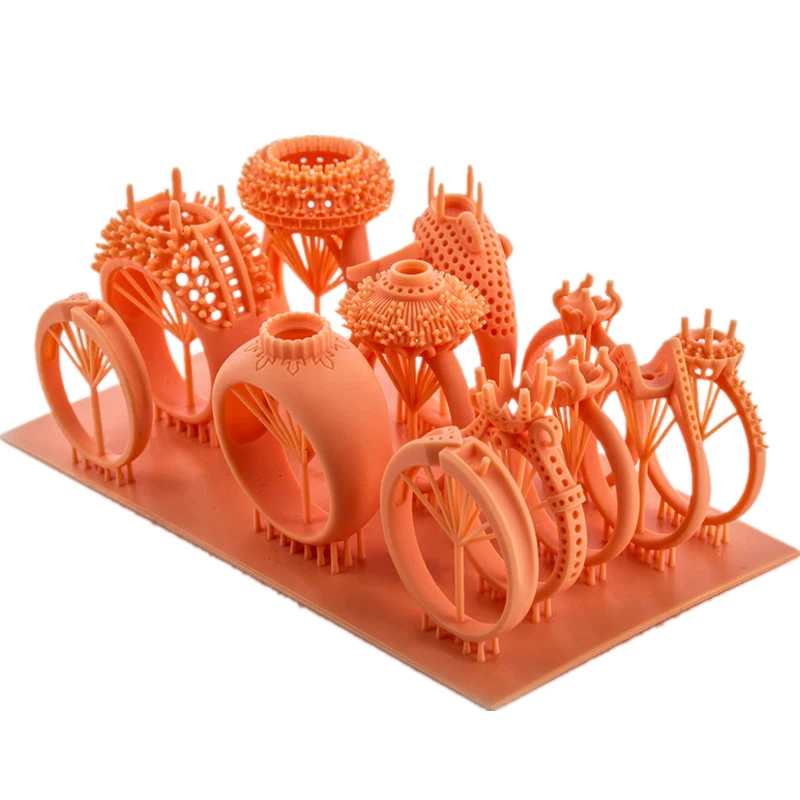
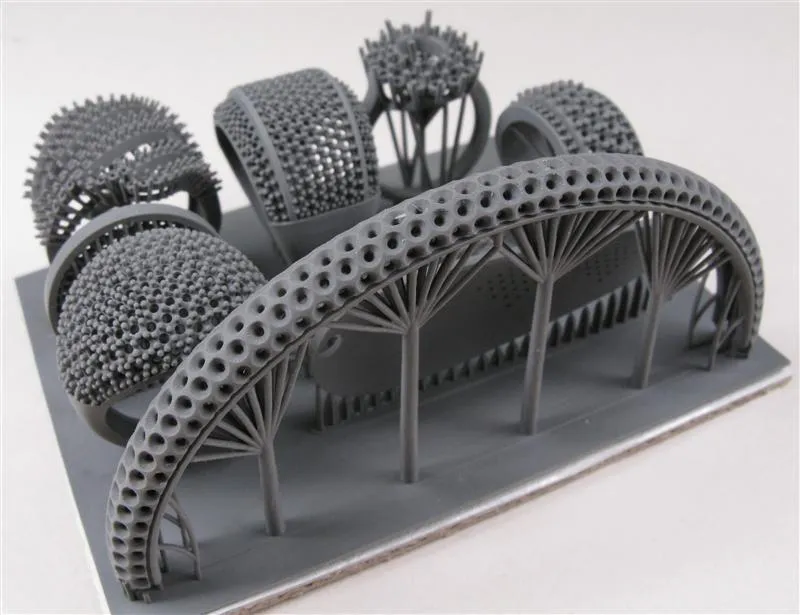
Standard Resins
- Properties: Balanced between strength and flexibility, standard resins are the go-to for general-purpose printing.
- Applications: Ideal for prototyping, art, and educational models.
Castable Resins
- Properties: Burn out cleanly without residue, perfect for investment casting.
- Applications: Widely used in jewelry making and dental industry for creating molds.
Flexible Resins
- Properties: Mimic the flexibility of rubber, with varying degrees of stiffness.
- Applications: Used for printing parts that require bending or compression, such as seals or gaskets.
Tough and Durable Resins
- Properties: Simulate the strength and stiffness of ABS plastic.
- Applications: Suitable for functional parts that require high impact resistance.
Water Washable Resins
- Properties: Easily cleaned with water, eliminating the need for chemical solvents.
- Applications: Convenient for educational settings and rapid prototyping.
Biocompatible Resins
- Properties: Safe for human contact, meeting medical industry standards.
- Applications: Essential for dental applications, hearing aids, and other medical devices.
Applications of DLP 3D Printing
DLP 3D printing has found its way into a vast array of industries, each harnessing the technology’s precision and efficiency for their unique needs.
Jewelry and Dentistry
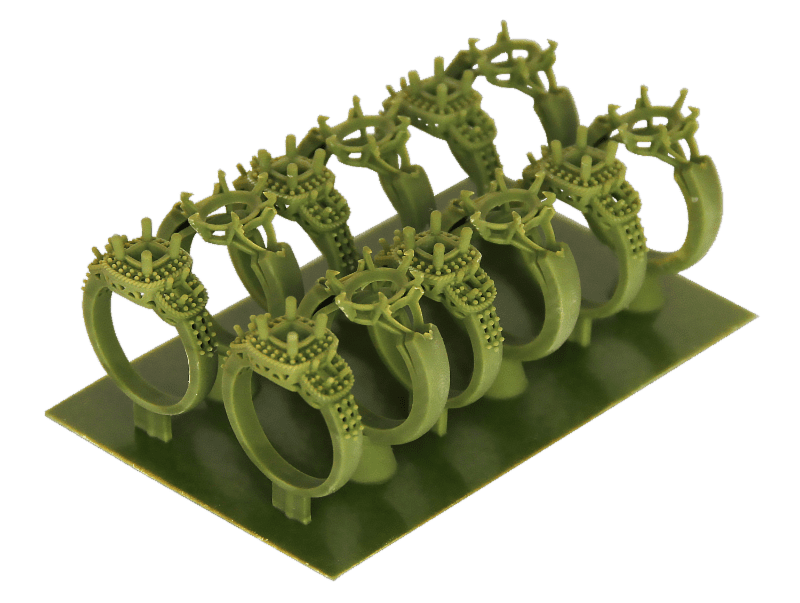
- Precision: Allows for intricate designs and fits that are essential in custom jewelry and dental appliances.
- Speed: Rapid prototyping speeds up the design process and production.
Prototyping and Manufacturing
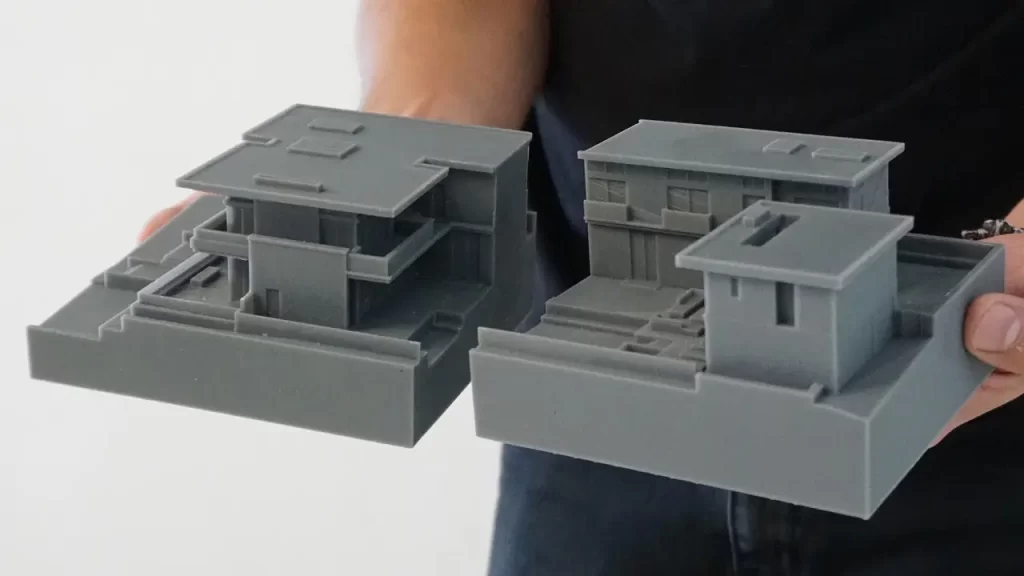
- Cost-Effective: Reduces the time and material costs associated with traditional prototyping.
- Customization: Enables the creation of parts tailored to specific requirements without additional costs.
Medical Industry
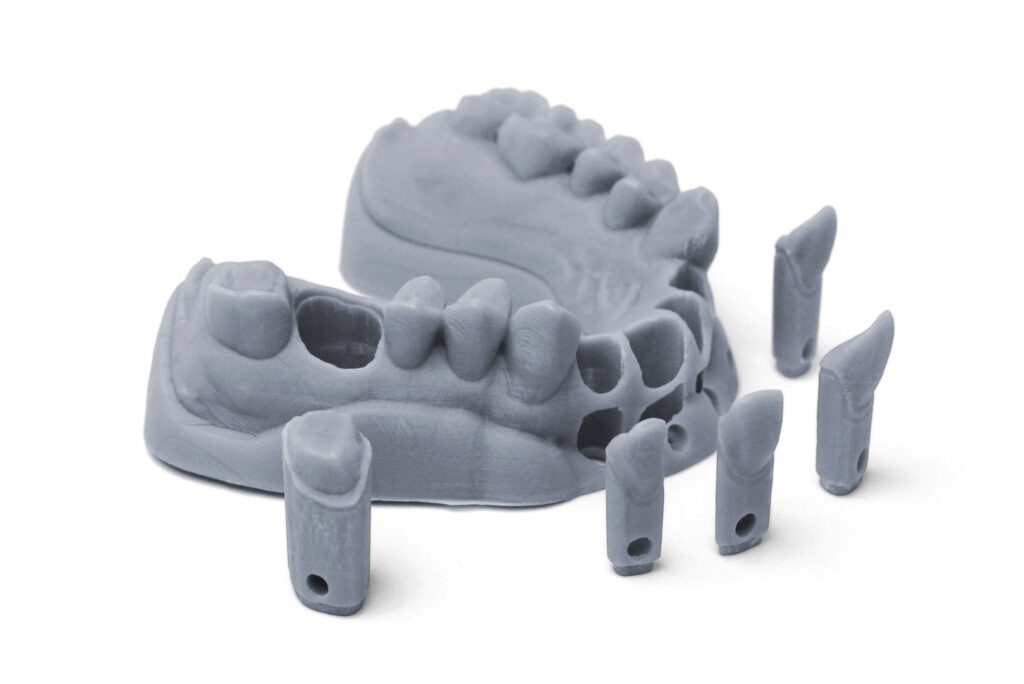
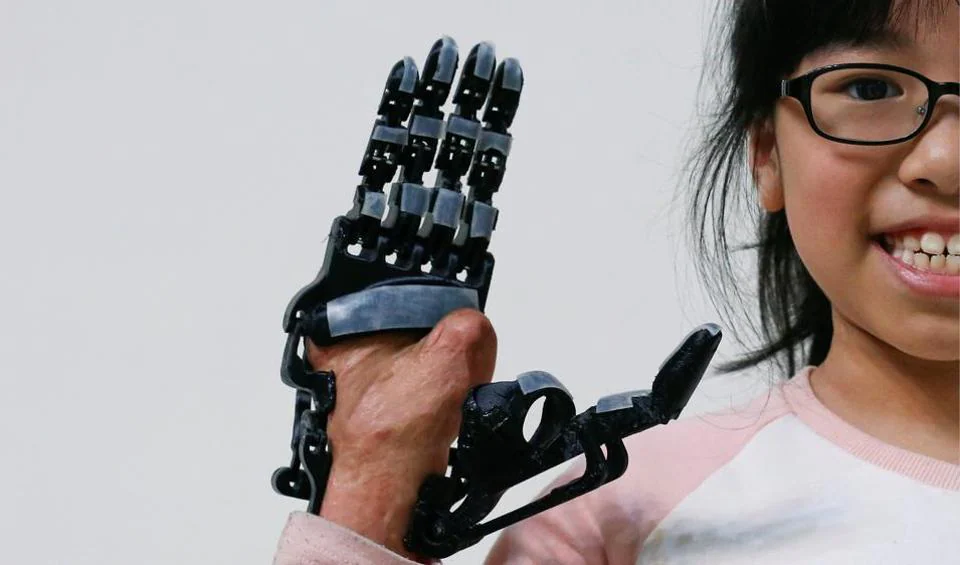
- Custom Implants: Produces patient-specific implants and surgical guides.
- Prosthetics: Allows for the creation of personalized prosthetics with a comfortable fit.
Education and Research
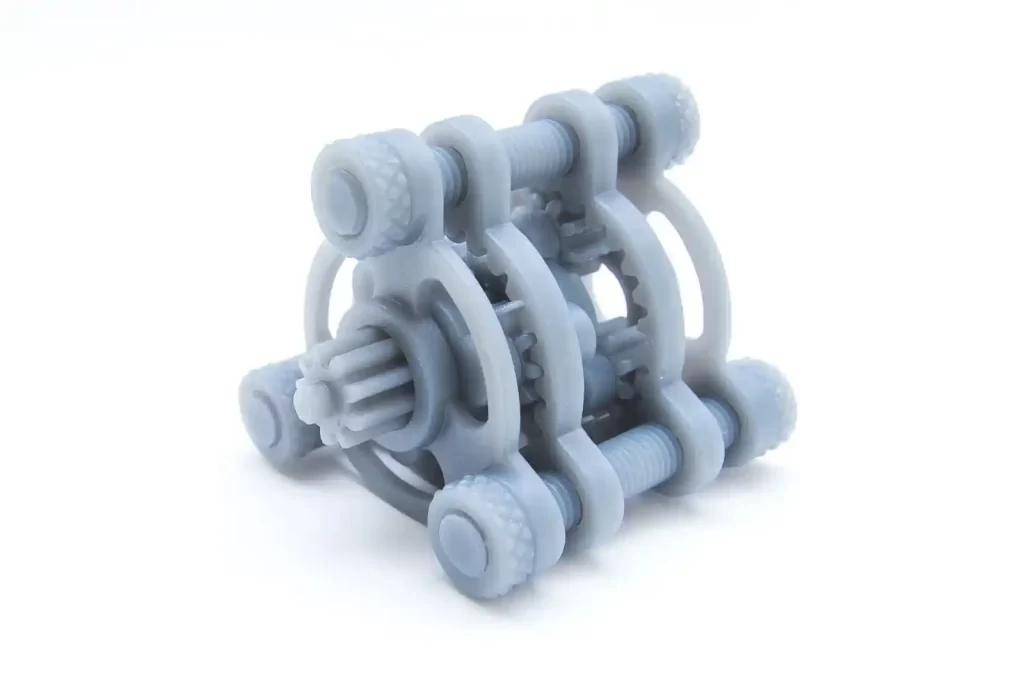
- Learning Tool: Assists in teaching complex concepts through tangible models.
- Research: Facilitates the development of new materials and printing techniques.
Hobbyist Projects
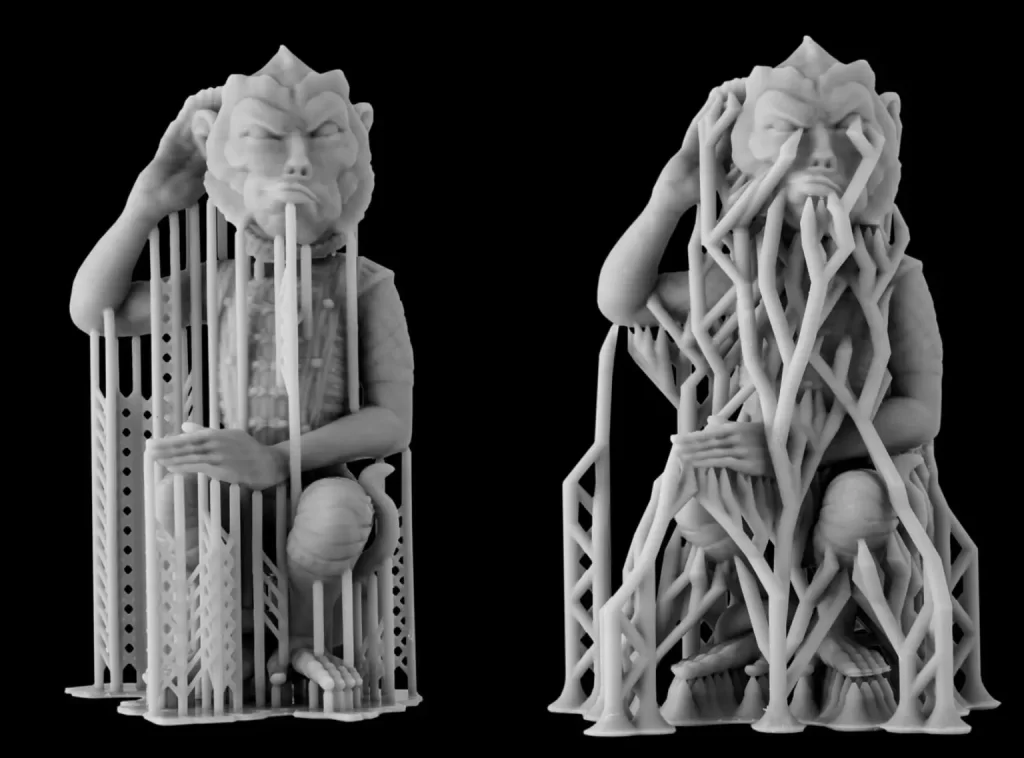
- Accessibility: Affordable desktop DLP printers have opened up possibilities for hobbyists.
- Community: A growing community of enthusiasts shares designs and techniques.
Choosing the Right Resin
Selecting the appropriate resin for your project is crucial. Here are some factors to consider:
- Mechanical Properties: Consider the strength, flexibility, and durability needed.
- Surface Finish: Some resins offer smoother finishes than others.
- Post-Processing: Think about the ease of support removal and additional curing.
Advantages and Limitations of DLP 3D Printing
When considering any technology, it’s crucial to weigh its strengths against its potential drawbacks. DLP 3D printing, with its unique capabilities, is no exception. In this section, we’ll dissect the advantages that make DLP a game-changer in the 3D printing arena, as well as the limitations that users and manufacturers need to navigate.
Advantages of DLP 3D Printing
DLP 3D printing technology boasts several features that make it a preferred choice for a wide range of applications:
High Resolution and Detail
- Precision: DLP can produce parts with extremely fine details, making it ideal for intricate designs.
- Surface Finish: Objects printed with DLP often have smooth surfaces, reducing the need for post-processing.
Speed
- Layer Curing: Unlike SLA that cures one point at a time, DLP cures a whole layer simultaneously, significantly speeding up the printing process.
- Turnaround Time: Fast printing capabilities mean shorter lead times from design to finished product.
Efficiency
- Material Usage: DLP printers only use the amount of resin necessary for the part, minimizing waste.
- Energy Consumption: The light source is only active during the actual curing process, which can be more energy-efficient.
Versatility
- Range of Materials: A wide variety of resins are available, allowing for different mechanical properties and applications.
- Scalability: DLP printers can be as small as a desktop machine or as large as industrial-sized equipment.
Limitations of DLP 3D Printing
Despite its many advantages, DLP 3D printing also comes with its own set of limitations:
Size Constraints
- Build Volume: DLP printers typically have a smaller build volume compared to other 3D printing methods, which can limit the size of parts that can be produced.
- Large Parts: Printing large parts may require them to be divided and assembled post-printing.
Material Limitations
- Resin Diversity: While there is a variety of resins available, the range is still more limited compared to materials available for other types of 3D printing like FDM.
- Durability: Some resins may not be as durable as traditional manufacturing materials, affecting the longevity of parts.
Post-Processing
- Cleaning: Printed parts often require cleaning to remove uncured resin, which can be a messy and time-consuming process.
- Curing: Additional UV curing may be needed to achieve the final material properties.
Operating Costs
- Resin Costs: High-quality resins can be expensive, which may impact the cost-effectiveness of DLP printing for certain projects.
- Maintenance: Regular maintenance and replacement of the light source can add to operating costs.
Future Developments and Trends in DLP 3D Printing
The landscape of 3D printing is ever-evolving, with DLP technology at the forefront of innovation. As we look to the future, it’s important to understand the potential advancements and trends that could shape the capabilities and applications of DLP 3D printing. This section will explore the emerging developments and predict how they might transform the industry.
Emerging Developments in DLP 3D Printing
The relentless pursuit of improvement in DLP 3D printing technology has led to several exciting developments:
Advanced Resins
- Bio-based Resins: Research into sustainable, bio-derived resins could reduce the environmental impact of 3D printing.
- High-Performance Resins: New formulations are being developed to enhance properties like temperature resistance and strength.
Improved Light Sources
- LED Innovations: Advances in LED technology could lead to more efficient and longer-lasting light sources for DLP printers.
- Laser Integration: Combining DLP with lasers might offer even finer detail and speed in the curing process.
AI and Machine Learning
- Predictive Analytics: AI could be used to predict and adjust printing parameters for optimal results.
- Quality Control: Machine learning algorithms might monitor prints in real-time to identify and correct issues.
Larger Build Volumes
- Scaling Up: Efforts to increase the build volume of DLP printers can open up possibilities for larger parts and new applications.
- Modular Designs: Printers with modular build areas could allow for customizable print sizes without compromising resolution.
Trends Influencing DLP 3D Printing
Several trends are currently influencing the direction of DLP 3D printing:
Customization
- Mass Customization: There is a growing demand for personalized products, and DLP’s precision makes it ideal for custom manufacturing.
- Healthcare Applications: Custom medical devices, implants, and prosthetics are becoming more prevalent, with DLP offering the necessary detail and material safety.
Automation
- Integrated Systems: The integration of DLP printers into automated production lines can streamline manufacturing processes.
- Smart Factories: As part of the Industry 4.0 movement, DLP 3D printing is becoming more interconnected with other digital manufacturing technologies.
Education and Collaboration
- Academic Research: Increased use in academic settings is driving research into new materials and processes.
- Open Source: A trend towards open-source hardware and software could accelerate innovation and reduce costs.
Sustainability
- Recyclable Materials: There’s a push for more environmentally friendly materials that can be recycled or are biodegradable.
- Energy Efficiency: As sustainability becomes a priority, the energy efficiency of DLP printing is a significant advantage.
Conclusion
The future of DLP 3D printing is bright and brimming with potential. With advancements in materials, light sources, and the integration of AI, the technology is set to become even more precise, efficient, and versatile. Trends like customization, automation, and sustainability are guiding the technology towards new industries and applications, making DLP 3D printing a key player in the next industrial revolution. As we continue to innovate and adapt, the possibilities of what can be created with DLP 3D printing are only bound by the limits of our imagination.