3D printing, an invention that seemed like science fiction only a few decades ago, is transforming how we create everything from toys to car parts to human organs. Today, we live in a world where if you can design it, you can print it — and in an astonishing array of materials. Two of the front runners in this technological revolution are Fused Deposition Modeling (FDM) and Selective Laser Sintering (SLS).
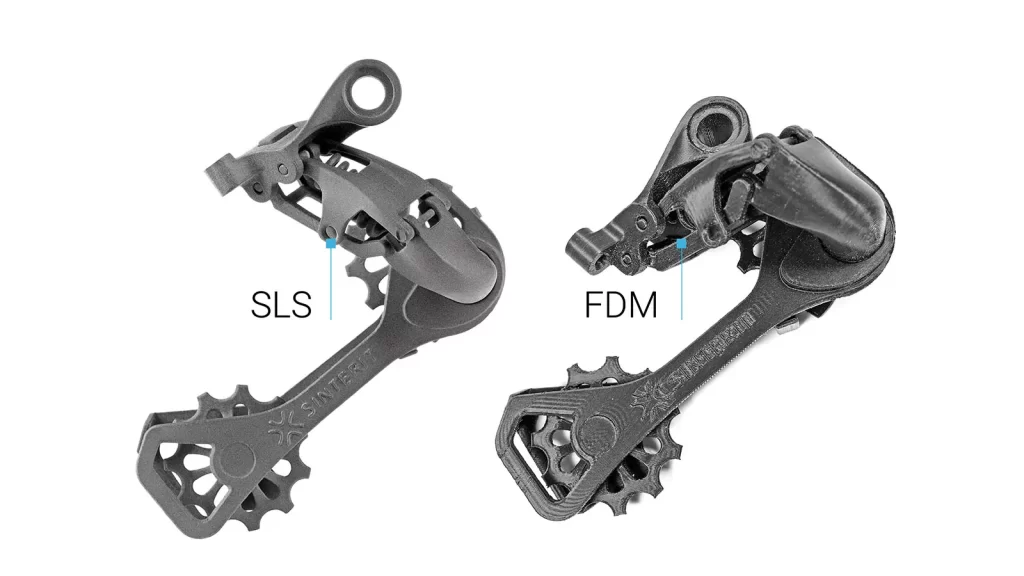
Through this article, we intend to elucidate FDM and SLS – the technologies, the processes, and their applications. We will embark on a comparative journey examining various factors like cost, materials, print quality, speed, and ease of use. The purpose? To provide you with a comprehensive understanding, enabling informed decisions for your future 3D printing projects. So whether you’re an enthusiast just starting or a professional seeking an in-depth comparative study, this post will be your engaging guide.
Understanding 3D Printing
As we stand on the threshold of the fourth industrial revolution, 3D printing, also known as additive manufacturing, has become a significant pillar of this transformative change. If you’ve ever designed a 3D model and watched it take form through a 3D printer, you understand the sense of innovation this technology fosters. But, to appreciate it fully, we should delve a little bit deeper into the essence and magnitude of 3D printing.
The Birth of 3D Printing
3D printing’s roots trace back to 1980s when Chuck Hull invented a process called “stereolithography.” This revolution sprung from a simple idea — transforming a digital file into a physical, three-dimensional object by adding material layer by layer, hence the term ‘additive manufacturing.’ Seems quite straightforward, right? But this seemingly straightforward concept transformed the face of design, modeling, and manufacturing!
The Power of 3D Printing
The ‘3D’ in 3D printing means that it creates objects in three dimensions, unlike the 2D (flat) printing we’re accustomed to. Below are the significant aspects that highlight the power of 3D printing:
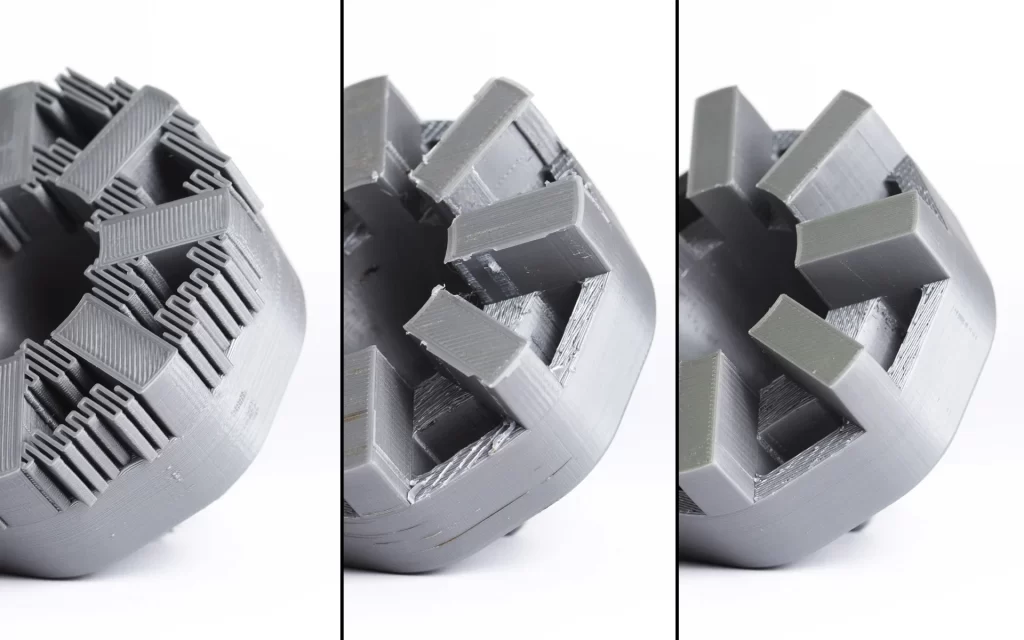
- Freedom of Design: 3D printing allows for an unprecedented level of design freedom. You can create complex geometry, structures that have been considered unachievable through traditional manufacturing techniques.
- Customizability: Every single print can be tailored to specific requirements. This feature is powerful, especially in fields like dentistry, where personalized prints are vital.
- Speed: 3D printing, often referred to as Rapid Prototyping, allows for the quick generation of models, significantly reducing the time from idea to physical product.
- Cost-Effective Prototyping: For small volume production, 3D printing can be cost-effective. The ability to print prototypes on demand allows for quicker design iterations and reduced development costs.
- Sustainability: By adding layer upon layer, 3D printing uses only the material needed for the part itself and minimal support structures, significantly reducing waste.
Applications: The Sky’s the Limit!
From automotive and aerospace to healthcare and fashion, 3D printing is finding relevance in various industries. In healthcare, 3D printing prosthetics tailor-made for the patient’s comfort are changing lives. In the automotive industry, companies print car parts for testing during the design process. Architects now print 3D models of their designs, providing clients with a tangible vision of the final product. Even in the culinary world, 3D printed confectioneries and intricate cake designs are transforming food art.
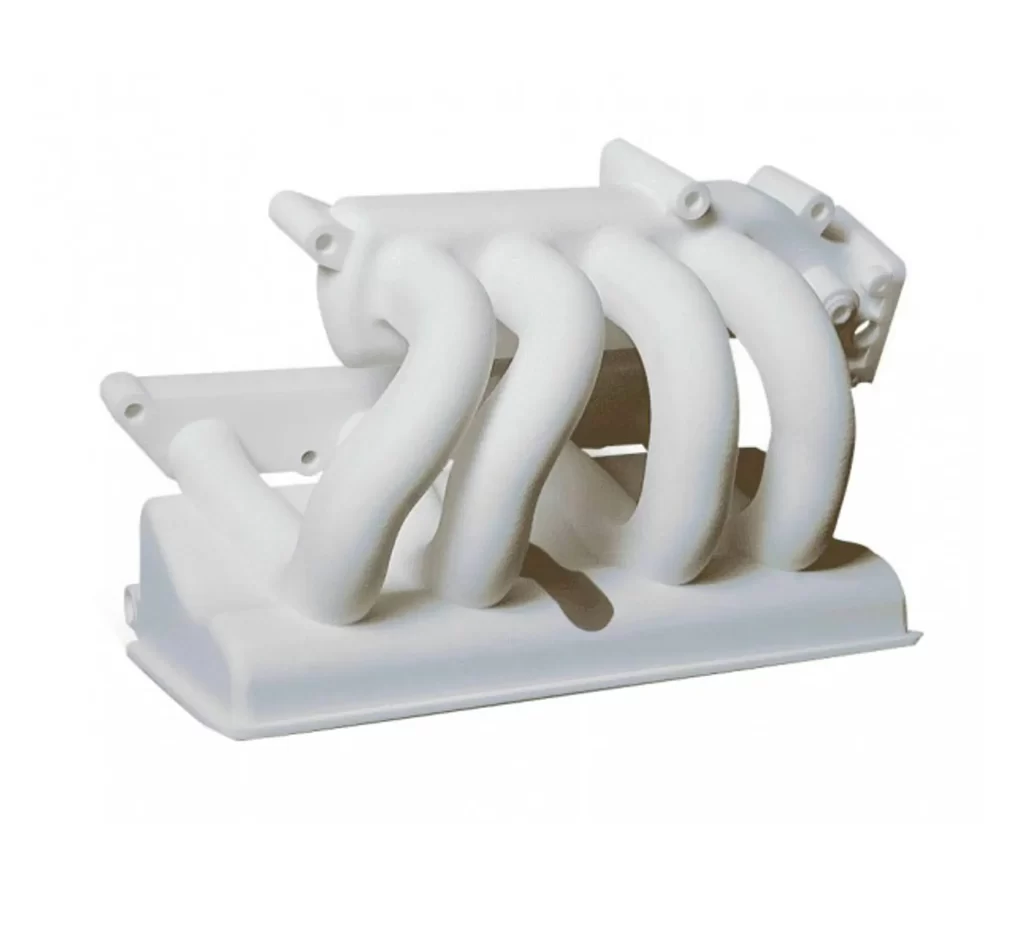
As we continue exploring the distinct aspects of FDM and SLS, remember, no one-size-fits-all solution in 3D printing. Through this comparative analysis, our aim is to provide you with a comprehensive understanding that enables you to select the technology best suited for your needs.
Exploring FDM 3D Printing
Stepping away from traditional manufacturing practices, we’re now entering a world that was, for the longest time, considered the stuff of science fiction. Buckle up because it is time to dive into the nuances of Fused Deposition Modeling (FDM), one of the most common and widely accessible forms of 3D printing available today.
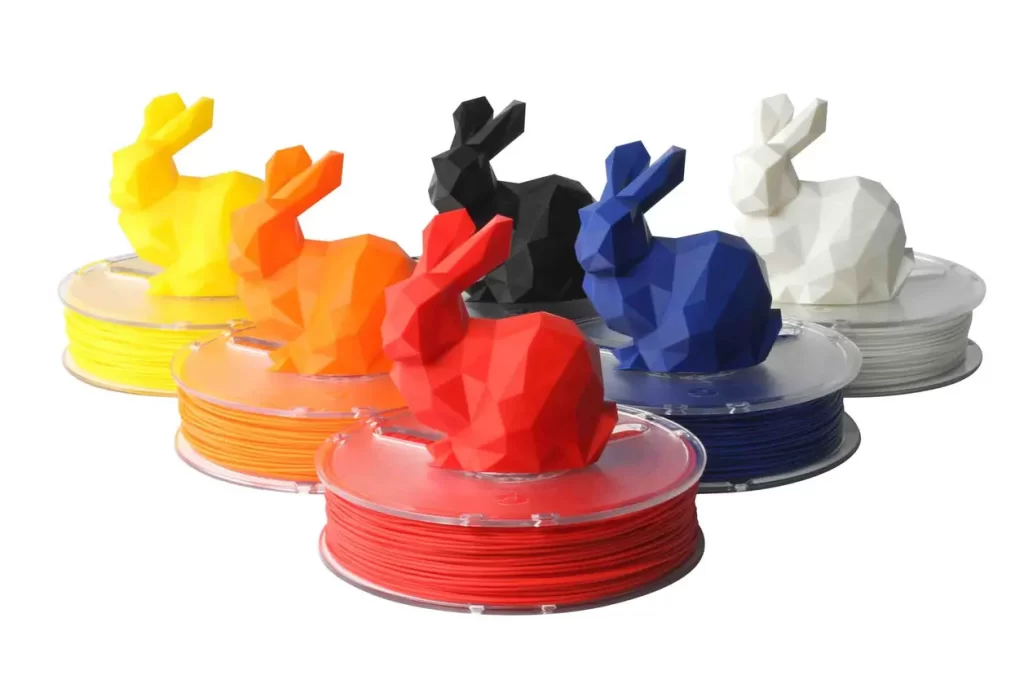
What is FDM?
FDM, or Fused Deposition Modeling, is a filament-based technology where a temperature-controlled head extrudes thermoplastic material. FDM printers use a thermoplastic filament, which is heated to its melting point and then extruded, layer by layer, to create a three-dimensional object.
The FDM process involves following key steps:
- Pre-processing: 3D designs are created and converted to the Universal 3D File format (“.stl”) to ensure compatibility with the FDM software.
- Production: The machine heats the thermoplastic filament to a semi-liquid state. The printhead then deposits the material layer by layer on the build platform, following the path designated in the design.
- Post-processing: Once the part is printed, it may undergo additional operations such as support removal, sanding, painting, or other finishing touch-ups.
Pros and Cons of FDM
While FDM has undoubtedly revolutionized the 3D printing sphere, it’s important to point out its advantages and disadvantages to understand its potential and limitations:
Advantages:
Affordability: FDM printers are typically more cost-effective compared to other 3D printers, which makes them highly attractive for beginners and small businesses.
Material Diversity: FDM can handle a wide range of thermoplastic materials, including ABS, PLA, PETG, and nylon, to name a few.
Ease of Use: The simplicity of the technology and the availability of desktop printers make FDM user-friendly and suitable for educational purposes.
Disadvantages:
Surface Finish: FDM parts may show visible layer lines, and post-processing may be needed in applications where smooth surfaces are crucial.
Dimensional Accuracy: While FDM is adequate for many applications, it may not achieve the precision required for highly detailed parts.
FDM Applications
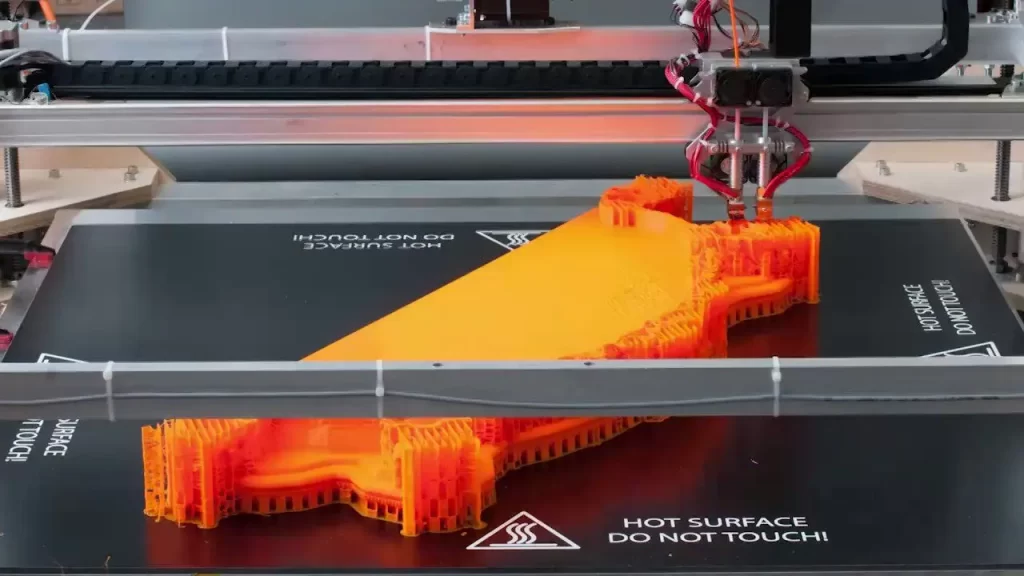
FDM finds its applications in a variety of scenarios thanks to its versatility. Here are a few examples:
Prototyping: The affordable nature of FDM makes it a popular choice for creating prototypes quickly and cost-effectively
Education: Due to its ease of use and safety, FDM is ideal for use in schools and educational institutes to teach students about 3D printing
Custom Components: FDM’s capability with durable materials makes it suitable for producing custom tools, fixtures, and end-use parts
Understanding FDM 3D printing brings us one step closer to a comprehensive comparison with SLS, allowing us to better determine the most suitable technology for our specific needs. Be it the decision based on cost-effectiveness, finish, diversity of materials, or ease of use, every aspect counts. So let’s proceed to the next chapter, where we continue our journey to examine Selective Laser Sintering (SLS)!
Selective Laser Sintering: A Deep Dive
Now that we’ve ventured into the fascinating world of Fused Deposition Modeling, it’s time to explore the other contender in our comparative journey – Selective Laser Sintering (SLS). SLS, like FDM, has a significant position in the world of 3D printing, but the science behind it and its applications are quite unique.
What is SLS?
Selective Laser Sintering is a 3D printing technique that uses a high power laser to fuse powdered material into a solid structure. Unlike FDM, which builds layer-by-layer from the bottom up, SLS starts with a bed of powdered material and the laser selectively sinters, or fuses, the powder into the shape defined by the digital 3D design.
The SLS process involves key steps like:
Pre-processing: Prepare 3D designs and convert to .stl file similar to FDM process.
Production: A thin layer of powder is spread across the building area and a laser selectively sinters portions based on the design. The process repeats layer by layer until the entire model is built.
Post-processing: The unsintered powder is removed revealing the finished part. Additional finishing steps may be applied depending on the application.
Pros and Cons of SLS
The SLS process carries its own set of benefits and drawbacks which are crucial to understand its value proposition:
Advantages:
Material Strength: SLS-printed parts are generally stronger and more durable than FDM counterparts. This makes SLS more suitable for functional parts.
Complexity is Not a Problem: SLS does not require support structures which makes it capable of printing very intricate geometries and moving parts in a single piece.
Surface Finish: SLS generally provides a better surface finish with no visible layer lines as seen in FDM-printed parts.
Disadvantages:
Higher Costs: SLS machines and materials are generally more expensive than FDM. Therefore, cost could be a decisive factor.
Limited Material Colors: SLS is limited in terms of colors due to the nature of the powders used.
Applications
Though more expensive, SLS has important uses in fields that require durability and complexity of design. Here are some examples:
Functional Prototypes: For high-stress tests and final-stage prototypes, SLS is preferred because of its strength and durability.
Manufacturing Aids: SLS can produce durable tooling and fixtures to streamline manufacturing processes.
Custom Products: With the ability to produce complex, customized designs, SLS provides great benefits to industries like healthcare, automotive, and aerospace.
While the battle of FDM vs. SLS might not have a definitive victor due to their individual strengths and applications, we hope this deep-dive has provided you with the knowledge to select a winner for your specific needs. Remember, in 3D printing and in life, it’s all about finding the right tool for the job!
Conclusion: FDM vs SLS
It’s been quite a journey, dipping our toes into the vast ocean that is 3D printing technology. Are you feeling a bit like a detective now, sifting through the myriad of clues these techniques provide? I sure do! So, let us bring together the insights we gained to draw our conclusions about Fused Deposition Modeling (FDM) and Selective Laser Sintering (SLS).
Key Differences
Both FDM and SLS offer unique benefits and setbacks. Whether one technique trumps the other depends entirely on the specific needs of your project.
Here are some key distinguishing factors:
Material Cost: FDM typically uses cheaper materials than SLS, making it a more cost-effective choice for those on a budget. For businesses, this could mean cheaper parts, prototypes, and products, attracting a wider audience.
Material Choices: Although FDM offers a good range of materials, SLS takes it a notch higher, handling everything from nylon to glass-filled polyamide, providing excellent durability and heat resistance.
Resolution and Finish: There’s no real competition in this aspect. SLS takes the cake with its ability to produce high-resolution parts with a smoother finish. This makes SLS more optimal for applications requiring precise detailing and surface quality.
Complexity: SLS does not require support structures, opening up a world of possibilities for complex designs and geometrical shapes that FDM can’t offer.
Production Time: Though it varies from part to part, SLS generally has a longer production time, attributed to its extensive cooling and post-processing requirements.
In conclusion, choosing between FDM and SLS is all about understanding your specific needs.