Understanding SLS 3D Printing Technology
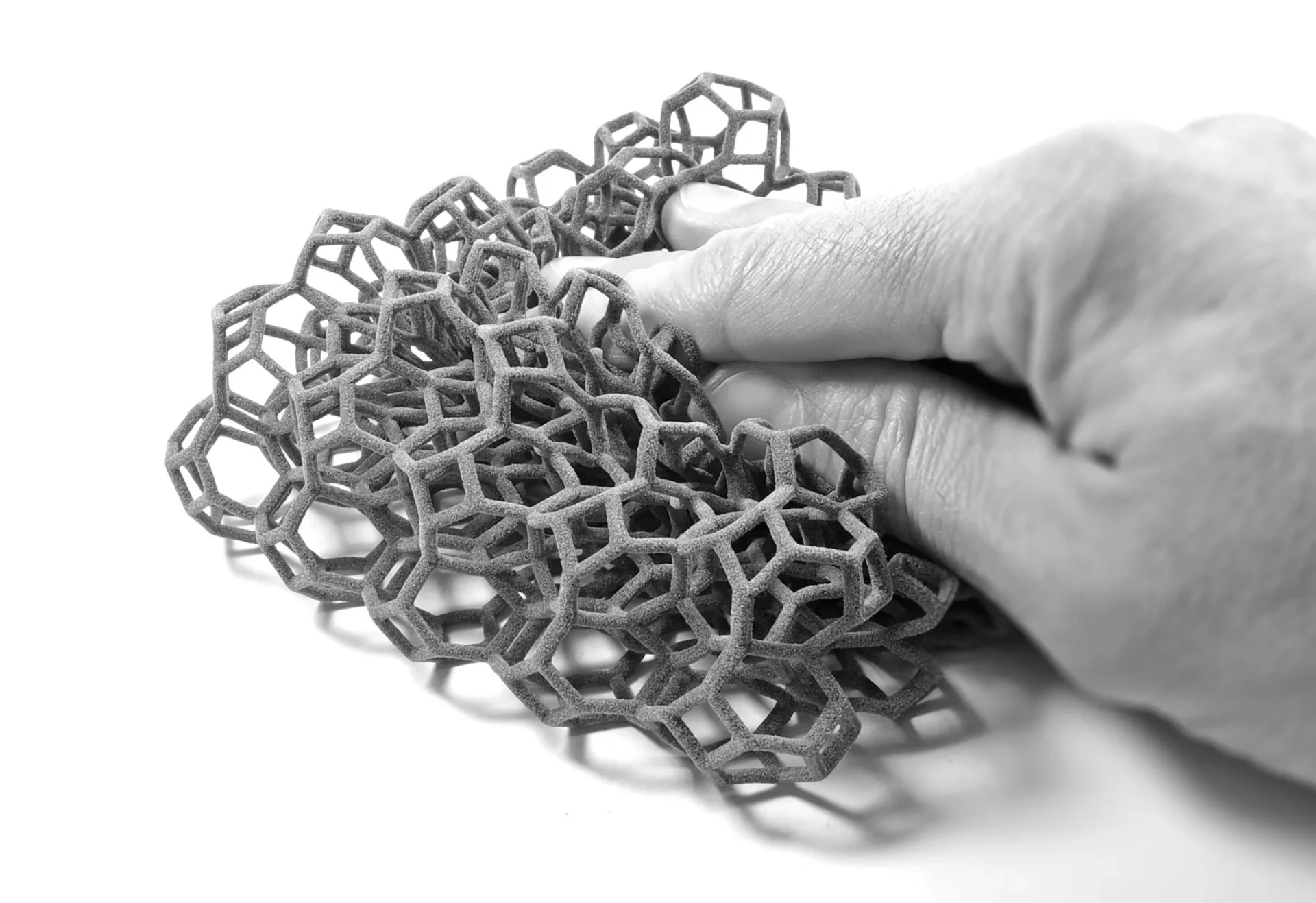
Selective Laser Sintering (SLS) is a key innovation in additive manufacturing. This technology uses powdered materials, which are selectively fused by a high-powered laser according to a digital model. The resulting layer-by-layer fabrication enables the production of complex geometries unattainable through traditional methods.
Fundamentals of SLS Technology
SLS operates using three core stages:
- Layer-by-Layer Construction: A thin layer of powder is spread across the build platform. The platform lowers after each layer, allowing for successive additions until the part is complete.
- Laser-Powder Interaction: The laser sinters only the designated regions of the powder bed, enabling precise internal structures and intricate external designs.
- Post-Processing: Excess powder is removed manually or via automated systems. Additional treatments, such as heat exposure or surface finishing, may be applied to enhance mechanical properties.
This process eliminates many constraints of subtractive manufacturing, offering greater design flexibility and material efficiency.
Materials Used in SLS
SLS supports a diverse range of powders, including:
- Thermoplastics: Nylon (Polyamide), Thermoplastic Polyurethane (TPU)
- Composite Powders: Reinforced with carbon fibers or glass beads for improved strength
- Emerging Materials: Metal and ceramic powders for specialized applications
Material selection directly influences mechanical performance, environmental resistance, and cost-effectiveness.
Advantages and Limitations of SLS
Advantages | Limitations |
---|---|
Design freedom for complex geometries | Post-processing requirements |
Material efficiency with recyclable powder | High initial equipment costs |
Rapid prototyping capabilities | Dimensional accuracy limitations |
Reduced lead times | Surface roughness requiring refinement |
Customization potential | Scalability challenges for mass production |
While SLS offers significant benefits, its limitations necessitate strategic implementation based on production volume, complexity, and budget considerations.
How SLS 3D Printing Impacts Industries
Transforming Design and Production
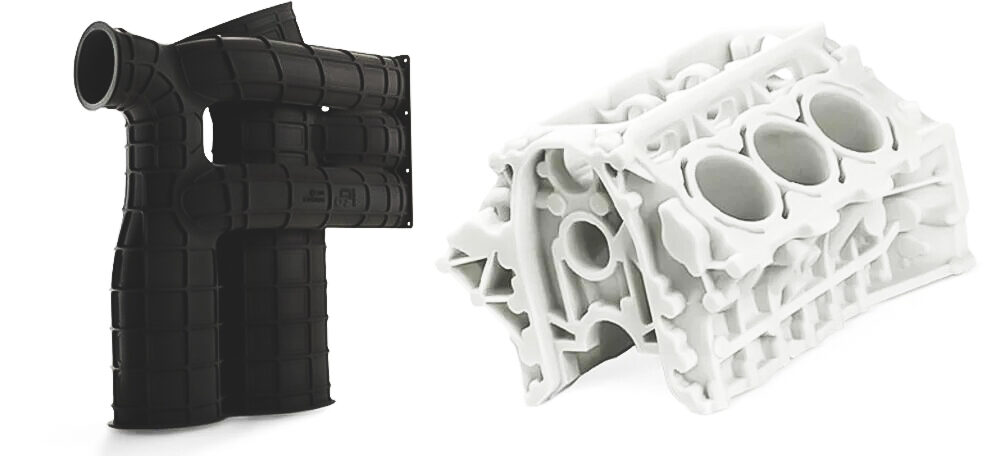
SLS enables the creation of previously impossible geometries, such as lattice structures and integrated channels. These features support lightweighting and functional integration in aerospace, automotive, and medical fields. Rapid prototyping accelerates product development cycles, reducing time-to-market. On-demand manufacturing further enhances agility by minimizing inventory costs.
Economic Impact and Cost Efficiency
SLS reduces reliance on expensive tooling, leading to lower upfront investment. Material reuse improves sustainability and economic viability. Faster iteration cycles also reduce R&D expenditures.
Cost Factor | Impact |
---|---|
Tooling Reduction | Eliminates mold costs |
Material Reuse | Reduces waste and procurement expenses |
Time-to-Market Speed | Accelerates revenue generation |
Enhancing Sustainability
SLS contributes to sustainable manufacturing through:
- Minimal material waste due to additive layering
- Energy-efficient operations in modern systems
- Localized production that lowers transportation emissions
By supporting circular economy principles, SLS aligns with global sustainability goals.
Operational Advantages Across Industries
SLS facilitates customization, lean inventory models, and supply chain simplification. It allows for multi-functional part integration, reducing assembly steps and improving reliability.
Operational Benefit | Industry Application |
---|---|
Mass Customization | Healthcare implants, consumer goods |
Inventory Reduction | Aerospace spare parts, industrial components |
Supply Chain Optimization | Automotive tooling, rapid prototyping |
Industry-Specific Applications and Case Studies
1. Aerospace and Aviation
Applications: Lightweight structural components, internal cooling channels, on-demand spares
Case Study – Engine Component Fabrication
An aerospace firm utilized SLS to produce turbine blades with integrated cooling ducts. Traditional machining could not achieve these internal features, while casting introduced excessive weight. The optimized design improved thermal management and overall engine efficiency.
Key Insight: SLS enables lightweight, functionally integrated aerospace components that enhance fuel efficiency and performance.
2. Automotive Industry
Applications: Prototyping chassis parts, custom interior trim, tooling fixtures
Case Study – Prototype Chassis Components
A supplier reduced design cycle times by 50% using SLS for chassis prototypes. Rapid iterations enabled early-stage testing under real-world conditions, accelerating final validation.
Benefits Summary:
- Faster innovation cycles
- Cost-effective tooling alternatives
- Enhanced consumer customization
3. Healthcare and Medical Devices
Applications: Patient-specific implants, surgical guides, orthotics
Case Study – Custom Hip Implants
A medical device company used SLS to fabricate hip implants tailored to individual CT scans. The personalized approach improved postoperative recovery and implant longevity.
Comparative Advantage: SLS provides superior fit and biomechanical compatibility compared to standard implants.
4. Consumer Goods and Retail
Applications: Custom eyewear, limited-edition fashion items, home decor
Case Study – On-Demand Eyewear Frames
A brand employed SLS to offer customizable eyewear frames. Customers selected from multiple designs or submitted personal preferences for bespoke production. This model increased customer satisfaction and brand loyalty.
Highlights:
- Customer-centric production
- Lean inventory strategies
- Fast market response
5. Industrial Manufacturing and Tooling
Applications: Replacement molds, optimized fixtures, functional prototypes
Case Study – Mold Component Replacement
An industrial manufacturer replaced obsolete mold inserts using SLS. The new components restored machine functionality without requiring full mold replacement, saving time and cost.
Essential Insight: SLS provides agile solutions for legacy system maintenance and production optimization.
6. Research and Development
Applications: Experimental design validation, interdisciplinary collaboration, accelerated prototyping
Case Study – Academic Research Projects
Universities integrated SLS into their labs to test novel composite materials and geometric configurations. Several patented innovations emerged from these studies.
Summary Benefits:
- Low-cost experimentation
- Rapid design iteration
- Cross-disciplinary innovation
In-Depth Analysis of SLS 3D Printing Impact
Comparative Analysis: SLS vs. Traditional Manufacturing & Other 3D Printing Methods
Comparison | SLS Advantage |
---|---|
Design Complexity | Supports internal structures and lattices |
Material Usage Efficiency | Minimal waste; reusable powder |
Lead Time Reduction | No tooling required |
Detail Precision (vs. FDM) | Higher resolution and finer geometry |
Mechanical Strength (vs. SLA) | Superior durability for end-use parts |
Performance Metrics and Quality Benchmarks
Metric | Evaluation |
---|---|
Dimensional Accuracy | ±0.3% with typical tolerances of 0.1–0.3 mm |
Surface Finish | Textured finish; post-processing options available |
Mechanical Properties | High tensile strength and impact resistance |
Repeatability | Consistent results with calibrated systems |
Scalability and Integration Challenges
Challenge | Solution Strategy |
---|---|
Limited Build Volume | Select larger-format SLS machines |
Layer-by-Layer Speed | Optimize scan paths and laser parameters |
Post-Processing Complexity | Implement semi-automated cleaning systems |
Operator Training Requirements | Develop standardized training programs |
Future Trends and Emerging Technologies in SLS
Cutting-Edge Research and Development
Ongoing research focuses on:
- Advanced Lasers: Higher power efficiency and precision
- Hybrid Materials: Polymer-metal composites for enhanced performance
- AI-Driven Process Control: Real-time monitoring and adaptive adjustments
Integration with Digital Technologies
Digital transformation is reshaping SLS through:
- Digital Twin Modeling: Simulating print processes before execution
- Cloud-Based Analytics: Aggregating data across global installations
- IoT Connectivity: Enabling remote diagnostics and parameter tuning
- Augmented Reality Support: Guided maintenance and troubleshooting
Market Forecast and Emerging Industries
SLS adoption is growing in:
- Aerospace: Lightweight structural components
- Healthcare: Biocompatible implants and prosthetics
- Consumer Electronics: Custom wearable device housings
- Sustainable Manufacturing: Recyclable material systems
Strategic Recommendations
To maximize ROI and stay competitive:
- Invest in IoT-enabled SLS systems for real-time monitoring
- Partner with academic institutions for material innovation
- Pilot projects to validate scalability before full deployment
- Emphasize sustainability in marketing and ESG reporting
Conclusion
Selective Laser Sintering has redefined manufacturing possibilities across industries. From aerospace to healthcare, SLS enables unprecedented design freedom, cost efficiency, and sustainability. As digital integration deepens and material science advances, SLS will continue to expand into new domains. Companies embracing this technology strategically will gain a long-term competitive advantage in an evolving industrial landscape.