The Selective Laser Sintering (SLS) 3D printing market is in a phase of dynamic growth and revolutionary innovation. As a fundamental part of the broader additive manufacturing industry, SLS technology empowers businesses across diverse sectors to reimagine product design, speed up prototyping, and optimize manufacturing processes. We are witnessing an expanding range of applications, driven by continuous progress in materials science, printer technology, and software solutions, all contributing to a robust market trajectory. Understanding the complex trends shaping this industry is crucial for stakeholders aiming to maintain a competitive edge and capitalize on emerging opportunities.
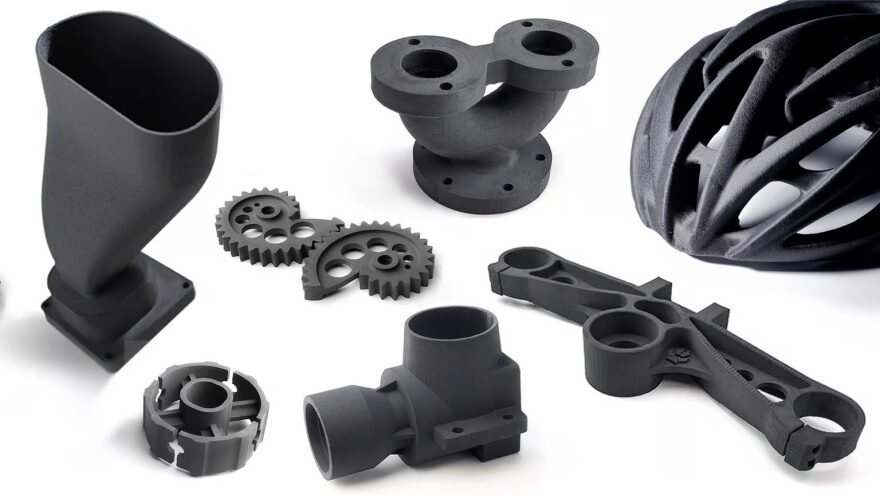
Market Size and Growth Projections
The global SLS 3D printer market has shown significant growth potential. In 2023, it was valued at USD 1.353 billion, and is projected to reach USD 2.8118 billion by 2032, with a compound annual growth rate (CAGR) of 8.5% during the forecast period. Another forecast anticipates the SLS market size to be USD 4.81 billion in 2025, growing to USD 13.25 billion by 2030, at a CAGR of 22.46%. A separate analysis projects the SLS equipment market to be valued at USD 1.0761 billion in 2025 and reach USD 5.7281 billion by 2035, with a CAGR of 18.2%.
These figures highlight the substantial and sustained growth expected within the SLS sector. The overall 3D printing market, of which SLS is an essential part, is also on a strong upward trend. It is estimated to grow from USD 17.5 billion in 2024 to USD 37.4 billion by 2029, at a CAGR of 16.4%. This broader market expansion provides a favorable environment for the specialized growth of SLS technology. The following table summarizes the market size projections for different periods:
Market Segment | 2023 Value | 2025 Projection | 2029 Projection | 2030 Projection | 2032 Projection | 2035 Projection | CAGR (Relevant Period) |
---|---|---|---|---|---|---|---|
SLS 3D Printer Market | USD 1.353 billion | – | – | – | USD 2.8118 billion | – | 8.5% (2023 – 2032) |
SLS Market (Another Projection) | – | USD 4.81 billion | – | USD 13.25 billion | – | – | 22.46% (2025 – 2030) |
SLS Equipment Market | – | USD 1.0761 billion | – | – | – | USD 5.7281 billion | 18.2% (2025 – 2035) |
Overall 3D Printing Market | – | – | USD 37.4 billion | – | – | – | 16.4% (2024 – 2029) |
Key Market Drivers Propelling SLS Adoption
Several powerful factors are fueling the accelerating adoption of SLS 3D printing technology.
Customization Capabilities
The ease of developing customized products is a primary driver. SLS technology excels at producing complex geometries and individualized designs, making it ideal for an era of mass personalization and on – demand manufacturing. This capability is particularly crucial in industries such as healthcare, for patient – specific medical devices, and consumer goods, for bespoke products. For instance, in healthcare, customized implants can be designed to fit a patient’s unique anatomy precisely, improving treatment outcomes.
Cost and Time Savings
The reduction in manufacturing costs and process downtime offered by SLS is a significant attraction for businesses. By streamlining prototyping and enabling the creation of functional end – use parts without the need for expensive tooling, SLS contributes to more agile and cost – effective production cycles. The ability to produce parts with joints, snap – fits, and living hinges directly is also a notable advantage. A comparison of traditional manufacturing and SLS in terms of prototyping cost and time is shown in the table below:
Manufacturing Method | Prototyping Cost (Estimated for a Medium – Complex Part) | Prototyping Time (Estimated for a Medium – Complex Part) |
---|---|---|
Traditional Manufacturing (Including Tooling) | USD 5000 – USD 10000 | 2 – 4 weeks |
SLS 3D Printing | USD 500 – USD 2000 | 1 – 3 days |
Government Support
Government investments in 3D printing projects globally are also playing a crucial role in fostering market growth. These initiatives often support research and development, infrastructure development, and the adoption of additive manufacturing technologies across various industries. For example, some governments provide grants to companies researching new materials for SLS 3D printing.
Material Diversity
The availability of a wide variety of industrial – grade 3D printing materials, especially advanced polymers and composites, is continually expanding the application scope of SLS. This includes materials with enhanced mechanical properties, thermal resistance, and chemical stability, catering to demanding industrial applications.
Complex Part Manufacturing
The capability for complex part manufacturing, particularly in sectors like aerospace and defense, is a strong driver. SLS allows for the creation of lightweight yet robust components with intricate internal structures, which are often impossible or prohibitively expensive to produce using traditional manufacturing methods.
Technological Advancements: The Engine of SLS Evolution
Continuous innovation in SLS technology is a critical trend, enhancing its capabilities, efficiency, and accessibility. These advancements span hardware, software, and materials.
Hardware Innovations
- Improved Laser Technology: There has been a significant shift from CO₂ lasers to more precise and energy – efficient fiber lasers. Fiber lasers offer a smaller spot size for finer detail, increased power density for faster sintering, and lower energy consumption, contributing to both quality and sustainability. Some modern SLS printers now feature lasers with power up to 400 watts.
- Multi – Laser Systems: The integration of multiple lasers working in parallel on the print bed significantly reduces build times, boosting productivity for high – volume production.
- Enhanced Thermal Control: Advanced temperature management systems are leading to more consistent part quality and a reduction in warping, a common challenge in powder bed fusion processes.
- Increased Build Volumes: Larger print chambers are becoming available, enabling the production of bigger parts or a greater number of components in a single print run, catering to industrial – scale manufacturing.
- Automated Powder Handling: Closed – loop powder circuits, intelligent sieving and mixing systems, and real – time powder quality monitoring are streamlining the workflow, minimizing operator exposure, ensuring material consistency, and reducing waste. These features are crucial for making SLS more suitable for high – volume production.
Software Enhancements
- AI and Machine Learning Integration: Artificial intelligence (AI) and machine learning (ML) are increasingly being employed to optimize the entire SLS process. This includes AI – powered design optimization (generative design and topology optimization) to maximize strength while minimizing material usage, print orientation optimization, real – time print parameter adjustments, predictive maintenance to reduce downtime, and automated quality control.
- Advanced Slicing Algorithms: Smart slicing algorithms optimize the build process, reducing material waste and minimizing print failures.
- Enhanced Simulation Tools: Sophisticated simulation software helps identify potential issues before printing, minimizing failures and optimizing build parameters.
Material Development
The portfolio of materials compatible with SLS is continually expanding, unlocking new applications.
- High – Performance Polymers: New and improved polymers such as PA6 (Polyamide 6), Polycarbonate (PC), PEEK (Polyether Ether Ketone), and PEKK (Polyetherketoneketone) offer enhanced mechanical properties, heat resistance, and chemical stability. Nylon remains a dominant material due to its strength, durability, and versatility.
- Composites: The development of composites, such as carbon fiber – reinforced or glass fiber – reinforced nylons, provides materials with superior strength – to – weight ratios, ideal for demanding applications in aerospace and automotive sectors.
- Flexible Materials: Materials like TPU (Thermoplastic Polyurethane) are enabling the production of flexible, wear – resistant parts.
- Sustainable Materials: There is a growing focus on developing more sustainable and recyclable powders, including bio – based resins and materials derived from waste sources, to reduce the environmental impact of SLS printing.
- Specialized Materials: This includes flame – retardant polymers, anti – static polymers, and biocompatible materials for medical applications.
Expanding Applications Across Key Industries
The versatility and advancing capabilities of SLS 3D printing are driving its adoption across a wide spectrum of industries.
Automotive
The automotive sector is a major user of SLS technology, commanding a significant market share. It is extensively used for manufacturing engine parts, prototype intake manifolds, and engine covers. The ability to produce heat – resistant and vibration – tolerant components, as well as customized parts and tooling, jigs, and fixtures, makes SLS invaluable for both prototyping and production.
Aerospace & Defense
This sector is a pioneer in adopting SLS for producing lightweight, complex parts, and increasingly for end – use components. The technology’s capacity to consolidate multiple parts into single, unified components reduces production time and costs while improving performance. Applications include ducting, brackets, drone components, and even rocket engine parts.
Healthcare & Medical Devices
SLS is revolutionizing the production of medical devices. Its ability to create patient – specific implants, surgical guides, prosthetics, and orthotics using biocompatible materials is transforming patient care. The technology allows for complex geometries and porous structures suitable for tissue engineering and personalized drug delivery systems.
Consumer Goods
SLS is facilitating mass customization in the consumer goods sector, enabling the production of personalized products like footwear, jewelry, and electronic device casings. For example, the French fashion brand Chanel used SLS to create a 3D – printed mascara brush.
Industrial Manufacturing & Tooling
SLS is increasingly used for creating tooling, jigs, fixtures, and other manufacturing aids, improving efficiency and reducing downtime on production lines. It’s also employed for producing small – batch end – use parts and replacement components, offering a solution for supply chain resilience and on – demand manufacturing.
Market Segmentation and Regional Analysis
Market Segmentation
The SLS market can be segmented by material (plastics, metals – though plastics are currently more prevalent for SLS), component (hardware, software, services), and end – user industry. While metal 3D printing processes like DMLS and SLM are growing, polymer – based SLS remains significant due to its affordability and suitability for prototyping and low – volume production.
Regional Analysis
- North America: Currently holds the largest market share for SLS 3D printing. This is attributed to strong industrial adoption, significant government R&D investments, and a strong presence of key industry players and end – user industries like aerospace and healthcare.
- Asia – Pacific: Projected to be the fastest – growing market. Rapid industrialization, increasing adoption of advanced manufacturing technologies, and a growing emphasis on domestic manufacturing capabilities in countries like China, Japan, and South Korea are driving this growth.
- Europe: Also represents a significant market, with strong adoption in its established automotive and aerospace sectors. The region’s focus on Industry 4.0 and sustainable manufacturing practices further supports the growth of SLS technology.
Overcoming Challenges: Paving the Way for Wider Adoption
Despite its numerous advantages and rapid growth, the SLS market faces certain challenges that need to be addressed for broader adoption.
High Initial Cost
The initial investment for SLS printers and materials can be substantial, potentially limiting adoption by small and medium – sized enterprises (SMEs). However, the emergence of more affordable benchtop and entry – level systems is gradually reducing this barrier.
Material Limitations
While the range of SLS materials is expanding, it is still narrower compared to some other 3D printing technologies. Continued research and development into new powder formulations are crucial.
Post – Processing
SLS parts typically require post – processing steps such as cleaning (depowdering), and sometimes surface finishing (e.g., media blasting or vapor smoothing) to achieve the desired surface quality. Automation in post – processing is an area of ongoing development to reduce manual labor and costs.
Skilled Workforce
Operating and maintaining SLS equipment, as well as designing for additive manufacturing, requires specialized knowledge and skills. Addressing the skills gap through training and education programs is important for wider adoption.
Sustainability Concerns
The energy consumption of SLS printers and the recyclability of unsintered powder are environmental considerations. Innovations in energy – efficient hardware and improved powder recycling methods are key to enhancing the sustainability of SLS.
The Future Outlook: Innovations on the Horizon
The future of SLS 3D printing appears very promising, with several exciting trends set to further revolutionize the manufacturing landscape.
Increased Automation and Integration (Industry 4.0)
We expect deeper integration of SLS systems into automated digital manufacturing workflows, in line with Industry 4.0 principles. This includes robotic material handling, automated post – processing, and seamless data exchange with other manufacturing systems.
Advancements in Multi – Material SLS
Although still in its early stages, the ability to print with multiple materials or create gradient materials within a single SLS build could open up a new world of functional parts with tailored properties.
AI – Driven Optimization and Smart Factories
AI will continue to play an even more important role, from generative design and process optimization to predictive quality control and intelligent factory management.
Democratization of SLS Technology
The availability of more affordable and user – friendly SLS printers will continue to expand access to this powerful technology for smaller businesses, research institutions, and even individual innovators.
Focus on Sustainability
The drive for greener manufacturing will prompt further innovation in sustainable SLS materials, energy – efficient printer designs, and more effective powder recycling strategies.
Expansion into New Application Frontiers
We anticipate SLS making inroads into even more diverse applications, including areas like advanced electronics (with conductive materials), personalized medicine beyond implants (such as tailored pharmaceuticals), and highly customized consumer experiences. The development of smart materials that can change properties in response to environmental stimuli also holds great promise.
Strategic Imperatives for Staying Ahead
To succeed in the rapidly evolving SLS 3D printing market, businesses and professionals must take a forward – looking approach:
- Embrace Continuous Learning: Keep up with the latest technological advancements, material developments, and emerging applications.
- Invest in R&D and Innovation: For technology developers and material suppliers, continuous investment in research and development is crucial for maintaining a competitive edge.
- Foster Collaboration: Partnerships between hardware manufacturers, material scientists, software developers, and end – users can speed up innovation and the development of customized solutions.
- Focus on Application – Specific Solutions: Understand the unique needs of different industries and develop targeted SLS solutions to drive market penetration.
- Address Sustainability: Proactively adopt and promote sustainable practices in SLS printing, which will be increasingly important for market acceptance and regulatory compliance.
In conclusion, the Selective Laser Sintering 3D printing market is on a remarkable growth path, characterized by rapid innovation and expanding applications. Although challenges remain, the ongoing advancements in hardware, software, and materials, along with the increasing adoption across key industries, point to a future where SLS plays an even more central role in shaping the next generation of manufacturing. By understanding these trends and proactively adapting to the changing landscape, we can jointly unlock the full potential of this transformative technology.