Understanding SLS Technology and Its Speed Advantages
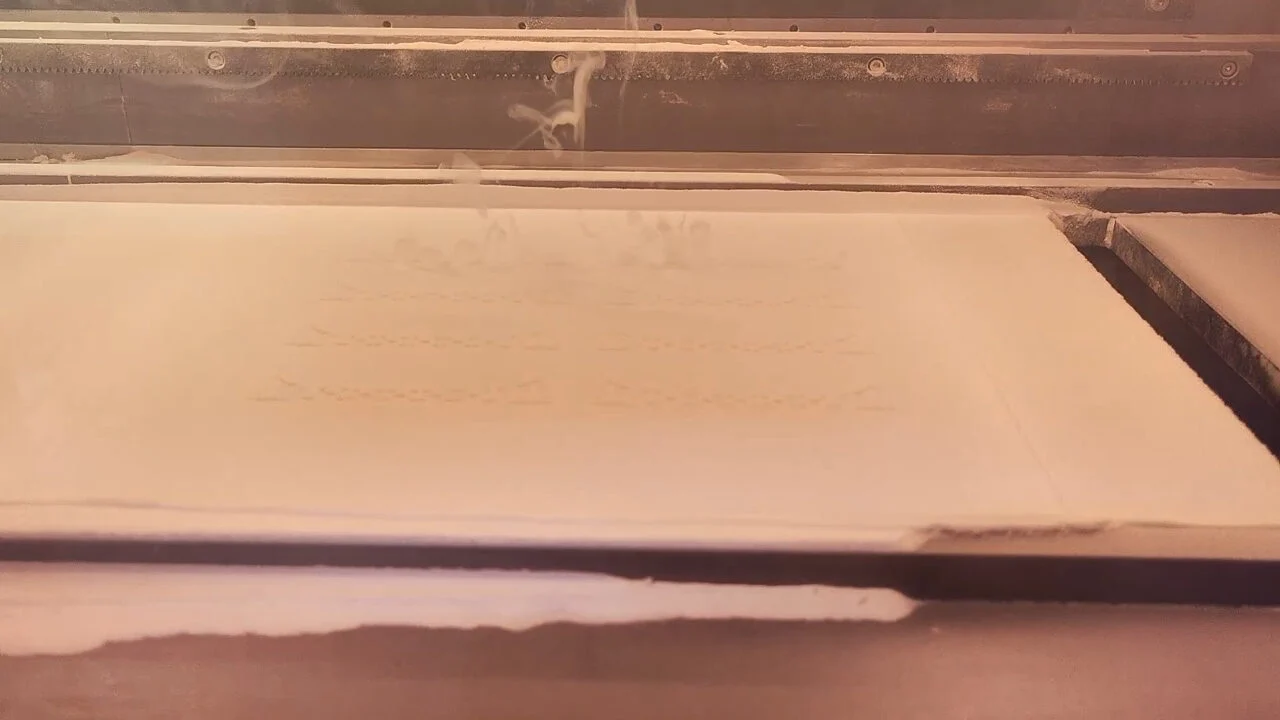
Selective Laser Sintering (SLS) is a leading additive manufacturing method known for its ability to rapidly produce complex parts with minimal setup requirements. Unlike traditional manufacturing or other 3D printing techniques, SLS uses a high-powered laser to fuse powdered materials layer by layer, eliminating the need for support structures and reducing post-processing time. This efficiency makes it particularly suitable for rapid prototyping and small-batch production where speed, design complexity, and material durability are critical.
How SLS Works
The SLS process follows a consistent sequence:
- Powder Preparation: A thin, even layer of powder is spread across the build platform.
- Laser Sintering: The laser selectively sinters the powder according to the digital model.
- Layer Lowering: The build platform lowers by one layer thickness (typically 50–150 microns).
- Powder Recoating: A new layer of powder is applied, repeating steps until completion.
- Cooling & Post-Processing: The part cools gradually before excess powder removal and finishing.
This automated workflow enables multiple parts to be built simultaneously within the same powder bed, enhancing throughput while maintaining precision.
Material Compatibility in SLS
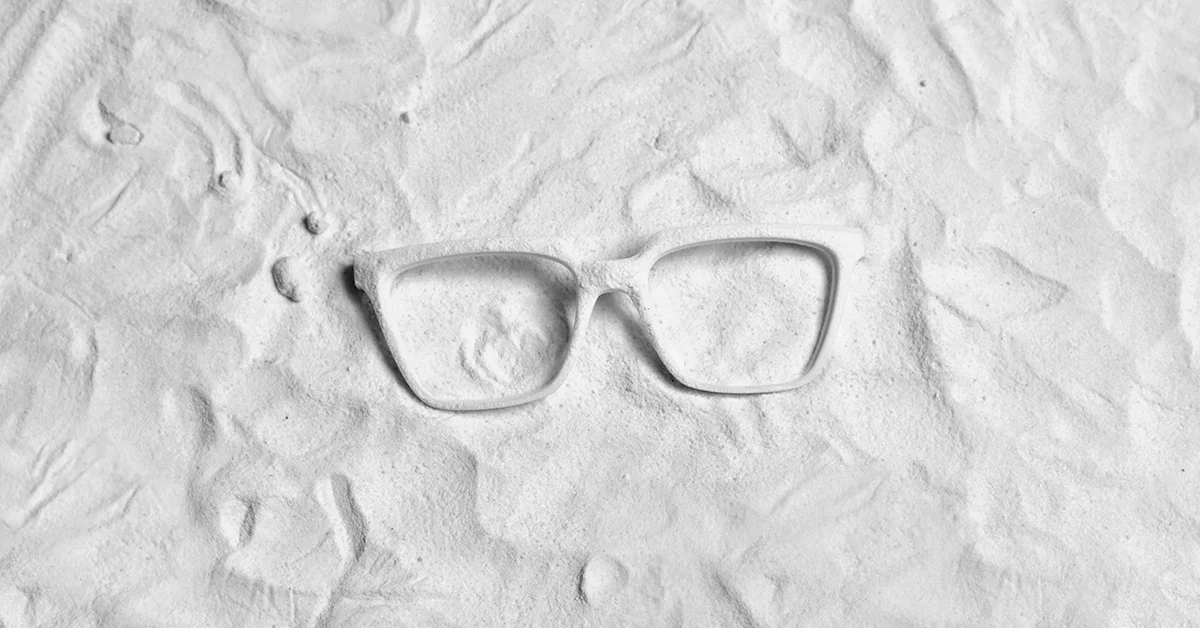
SLS supports a diverse range of thermoplastic powders, including:
- Nylon (Polyamide): Offers excellent mechanical properties, flexibility, and durability.
- Glass-Filled Nylon: Enhances stiffness and heat resistance for engineering applications.
- Aluminum-Filled Nylon: Improves thermal conductivity and surface finish.
- TPU (Thermoplastic Polyurethane): Provides elasticity for flexible, rubber-like components.
- Polycarbonate & Specialty Polymers: Emerging options for high-performance use cases.
These materials combine fast sintering speeds with functional performance, enabling ready-to-use parts without extensive secondary processing.
Key Factors Driving Faster Production with SLS
Layer-by-Layer Sintering: Precision and Efficiency
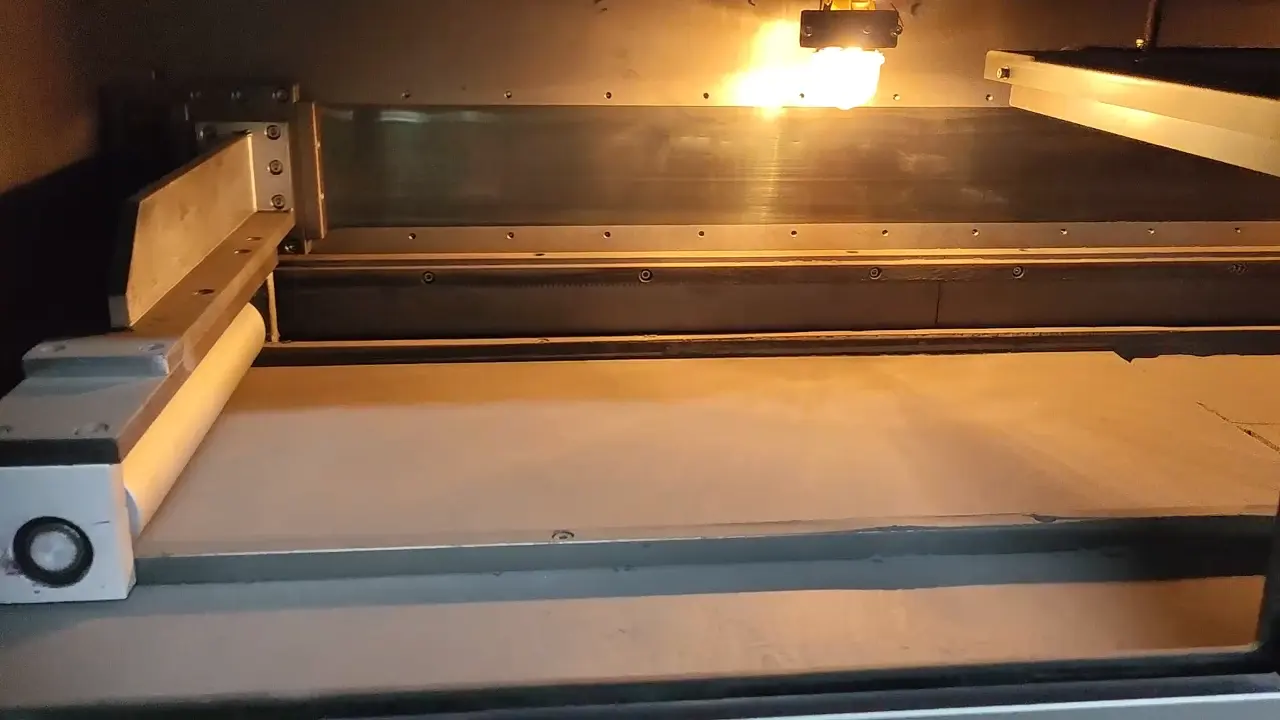
SLS builds parts additively, fusing only the required areas per layer. This eliminates tooling delays and allows for consistent print speeds regardless of geometric complexity. Additionally, precise laser targeting ensures energy efficiency and minimal waste.
Elimination of Support Structures
A major advantage of SLS is that unfused powder acts as a natural support structure during printing. This removes the need for additional scaffolding, streamlining both preparation and post-processing stages.
Process Stage | Impact Without Supports | Impact With Supports |
---|---|---|
Print Preparation | Faster setup | Requires support generation |
Printing Time | Streamlined | Extended due to supports |
Post-Processing | Simple powder removal | Extensive support removal |
Total Time Saved | Significant reduction | Increased production cycle |
Batch Production Capabilities
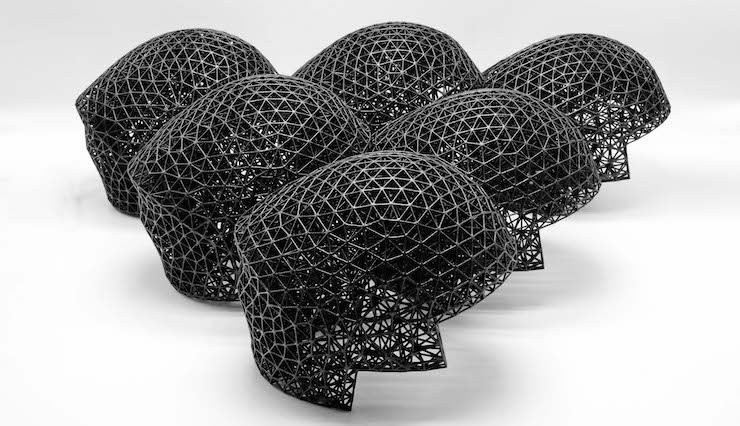
SLS printers utilize a powder bed that accommodates multiple parts in a single build. This capability allows for efficient nesting and full utilization of build volume, increasing throughput and reducing idle machine time between jobs.
Powder Reusability and Workflow Continuity
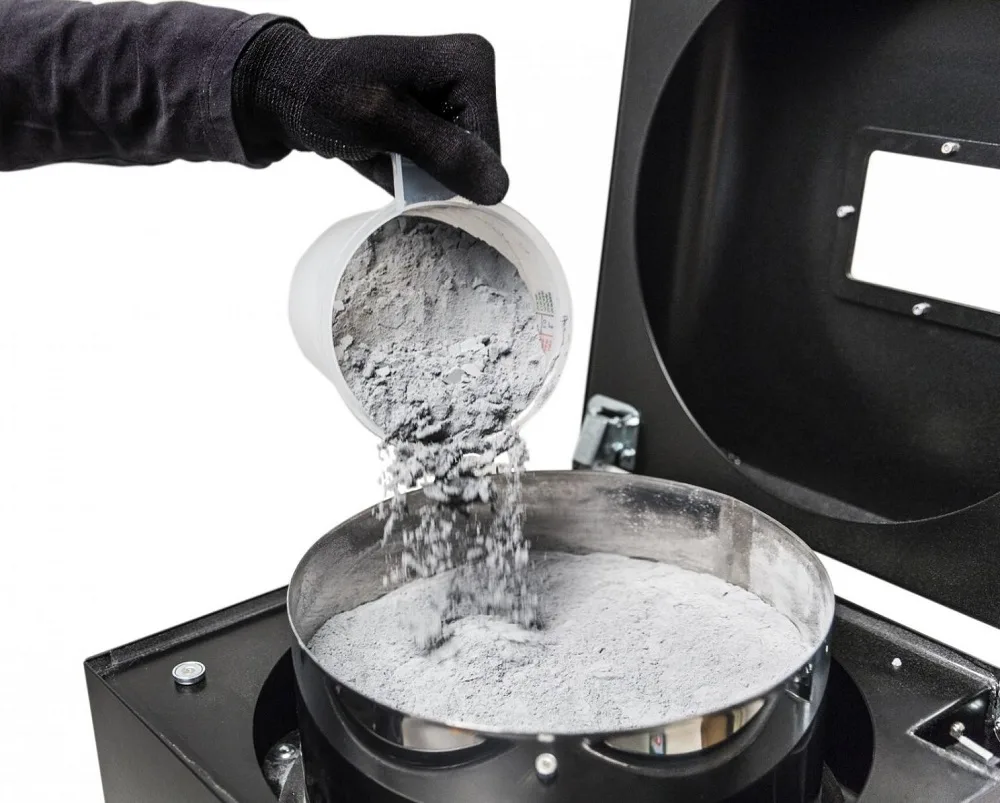
Unused powder remains viable for subsequent builds after sieving. This minimizes material waste and reduces preparation downtime, supporting continuous production cycles.
Automation Integration
Modern SLS systems increasingly incorporate automation at various stages:
- Powder Handling: Automated loading, distribution, and recycling reduce manual labor.
- Build Job Scheduling: Software optimizes layout and sequencing to maximize printer uptime.
- Part Removal & Cleaning: Depowdering stations and robotic post-processing accelerate finishing.
These integrations significantly reduce human intervention, improving overall workflow efficiency.
Comparative Analysis: SLS vs. Other 3D Printing Technologies
Technology | Common Materials | Layer Thickness | Speed Characteristics |
---|---|---|---|
SLS | Nylon, TPU, Glass-Filled | 50–150 µm | Fast for complex, batch parts; no supports |
FDM | PLA, ABS, PETG | 100–300 µm | Slower for complex parts; requires supports |
SLA | Photopolymer Resins | 25–100 µm | High resolution but slower build times |
MJF | Nylon Powders | 50–100 µm | Comparable or faster than SLS; limited materials |
SLS vs. FDM
FDM extrudes thermoplastic filament layer by layer, requiring physical nozzle movement and cooling intervals. While cost-effective for simple prototypes, FDM becomes inefficient for complex geometries and batch production. In contrast, SLS prints multiple parts simultaneously without support structures, offering superior throughput for functional components.
SLS vs. SLA
SLA provides exceptional surface detail using UV-cured resin. However, resin handling, washing, and curing extend lead times. SLS bypasses these steps, making it more suitable for functional testing and end-use parts.
SLS vs. MJF
Both SLS and Multi Jet Fusion (MJF) operate on powder bed principles. MJF applies fusing agents before heating, often achieving slightly faster print speeds and finer resolution. However, SLS offers broader material compatibility and greater flexibility in engineering-grade applications.
Real-World Applications Benefiting from SLS’s Speed
Rapid Prototyping and Design Iteration
SLS enables engineers to produce functional prototypes with mechanical properties close to final products. This accelerates design validation and reduces reliance on expensive molds.
Small to Medium Batch Manufacturing
For short-run production, SLS eliminates tooling costs and lead times. It supports customization and variant production without retooling, making it ideal for industries such as automotive, consumer goods, and electronics.
Complex Geometries and Assembly Reduction
SLS facilitates the integration of multiple components into a single printed part, reducing assembly complexity and logistics overhead. Internal channels, lattice structures, and embedded features can be manufactured directly without secondary operations.
Medical Devices and Customization
Hospitals and medical device manufacturers leverage SLS for patient-specific implants, prosthetics, and surgical guides. Biocompatible materials and rapid turnaround improve treatment timelines and operational efficiency.
Aerospace and Automotive Components
Both sectors demand lightweight yet durable parts with tight deadlines. SLS delivers on-demand spare parts, reduces inventory costs, and supports lean manufacturing strategies through rapid prototyping and validation.
Limitations and Operational Challenges
Despite its speed advantages, SLS has constraints that affect production timelines:
- Size Constraints: Build volume limits large-scale production, requiring dedicated print jobs for oversized parts.
- Machine Maintenance: Regular calibration and cleaning introduce potential downtime.
- Material-Specific Variables: Some powders require slower parameters for optimal results.
- Post-Processing Requirements: Although simplified compared to other methods, depowdering and optional finishing steps still impact total lead time.
Optimization Strategies for Maximum Time Efficiency
Part Orientation and Packing Density
Maximizing build chamber usage involves strategic part arrangement and orientation. Nesting software automates this process, ensuring optimal space utilization and minimizing empty powder regions.
Material Selection for Faster Sintering
Standard nylon powders generally offer the fastest sintering rates. Avoid overfilled variants unless specific mechanical properties justify the trade-off in speed.
Software-Driven Workflow Optimization
Advanced software tools enhance laser path efficiency, simulate thermal effects, and automate job scheduling to reduce idle time and increase throughput.
Preventative Maintenance Routines
Scheduled calibration, recoater blade cleaning, and powder quality checks ensure consistent performance and minimize unplanned interruptions.
Integration into Lean Manufacturing
Aligning SLS with lean workflows includes design-for-manufacturability principles, streamlined post-processing, and real-time tracking to optimize scheduling and resource allocation.
Economic Impact of Faster SLS Production
Cost Implications
Faster production translates to reduced labor, lower inventory carrying costs, and minimized tooling expenses. Energy-efficient operation further decreases utility bills.
Cost Factor | Traditional Manufacturing | SLS 3D Printing | Economic Effect |
---|---|---|---|
Tooling | High upfront cost | None | Significant capital savings |
Labor | High | Low | Reduced operational expenses |
Inventory | Large stockpiles required | On-demand | Reduced storage and waste |
Energy | Variable | Efficient | Lower utility consumption |
Market Agility and Competitive Advantage
Accelerated product development cycles allow companies to respond quickly to market feedback, launch products faster, and maintain innovation leadership.
Return on Investment (ROI) Considerations
Higher throughput, reduced labor costs, and increased customization opportunities contribute to improved profit margins and asset return.
Future Trends in SLS Speed Enhancement
Advances in Laser Technology
Multiple laser arrays, higher wattage lasers, and improved scanning optics will further reduce sintering times while maintaining resolution.
Innovations in Powder Materials
Finer, uniform powders and hybrid sintering techniques—such as infrared preheating—are being developed to improve fusion efficiency and part quality.
AI-Driven Automation
Artificial intelligence will optimize print scheduling, dynamically adjust laser parameters, and predict maintenance needs to minimize downtime and maximize productivity.
Industry Adoption and Scalability
Larger format machines, integration with hybrid manufacturing workflows, and sustainability-focused advancements will expand SLS adoption in mass production environments.