In the dynamic realm of manufacturing, 3D printing has emerged as a transformative force, revolutionizing product design and production. Among various 3D printing technologies, Selective Laser Sintering (SLS) stands out for its ability to craft complex geometries with remarkable strength and precision. However, the costs associated with this innovative technology often puzzle businesses and individuals.
Grasping the expenses related to SLS 3D printing is crucial for those considering it for prototyping, small – scale production, or mass manufacturing. Multiple factors, from material selection and machine investment to labor costs and post – processing, influence the overall cost of SLS printing. This article conducts an in – depth cost analysis of SLS 3D printing, dissecting the components that affect pricing. It explores the differences between SLS and other printing methods, presents cost – optimization strategies, and examines real – world case studies. By the end, readers will comprehensively understand the financial implications of SLS 3D printing, enabling informed decision – making for their projects.
What is SLS 3D Printing?
Selective Laser Sintering (SLS) is a revolutionary additive manufacturing technology that has transformed design and production approaches. Unlike traditional manufacturing methods, SLS uses a laser to fuse powdered materials layer by layer, creating intricate and durable parts. Let’s explore the fundamentals, advantages, and applications of SLS technology.
How SLS Works
At its core, SLS operates on a straightforward principle:
- Material Preparation: The process starts with a bed of finely powdered material. Nylon is commonly used, but metals and ceramics can also be employed.
- Laser Sintering: A high – powered laser scans across the powder bed. Based on 3D model data, it selectively melts and fuses the particles together.
- Layering: After the laser completes one layer, the powder bed is lowered, and a new layer of powder is applied. This process continues until the part is fully formed.
- Cooling and Removal: Once printing is finished, the part is allowed to cool in the powder bed. Then, it is carefully removed and cleaned.
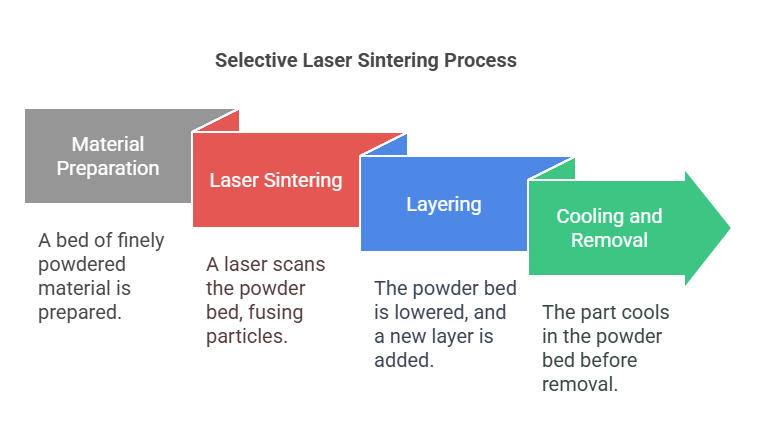
The following diagram illustrates the SLS process:
Powder Bed |
[Laser] |
——————- |
Layer 1 |
——————- |
Layer 2 |
——————- |
Layer 3 |
——————- |
Part |
+——————-+ |
Advantages of SLS Printing
SLS offers numerous benefits that make it a preferred choice for many applications:
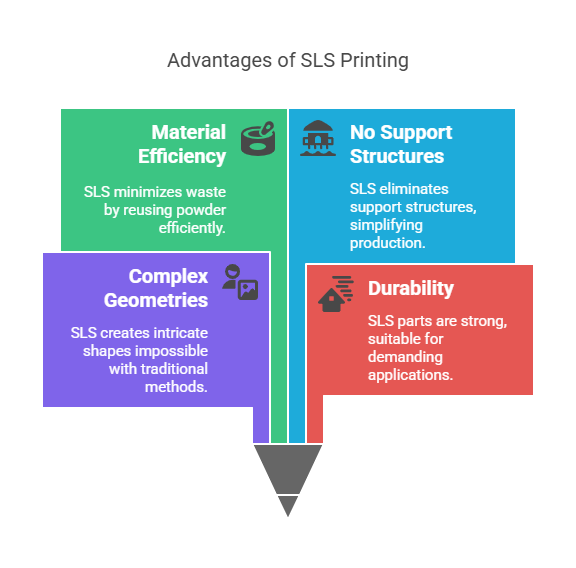
- Complex Geometries: SLS can produce complex shapes that are often unachievable with traditional manufacturing methods. This includes intricate internal structures and support features. For example, in aerospace component design, SLS can create lightweight parts with complex internal lattice structures for enhanced strength – to – weight ratios.
- Durability: Parts produced via SLS are typically strong and functional, making them suitable for end – use applications. In the automotive industry, SLS – printed parts can withstand the rigors of engine testing and actual vehicle use.
- Material Efficiency: SLS uses a powder bed that can be reused for subsequent prints. This minimizes waste and reduces costs. For instance, in a small – scale manufacturing facility, reusing powder can lead to significant savings over time.
- No Support Structures: Unlike other 3D printing technologies like Fused Deposition Modeling (FDM), SLS does not require additional support structures. The surrounding powder supports the part during the printing process, simplifying the production process.
Common Applications of SLS 3D Printing
SLS technology is widely used across various industries due to its versatility and efficiency. Here are some common applications:
Industry | Application |
Aerospace | Lightweight components and prototypes |
Automotive | Functional prototypes and tooling |
Medical | Custom implants and surgical guides |
Consumer Products | Customized and complex designs |
Industrial | Manufacturing aids and jigs |
In summary, SLS 3D printing is a powerful and versatile manufacturing solution. Understanding its mechanisms, advantages, and applications is essential for grasping the factors that influence SLS printing costs.
Factors Influencing SLS 3D Printing Costs
Understanding the costs associated with Selective Laser Sintering (SLS) 3D printing is vital for those considering this technology for their projects. Multiple factors contribute to the overall expense, and being aware of these can help in making informed decisions. Let’s explore the primary elements affecting SLS printing costs in detail.
1. Material Costs
Material selection significantly influences the cost of SLS printing. Thermoplastic powders are commonly used, with Nylon (PA 12 and PA 11) being prevalent due to their excellent mechanical properties. However, costs vary based on material quality, properties, and sourcing.
Material | Typical Cost per kg | Properties | Common Uses |
Nylon PA 12 | $$50 -$$70 | Strong, flexible, good chemical resistance | Prototyping, functional parts |
Nylon PA 11 | $$60 -$$80 | More eco – friendly, tougher than PA 12 | Automotive parts, consumer products |
TPU | $$80 -$$120 | Flexible, rubber – like characteristics | Gaskets, seals, soft – touch products |
Metal Powders | $$100 -$$300+ | High strength, conductive | Aerospace, automotive components |
- Bulk Buying: Purchasing materials in larger quantities can lead to significant cost reductions. For example, a manufacturing company that regularly uses SLS printing can save money by buying nylon powder in bulk.
- Quality Variations: Higher – quality materials may offer better performance but come at a premium price. A medical device manufacturer might choose a high – quality biocompatible powder for custom implants, despite its higher cost.
2. Machine Costs
Investment in SLS machinery greatly impacts overall costs. Consider the following aspects:
- Initial Investment: SLS printers range from tens of thousands to millions of dollars, depending on their capabilities and intended use. Entry – level SLS systems may start around $50,000, while industrial – grade systems can exceed $500,000. A startup focused on small – scale prototyping might opt for an entry – level printer to keep costs down.
- Maintenance and Upkeep: Regular maintenance is crucial to keep SLS printers in optimal condition. This includes routine cleaning of laser optics, calibration and alignment, and replacement of parts as needed. For instance, a well – maintained printer will have fewer breakdowns, reducing production downtime.
- Depreciation: Factor in the depreciation of equipment over time in cost calculations. As technology advances, the value of SLS printers may decrease, affecting the overall cost – effectiveness.
3. Labor Costs
Labor plays a critical role in the SLS printing process, especially in production facilities. Consider these labor cost aspects:
- Skilled Operators: Operating an SLS printer requires skilled personnel who can handle the machine, troubleshoot issues, and ensure quality control. Labor costs vary based on location and expertise, typically ranging from $20 to $50 per hour. In a high – cost – of – living area, the labor cost for an experienced operator may be on the higher end of this range.
- Post – Processing: After printing, parts often need cleaning and finishing. This involves removing excess powder, surface finishing (such as sanding and painting), and quality inspections. These steps can add significant labor costs, particularly in high – volume production. For example, in a consumer product manufacturing facility, post – processing a large number of SLS – printed parts can be time – consuming and expensive.
4. Energy Consumption
Energy costs, though often overlooked, can significantly impact the overall cost of SLS printing. Consider these key points:
- Electricity Usage: SLS printers consume substantial power during operation, mainly due to heating elements that maintain the powder bed temperature. A large – scale SLS printer may use a significant amount of electricity during a long print job.
- Cost Calculation: An average SLS printer might consume 5 to 15 kWh during a typical print job. If electricity costs are around $0.12 per kWh, the energy cost for a single print could range from $0.60 to $1.80 or more. This cost can add up over multiple print jobs.
5. Software and Licensing
Software contributes to the overall costs associated with SLS printing. Here’s what to know:
- Design Software: CAD software is essential for creating 3D models, and its price varies significantly. Popular tools like SolidWorks cost $3,000 – $9,000 (depending on the version), and AutoCAD costs $1,700 – $4,200 annually. A design studio may choose AutoCAD for its versatility and relatively lower annual cost.
- Slicing Software: Slicing software is necessary to prepare models for printing. While some options are free, advanced software with additional features may have licensing fees ranging from $500 to $2,000. A professional 3D printing service might invest in advanced slicing software to improve print quality and efficiency.
In conclusion, material costs, machine costs, labor costs, energy consumption, and software and licensing fees all influence SLS 3D printing costs. Understanding and managing these factors can help optimize SLS printing expenses.
Breakdown of SLS Printing Costs
When considering SLS for 3D printing, understanding cost breakdown is essential for budgeting and financial planning. This section analyzes pre – production, production, and post – production expenses, providing a detailed view of the total financial commitment in SLS printing.
1. Pre – Production Costs
Pre – production costs cover all expenses before actual printing. These costs are crucial as they lay the foundation for a successful project.
- Design and Prototyping Costs: Creating a 3D model is often the first step. Depending on complexity, CAD modeling costs can vary:
- In – house Design: Free if done internally. A company with an in – house design team can save on this cost.
- Outsourcing to Designers: $50 – $150 per hour. A startup without an in – house design team may outsource design work, incurring this hourly cost.
- 3D Model Preparation: This includes slicing the model and optimizing it for printing. Costs involve software licenses and the time spent preparing the model, which can take several hours depending on complexity.
Pre – Production Expense | Estimated Cost |
In – house Design | $0 |
Outsourced Design (3 hours) | $$150 -$$450 |
Software License (annual) | $$500 -$$4,200 |
Total Pre – Production Cost | Varies significantly |
2. Production Costs
Production costs are the actual expenses during the SLS printing process. These are often the most substantial costs and include:
- Material Usage: The amount of material used is directly related to the size and complexity of the prints. On average, expect a material consumption cost of $50 – $100 per kg of powder used. For example, printing a large, complex part will require more powder and thus cost more.
- Time Taken for Printing: The printing duration affects expenses, especially in terms of energy and labor. Print times can range from a few hours to several days based on part size. A large – scale industrial part may take days to print, increasing production costs.
- Electricity Costs: As mentioned earlier, a printer’s energy consumption during production adds to costs. For example, the energy cost for a typical print is $0.60 – $1.80 per job.
Production Expense | Estimated Cost |
Material (1 kg) | $$50 -$$100 |
Printing Time (8 hours) | $$1.60 -$$14.40 (energy) |
Total Production Cost (1 kg) | $$51.60 -$$114.40 |
3. Post – Production Costs
Post – production costs cover all expenses after printing. Proper finishing is crucial for achieving desired quality, especially in functional parts.
- Cleaning and Finishing: Removing excess powder and finishing parts requires significant labor. Cleaning labor costs $20 – $50 per hour, and typically 1 – 2 hours are needed per job. In a high – volume production scenario, this labor cost can be substantial.
- Quality Control: Ensuring parts meet specifications incurs costs. This includes inspection processes, testing for durability or precision, and possible part reworking. A medical device manufacturer will need to conduct strict quality control to ensure the safety and effectiveness of SLS – printed implants.
- Packaging and Shipping: If parts need to be delivered, consider packaging materials ($5 – $15 per part) and shipping costs, which vary based on destination and size. A company shipping SLS – printed parts internationally will face higher shipping costs.
Post – Production Expense | Estimated Cost |
Cleaning Labor (2 hours) | $$40 -$$100 |
Quality Control | $$50 -$$200 (depending on complexity) |
Packaging and Shipping | $$5 -$$30 |
Total Post – Production Cost | $$95 -$$330 |
Summary of Total Costs
Aggregating costs from all three stages gives a clear picture of the total financial commitment. Here’s a simplified summary of potential costs for a single print job:
Cost Component | Estimated Total Cost |
Total Pre – Production Cost | $$150 -$$450 |
Total Production Cost | $$51.60 -$$114.40 |
Total Post – Production Cost | $$95 -$$330 |
Total Estimated Cost | $$296.60 -$$894.40 |
These figures show that SLS printing costs vary significantly based on factors like design complexity, material choice, and finishing requirements. Understanding this breakdown helps identify areas for cost optimization.
Comparing SLS Printing Costs with Other 3D Printing Technologies
As the additive manufacturing landscape expands, various 3D printing technologies offer distinct advantages and cost structures. Understanding how SLS compares to other methods is crucial for making informed project decisions. This section compares SLS printing costs with those of Fused Deposition Modeling (FDM) and Stereolithography (SLA).
1. Overview of 3D Printing Technologies
Before comparing costs, briefly outline the three technologies:
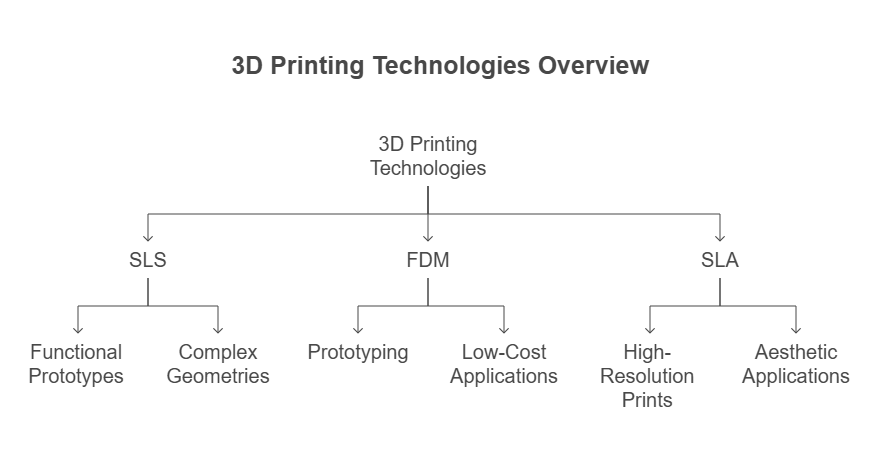
- Selective Laser Sintering (SLS): Uses a laser to fuse powdered materials layer by layer, suitable for functional prototypes and complex geometries. For example, it can create intricate parts for the aerospace industry.
- Fused Deposition Modeling (FDM): Melts and extrudes thermoplastic filament to build objects layer by layer. FDM is commonly used for prototyping and low – cost applications. A hobbyist might use an FDM printer to create simple models.
- Stereolithography (SLA): Employs a UV laser to cure liquid resin into solid parts, offering high – resolution prints but often at a higher material cost. SLA is ideal for applications where aesthetics are crucial, such as jewelry design.
2. Cost Comparison
A cost comparison between SLS, FDM, and SLA can be structured around material costs, machine costs, and operational costs.
Cost Factors | SLS | FDM | SLA |
Material Costs | $$50 -$$120 per kg | $$20 -$$50 per kg | $$100 -$$300 per liter |
Machine Costs | $$50,000 -$$500,000+ | $$200 -$$5,000 | $$3,000 -$$200,000 |
Print Time | Hours to days depending on size | Faster for small parts | Generally faster for small parts |
Energy Consumption | Moderate to high | Low to moderate | Moderate |
Labor Costs | $$20 -$$50 per hour | $$15 -$$30 per hour | $$20 -$$50 per hour |
3. Detailed Breakdown of Costs
Material Costs
- SLS: SLS material costs can be high due to specialized powders. However, these materials yield strong, functional parts, justifying the expense in many professional applications. The ability to reuse excess powder helps reduce material costs. For example, in automotive prototyping, SLS – printed parts need to be durable, so the higher material cost is acceptable.
- FDM: FDM materials, mainly thermoplastic filaments, are generally more affordable and widely available. This makes FDM an attractive option for hobbyists and small businesses seeking low – cost prototyping. A startup on a tight budget might choose FDM for quick and inexpensive prototypes.
- SLA: SLA materials, usually in liquid resin form, are often the most expensive per unit volume. However, SLA prints can achieve exceptional detail and smooth finishes, making them ideal for applications where aesthetics are important. A jewelry designer might use SLA to create intricate and beautiful pieces.
Machine Costs
- SLS Machines: Investing in SLS technology is substantial, with industrial systems often costing hundreds of thousands of dollars. This upfront cost can be a barrier for some users. However, in the long run, the potential for high – quality production can offset this. A large – scale manufacturing company may find the investment worthwhile for high – volume, high – quality production.
- FDM Printers: FDM printers are available at various price points, making them the most accessible option for beginners and small businesses. Entry – level machines can cost as little as $200, while professional – grade machines may reach up to $5,000. A hobbyist can start with an inexpensive entry – level FDM printer.
- SLA Printers: SLA machines vary widely in price. While entry – level models are affordable, professional SLA printers can be very costly due to advanced technology and capabilities. A dental laboratory might invest in a high – end SLA printer for accurate dental models.
Operational Costs
- SLS: SLS operating costs can be higher due to energy consumption and the need for skilled labor for setup and post – processing. The complexity of SLS requires experienced operators to ensure quality and efficiency. For example, in a precision – parts manufacturing facility, the operator needs to carefully calibrate the laser settings for each job, which takes time and expertise. This, combined with the significant energy usage during the printing process, contributes to the relatively high operational costs.
- FDM: FDM typically has lower operational costs. The printing process is relatively straightforward, and it requires less post – processing. For instance, a small – scale 3D printing service that mainly caters to hobbyists can quickly produce FDM – printed parts with minimal additional processing. However, the quality of FDM parts may not match that of SLS or SLA for certain applications, such as those requiring high – strength or smooth – surface finishes.
- SLA: SLA operations also demand higher labor costs because of the extensive post – processing and finishing work involved. Cleaning parts and curing them can add to labor time and associated costs. In a jewelry production studio using SLA, workers need to spend a significant amount of time carefully removing support structures and polishing the printed pieces to achieve the desired aesthetic quality.
4. When to Choose SLS Over Other Technologies
Choosing SLS over FDM or SLA depends on specific project requirements:
- Choose SLS if:
- You need strong, durable parts suitable for functional testing or end – use applications. For example, in the aerospace industry, SLS – printed components can withstand the extreme conditions of flight, making them ideal for use in aircraft.
- You require complex geometries or intricate designs that traditional methods can’t achieve. SLS can create parts with internal lattice structures or complex organic shapes that are difficult to produce through other means.
- You have a higher budget and are focused on quality over cost. A medical device company developing a custom – made implant may opt for SLS to ensure the highest quality and performance.
- Choose FDM if:
- You are working on a tight budget and need a cost – effective solution for prototyping. A startup in the consumer product industry may use FDM to quickly test design concepts without breaking the bank.
- Your parts do not require the high strength or detail that SLS provides. Simple prototypes or parts for non – critical applications can be effectively produced using FDM.
- You need quick iterations or lower volume production. FDM’s relatively fast printing speed for small parts and lower setup costs make it suitable for rapid prototyping.
- Choose SLA if:
- Fine detail and surface finish are critical for your application, such as in jewelry design, dental models, or high – end consumer product prototypes. SLA can achieve smooth, high – resolution surfaces with intricate details.
- You are creating small parts where time – to – print is a significant factor. SLA’s fast curing process can quickly produce small, detailed parts.
- You can afford the higher material costs for the benefits of high – resolution prints. A luxury goods manufacturer may be willing to pay more for SLA materials to create high – quality prototypes.
In summary, each 3D printing technology has its own set of advantages and cost – related considerations. SLS is often the top choice for producing strong, complex parts, while FDM and SLA serve different market niches. Understanding these cost components is essential for choosing the right technology for specific projects.
Strategies for Optimizing SLS Printing Costs
Selective Laser Sintering (SLS) offers remarkable advantages in additive manufacturing, but its costs can accumulate rapidly. To maximize investment returns and ensure the best outcomes, it’s crucial to implement strategies that optimize SLS printing costs. This section explores various methods to reduce expenses while maintaining quality and efficiency.
1. Material Efficiency
Maximizing material use is an effective way to cut costs. Consider the following strategies:
- Design for SLS:
- Create designs that minimize material usage. For example, use hollow structures, lattice designs, or less dense infill patterns. A lightweight bicycle frame prototype can be designed with a lattice structure using SLS, reducing the amount of powder needed without sacrificing strength.
- Avoid over – engineering. Only include necessary features to save on material costs. When designing a simple consumer product part, eliminate any non – essential elements that would increase material consumption.
- Reuse Excess Powder: SLS technology allows for the reusability of unused powder from previous prints. Establish a system to collect, sift, and reuse this powder effectively. In a medium – sized 3D printing service, reusing powder can lead to cost savings of up to 50%.
- Bulk Purchasing: Buying materials in larger quantities can result in bulk discounts. However, ensure you have proper storage and inventory management strategies in place. A large – scale manufacturing company that regularly uses SLS can save 10 – 15% on material costs by purchasing powder in bulk.
Material Efficiency Strategy | Impact on Costs |
Design for SLS | Reduce material usage by 20 – 30% |
Reuse excess powder | Lower costs by up to 50% |
Bulk purchasing | Average savings of 10 – 15% |
2. Process Optimization
Streamlining the printing process can lead to significant cost savings. Here are some tips:
- Optimizing Print Settings: Fine – tune laser settings, layer thickness, and print speed according to the part geometry. Adjusting these parameters can boost production speed while maintaining quality, thereby reducing operational costs. For a particular automotive part, adjusting the laser power and layer thickness can cut the print time by 20% without affecting the part’s integrity.
- Batch Printing: Whenever possible, batch similar parts in one print job. This minimizes the setup time and energy consumption per part. A 3D printing service can save costs by printing multiple small parts of the same type in a single batch.
- Utilizing Simulation Software: Use software to simulate the build process before actual printing. This helps identify potential issues and optimize the layout of parts in the build chamber. For example, simulation software can predict where parts might experience warping during printing, allowing users to adjust the design or print settings accordingly.
3. Labor Cost Management
Labor expenses can have a major impact on overall costs, so managing them is essential. Here’s how:
- Investing in Training: Provide training for staff to ensure they are proficient in operating SLS printers and conducting post – processing tasks efficiently. A well – trained operator can reduce printing errors by 30 – 50% and minimize downtime. In a manufacturing facility, investing in operator training can lead to significant savings in the long run.
- Streamlining Post – Processing: Develop a standardized process for cleaning and finishing parts. Consider investing in automated tools to speed up the post – processing phase. A company producing high – volume SLS – printed parts can decrease labor time by 20 – 40% by using automated powder – removal equipment.
Labor Cost Management Strategy | Impact on Costs |
Staff training | Reduce errors by 30 – 50% |
Streamlined post – processing | Decrease labor time by 20 – 40% |
4. Energy Efficiency
Since energy consumption contributes to overall costs, implementing energy – saving measures is beneficial. Consider the following strategies:
- Monitoring Energy Usage: Use energy monitoring systems to track usage throughout the printing process. Identify areas where energy consumption is higher than average and find ways to reduce it. For example, if a particular printer model consumes excessive energy during the pre – heating phase, explore ways to optimize this process.
- Scheduling Printing Wisely: Schedule printing jobs during off – peak electricity hours if your energy provider offers lower rates. A 3D printing business can save on energy costs by running print jobs overnight when electricity rates are lower.
5. Quality Control Measures
Investing in proper quality control can save costs in the long term by preventing expensive reprints and ensuring parts meet specifications. Here’s how to implement quality control effectively:
- Regular Inspections: Conduct periodic checks of both the printer and the materials used. Early detection and resolution of issues can prevent defects and costly reprints. In a medical device manufacturing facility, regular inspections of SLS printers and materials are crucial to ensure the safety and effectiveness of printed implants.
- Feedback Loop: Establish a feedback system between the design and production teams. Continuously improve part designs based on performance and issues encountered during production. For example, if a particular part design frequently leads to printing errors, the design team can make adjustments based on feedback from the production team.
Quality Control Strategy | Impact on Costs |
Regular inspections | Reduce reprint costs by 20 – 50% |
Feedback loop | Continuous improvement reduces errors over time |
Optimizing SLS printing costs requires a multi – faceted approach. By focusing on material efficiency, process optimization, labor cost management, energy efficiency, and quality control, businesses can reduce expenses and increase profitability while maintaining the high – quality standards of SLS technology.
Emerging Trends and Technologies in SLS Printing
As the additive manufacturing field continues to evolve, Selective Laser Sintering (SLS) remains at the forefront of innovation. New trends and technologies are emerging, enhancing SLS printing capabilities, reducing costs, and improving overall efficiency. This section explores significant trends and advancements in SLS technology and their potential impact on the future of SLS printing.
1. Advancements in Material Science
Material innovation is vital for the continued success and versatility of SLS. Consider these developments:
- New Powder Materials: Researchers are developing advanced polymers with improved mechanical properties, thermal resistance, and biocompatibility for medical applications. High – performance nylon blends and composite powders are becoming more popular. For example, carbon fiber – reinforced nylon powders combine the strength of carbon fibers with the versatility of nylon, creating lightweight and extremely durable parts. These materials are ideal for applications in the aerospace and automotive industries, where strength – to – weight ratios are crucial.
- Recyclable and Eco – Friendly Materials: There is a growing emphasis on sustainability in manufacturing. New biodegradable and recyclable powder materials are emerging, reducing the environmental impact of SLS printing. Bio – based polyamides made from renewable resources offer comparable mechanical properties to traditional materials while minimizing reliance on fossil fuels. A consumer product manufacturer might use these eco – friendly materials to meet sustainability goals without sacrificing product quality.
Material Science Advancement | Impact on SLS Printing |
New powder materials | Enhanced performance and capability |
Recyclable materials | Reduced environmental impact |
2. Automation and Industry 4.0 Integration
The integration of automation and Industry 4.0 principles is transforming SLS printing operations:
- Automated Workflow: Automation tools are being developed to handle repetitive tasks such as powder bed cleaning, part removal, and post – processing. This reduces labor costs and minimizes human error. In a large – scale 3D printing factory, automated powder – bed cleaning systems can work continuously, improving production efficiency and reducing the need for manual labor.
- Data – Driven Manufacturing: The use of IoT (Internet of Things) technologies enables real – time monitoring of printing processes. Sensors provide data on temperature, humidity, and machine performance, facilitating predictive maintenance and reducing downtime. For example, a company can remotely monitor printer parameters and adjust settings in real – time to optimize performance and quality. This ensures that the printer operates at its best, reducing the risk of breakdowns and costly repairs.
Automation Trend | Impact on SLS Printing |
Automated workflows | Increased efficiency and accuracy |
Data – driven manufacturing | Enhanced predictive maintenance |
3. Improved Software Solutions
Advancements in software technology are making SLS more accessible and efficient:
- Enhanced Design Software: The latest CAD software tools are incorporating features tailored for SLS printing. These include design optimization algorithms that suggest the best structures for strength while minimizing material use. A product designer can use this software to create innovative, lightweight designs that are both functional and cost – effective.
- Slicing Software Enhancements: Advanced slicing software now includes simulation capabilities. It can predict potential print failures, allowing users to adjust designs before printing. For instance, some software can evaluate the thermal behavior of parts to prevent warping or other issues during the printing process. This saves time and materials by avoiding costly reprints.
Software Advancement | Impact on SLS Printing |
Enhanced design software | Improved part optimization |
Advanced slicing capabilities | Reduced print failures |
4. Cost Reduction Efforts
As competition in the 3D printing market intensifies, companies are focusing on reducing SLS printing costs:
- Economies of Scale: Larger SLS printing facilities are emerging, capable of high – volume production runs. This allows companies to spread fixed costs over a larger number of parts, significantly reducing the per – unit cost. A large – scale contract manufacturing company can take advantage of economies of scale to offer more competitive pricing for SLS – printed parts.
- Hybrid Manufacturing: Combining SLS with other manufacturing processes, such as CNC machining, can optimize production efficiency. Using SLS for complex geometries and CNC for finishing can result in lower overall costs. For example, in the production of a high – precision mold, SLS can be used to create the intricate internal features, and CNC machining can be used to finish the surface to the required tolerance.
Cost Reduction Trend | Impact on SLS Printing |
Economies of scale | Lower per – unit costs |
Hybrid manufacturing | Enhanced efficiency |
5. Customization and On – Demand Production
The demand for customized products is driving changes in SLS technology:
- Personalization: SLS printing enables the creation of highly customized products tailored to individual needs. This trend is particularly prominent in industries like healthcare, where custom prosthetics and dental devices are becoming more common. A patient – specific dental implant can be designed and printed using SLS technology, providing a better fit and improved functionality.
- On – Demand Manufacturing: The ability to produce parts on – demand reduces inventory costs and waste. SLS is well – suited for this model, allowing companies to produce products only as needed and optimize their supply chain. A consumer electronics company can use SLS to produce replacement parts on – demand, eliminating the need for large inventory stockpiles.
Customization Trend | Impact on SLS Printing |
Increased personalization | Growth in niche markets |
On – demand manufacturing | Reduced waste and inventory costs |
The SLS printing landscape is constantly evolving, driven by advancements in materials, automation, software, cost – reduction strategies, and the demand for customization. Staying updated on these trends is essential for businesses looking to leverage SLS technology effectively. By adopting these innovations, companies can reduce costs, enhance the quality and functionality of their printed parts, and gain a competitive edge in the market.