Selective Laser Sintering (SLS) 3D printing has emerged as a transformative manufacturing technique, offering distinct advantages over conventional production methods. This paper provides a structured comparison between SLS 3D printing and traditional manufacturing, evaluating technical processes, design flexibility, cost structures, production scalability, environmental impact, and industry applications. By analyzing strengths and limitations within each domain, this study supports informed decision-making for manufacturers, engineers, and product developers seeking optimal production strategies.
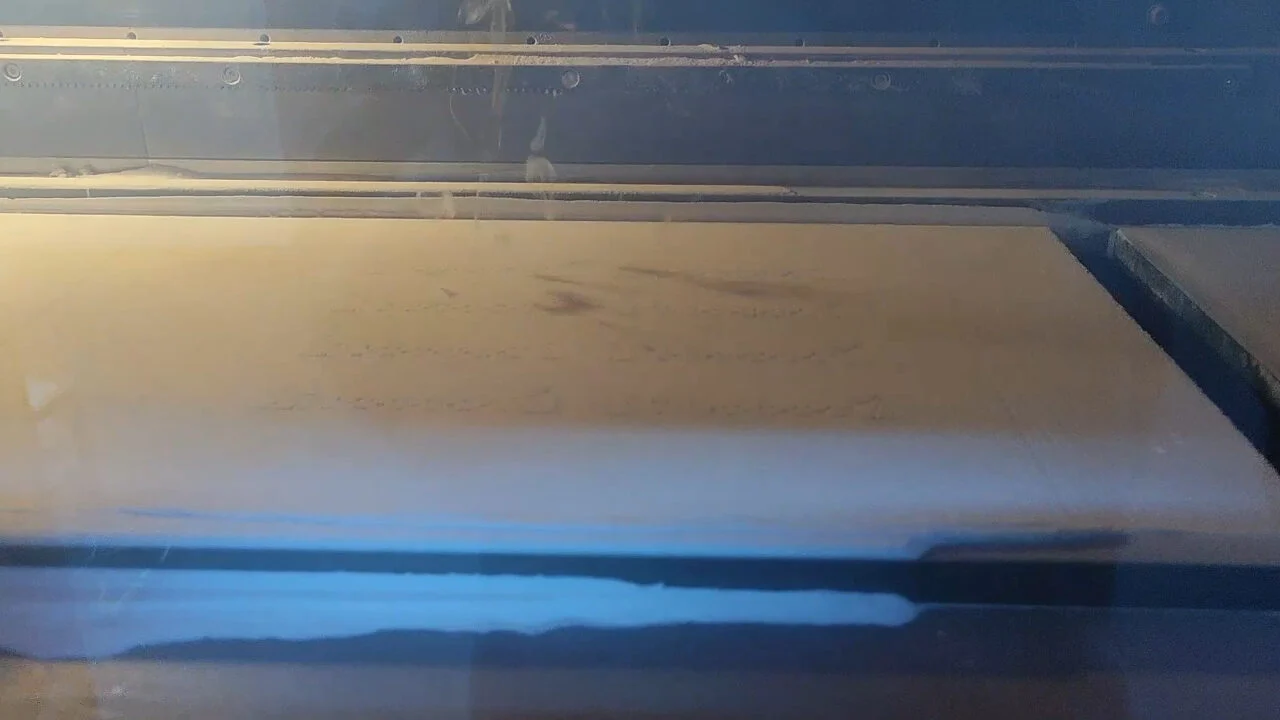
In the evolving landscape of industrial production, selecting the appropriate manufacturing method significantly influences product development success. As additive manufacturing technologies mature, SLS 3D printing challenges established methodologies such as CNC machining, injection molding, and casting. This paper examines core differences between SLS and traditional approaches, focusing on practical applicability across industries.
Technical Foundations
Selective Laser Sintering (SLS)
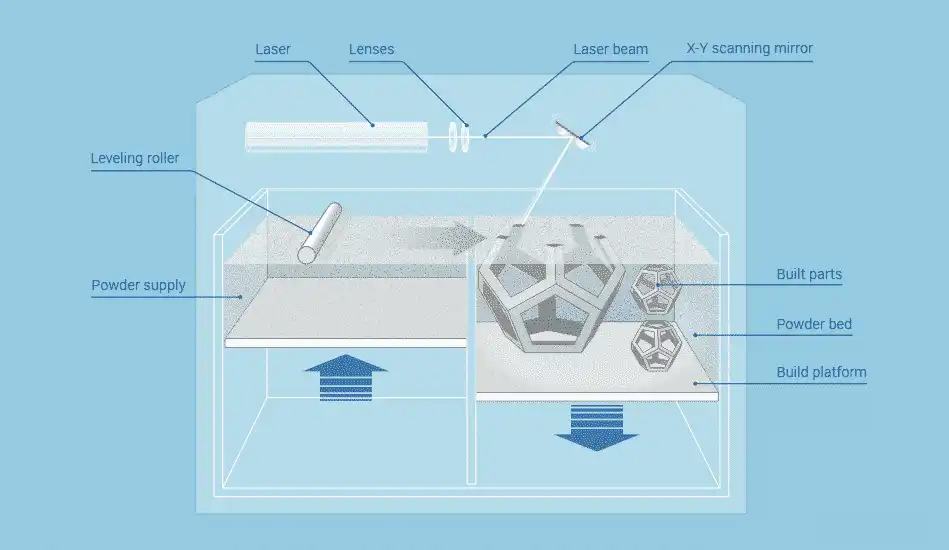
SLS is an additive manufacturing process that constructs three-dimensional components by selectively fusing polymer powder layers using a high-powered laser. The process involves four key stages:
- Powder Bed Preparation : A thin layer of thermoplastic powder is uniformly spread across the build platform.
- Laser Sintering : The laser scans cross-sectional data from a CAD model, sintering powder particles without full melting.
- Layer-by-Layer Construction : After each layer completes, the platform lowers, and a new powder layer is applied. This iterative process continues until the part forms.
- Cooling and Post-Processing : Once printing concludes, parts cool gradually to minimize deformation. Excess powder is removed, and optional finishing techniques enhance surface quality.
Common materials include nylon (PA12), TPU, and PEEK, offering mechanical strength, thermal resistance, and biocompatibility.
Traditional Manufacturing
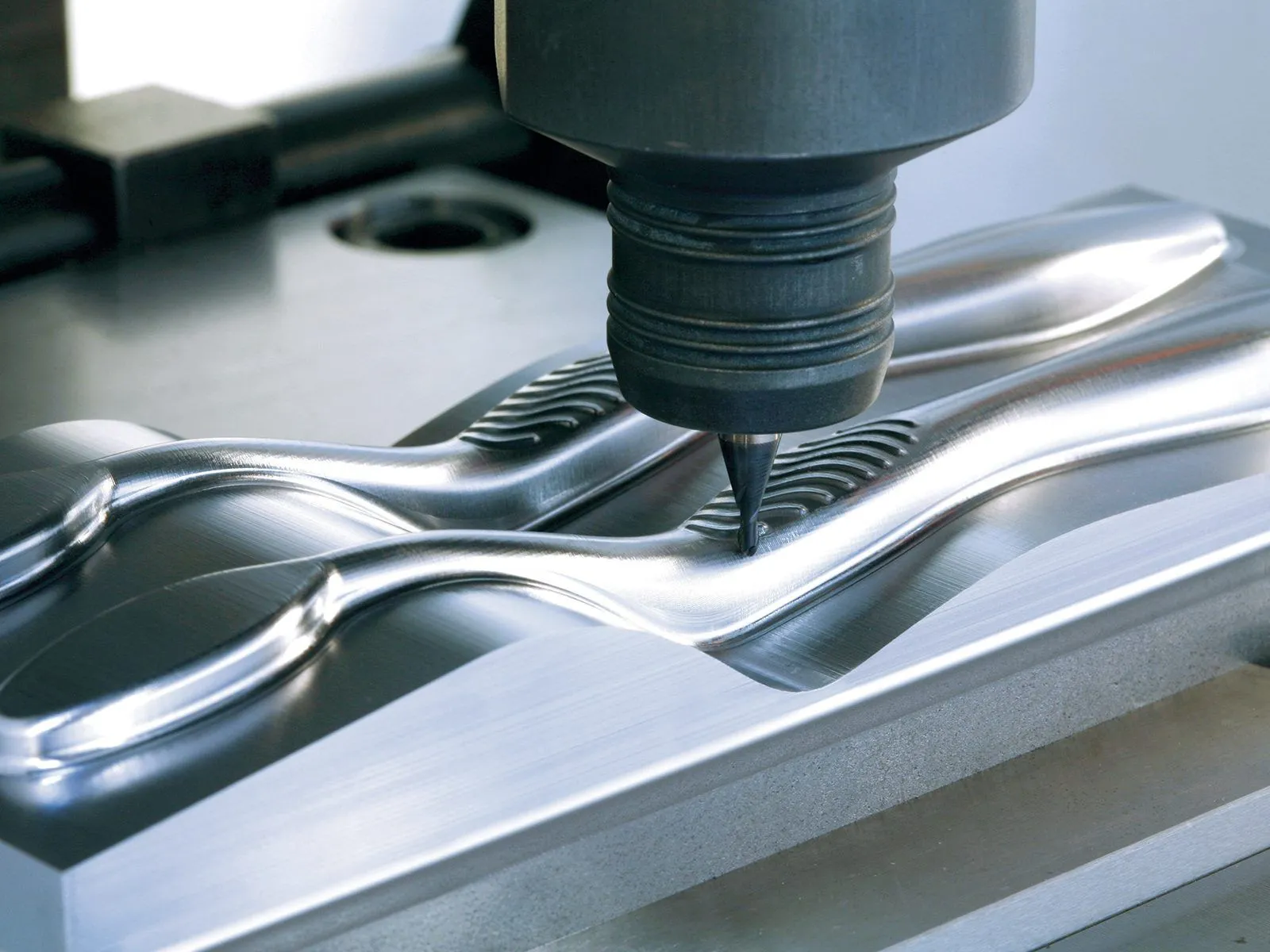
Conventional methods fall into two categories: subtractive and formative. Subtractive techniques, such as CNC machining, remove material from a solid block to create desired geometries. Formative processes like injection molding shape material through molds or pressure.
Each approach presents distinct tooling dependencies, production cycles, and geometric constraints. While these methods enable high-volume output with consistent quality, they often require significant upfront investment in molds or fixtures.
Design Flexibility and Complexity
Advantages of SLS
SLS excels in fabricating complex internal geometries and lattice structures unattainable via traditional means. Key benefits include:
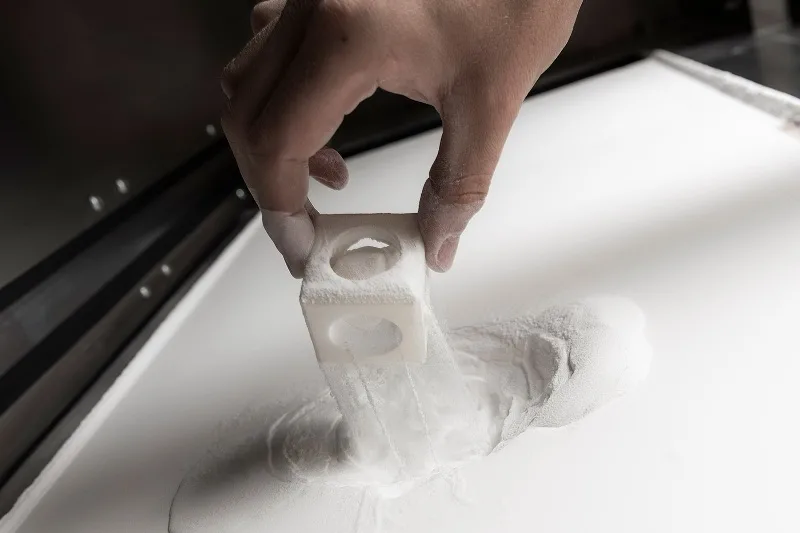
- Support-Free Printing : Unfused powder acts as a natural support structure, enabling overhangs and intricate cavities without additional scaffolding.
- Integrated Assembly : Multi-component assemblies can be printed as single units, reducing post-processing labor and assembly complexity.
- Rapid Iteration : Digital design modifications translate directly to physical prototypes, eliminating mold revisions and accelerating development cycles.
Limitations in Traditional Manufacturing
Conventional methods impose design restrictions due to tool access and mold requirements. For instance:
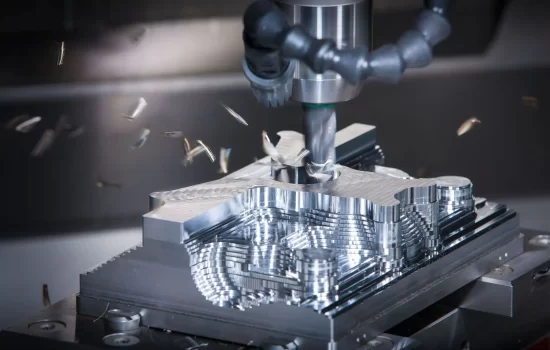
- Undercuts and Internal Channels : Often necessitate complex mold designs or secondary machining steps.
- Draft Angles : Injection-molded components require draft angles to facilitate part ejection, limiting certain shapes.
- Assembly Requirements : Complex parts typically require disassembly into multiple components before fabrication.
Production Speed and Scalability
SLS Performance Characteristics
SLS achieves rapid prototyping and small-batch production but faces throughput limitations at scale. Factors influencing speed include:
- Layer Thickness : Thinner layers improve detail resolution but increase print duration.
- Part Volume : Larger components demand more time due to increased scanning area and cooling needs.
- Batch Processing : Multiple parts fit within a single print bed, enhancing efficiency for low-volume runs.
Post-processing steps—such as powder removal, sanding, and sealing—affect total production time.
Traditional Manufacturing Efficiency
Established methods demonstrate superior scalability for mass production:
- Mold-Based Processes : Injection molding enables thousands of identical parts per hour once tooling is complete.
- CNC Machining : Offers precision and repeatability for mid-to-large batches when setup time amortizes across volume.
However, initial preparation delays and tooling costs render these options less viable for short-run or custom projects.
Cost Analysis
SLS Cost Drivers
Cost determinants include:
- Material Utilization : Unused powder can be recycled, minimizing waste.
- Design Complexity : Highly detailed parts may require extended post-processing.
- Production Volume : Economically advantageous for quantities below 1,000 units.
Traditional Manufacturing Economics
Key financial considerations:
- Upfront Investment : Mold creation incurs substantial costs, particularly for injection molding.
- Unit Cost Reduction : Economies of scale dramatically lower per-unit expenses beyond threshold volumes.
- Tool Maintenance : Ongoing wear and potential repairs affect long-term expenditure.
Quality and Precision
Surface Finish and Dimensional Accuracy
SLS-printed components exhibit inherent surface roughness (Ra: 6–12 µm), requiring polishing or infiltration for smooth finishes. Dimensional tolerances range from ±0.1 to ±0.3 mm, influenced by particle size, laser calibration, and thermal behavior.
Traditional methods deliver superior surface quality and tighter tolerances:
- CNC Machining : Achieves Ra values below 1.6 µm with tolerances ±0.005–±0.02 mm.
- Injection Molding : Surface finish Ra: 0.4–3.2 µm; dimensional accuracy ±0.05–±0.2 mm.
Mechanical Properties
SLS parts exhibit slight anisotropy due to layer bonding, while traditionally manufactured components maintain isotropic properties, ensuring uniform performance under stress.
Environmental Impact
SLS Sustainability Advantages
- Material Efficiency : High reuse rate of unsintered powder reduces waste.
- Lightweight Structures : Enables resource-efficient component designs.
- On-Demand Production : Minimizes overproduction and inventory surplus.
Challenges in Traditional Manufacturing
- High Material Waste : Subtractive processes generate significant scrap.
- Energy Consumption : Melting and forming operations are energy-intensive.
- Chemical Usage : Coolants and solvents pose environmental risks if improperly managed.
Industry Applications
SLS in Aerospace, Medical, and Automotive Sectors
- Aerospace : Lightweight brackets, ducts, and structural prototypes reduce aircraft weight and fuel consumption.
- Medical : Custom implants and surgical guides leverage biocompatible materials for patient-specific solutions.
- Automotive : Functional prototypes and aftermarket parts benefit from rapid iteration and minimal tooling.
Traditional Manufacturing Dominance
- Mass Production : Automotive body panels and engine components rely on mold-based efficiency.
- Electronics : Enclosures and connectors demand high precision and surface quality.
- Construction : Prefabricated metal components ensure durability and standardization.
Limitations and Future Trends
Current Constraints
- SLS : Limited material selection, slower large-part production, and higher equipment costs.
- Traditional Methods : High mold expenses, design inflexibility, and waste generation.
Emerging Innovations
- Hybrid Manufacturing : Combines additive and subtractive techniques for optimized performance.
- Smart Factory Integration : Leverages IoT and AI for real-time production optimization.
- Sustainable Practices : Focuses on energy efficiency, recyclability, and reduced emissions.
Conclusion
Both SLS 3D printing and traditional manufacturing offer distinct advantages contingent on application context. SLS excels in customization, complexity, and sustainability for low-volume production, whereas traditional methods remain superior for high-volume, standardized outputs. Strategic adoption of hybrid models enhances flexibility, combining rapid prototyping with scalable mass production. Understanding these dynamics empowers stakeholders to align manufacturing choices with project goals, cost parameters, and sustainability objectives.