At the Fakuma International Trade Fair for Plastics Processing in Germany, an SLS machine hums quietly as a laser beam dances across a bed of nylon powder, layer by layer crafting a drone frame that marries the strength of carbon fiber with the lightweight efficiency of honeycomb structures. This is no lab experiment – it’s a manufacturing revolution reshaping industries from automotive to aerospace and healthcare: Selective Laser Sintering (SLS) combined with composite materials is rewriting the rules of what’s possible, where complex designs no longer mean compromising on performance.
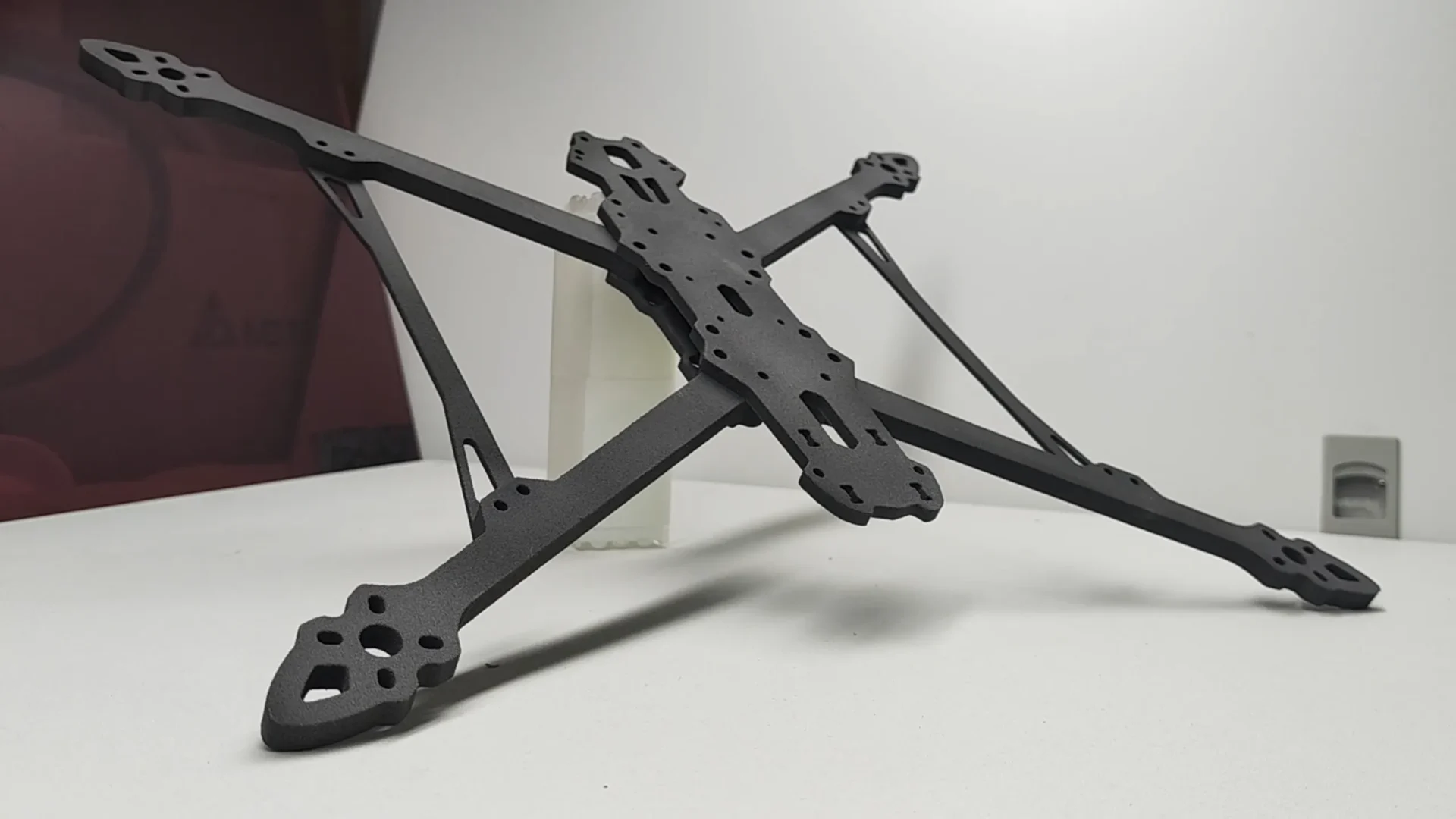
1. SLS Technology: The “Freedom Designer” of Additive Manufacturing
As a cornerstone of powder bed fusion technology, SLS acts like a tireless sculptor, using lasers to carve geometric marvels from powder:
- The Four-Act Magic of SLS
- Powder Spreading: A precision 刮刀 lays down a 0.1mm-thin layer of nylon powder, preheated just below its melting point to prime it for sintering;
- Laser Sintering: A CO₂ laser beam follows CAD slice data to selectively fuse powder particles, akin to drawing a 3D map in the snow;
- Layer-by-Layer Stacking: The build platform descends 0.1mm after each layer, allowing fresh powder to cover the surface and repeating the sintering process until the digital model materializes;
- Powder Debinding: After cooling, the part is unearthed from the unsintered powder “matrix,” much like an archaeological excavation revealing a masterpiece.
- Inherent Freedom in Design
The absence of needing support structures gives SLS unmatched ability to create geometries impossible with injection molding: think conformal cooling channels in car engines, lattice lightweighting in aerospace components, or bionic bone scaffolds in medical devices. As a Boeing additive manufacturing engineer puts it: “SLS turns our ‘maybe’ designs into ‘makeable’ realities.”
2. Composite Materials: The Formula Revolution Behind Supercharged Parts
If SLS is the stage, composite materials are the star performers. These “super materials,” made by combining polymer matrices with reinforcing agents, are redefining part performance:
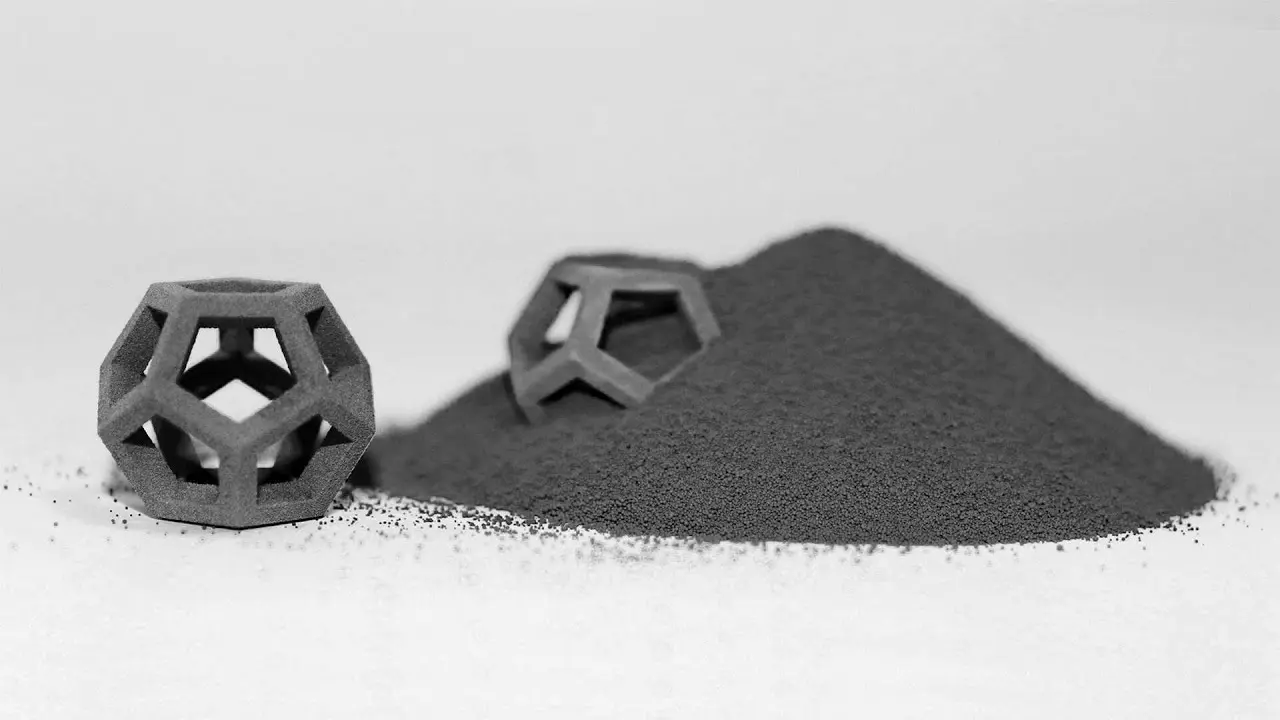
(1) The Reinforcement All-Stars: Masters of Specific Skills
Reinforcement | Core Advantages | Typical Applications | Industry Quote |
---|---|---|---|
Carbon Fiber | Higher strength-to-weight ratio than metal, conductive | Drone frames, racing car components | “Giving plastic the soul of steel” – Formula E engineer |
Glass Fiber | Cost-effective stiffness and heat resistance | Industrial gears, home appliance structural parts | “Performance leap at an affordable price” – Home appliance manufacturer |
Aramid Fiber | Impact resistance “gold standard” | Protective helmets, robot grippers | “Survives drone crash landings – a game-changer” – Parrot Drone Team |
Ceramic Particles | Extreme wear resistance | Injection mold inserts, mining drill bits | “Plastic that can go toe-to-toe with metal” – Caterpillar engineer |
(2) The Math of Performance Gains
- Strength Surge: Adding 30% carbon fiber to PA12 nylon boosts tensile strength from 50MPa to 120MPa – three times that of concrete’s compressive strength;
- Heat Resistance Breakthrough: Glass fiber-reinforced nylon raises the Heat Deflection Temperature (HDT) from 80°C to 170°C, ready for the harsh environment of car engine bays;
- Functional Expansion: Carbon nanotube-filled composites enable electrostatic discharge (ESD) properties, making plastic parts safe for electronics manufacturing floors.
3. Industrial Applications: From Lab to Production Line
At BMW’s Munich factory, SLS-manufactured carbon fiber-reinforced nylon engine brackets undergo rigorous testing. These topologically optimized parts are 40% lighter than traditional aluminum counterparts yet withstand the same vibration loads. This “lightweight without compromising strength” is the holy grail for industries:
(1) Aerospace: The Ultimate Lightweight Solution
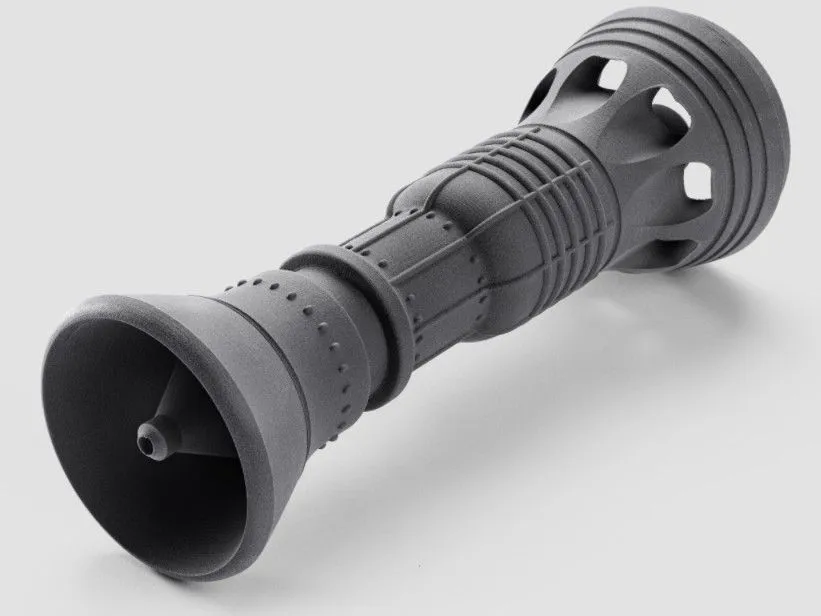
Over 200 SLS composite parts now fly in Airbus A350 cabins, from ventilation ducts to electronic brackets. Carbon fiber-reinforced nylon has helped reduce aircraft weight by hundreds of kilograms – equivalent to the fuel efficiency of adding 10 more passengers. NASA’s Mars rover sets a record: SLS-manufactured ceramic matrix composite heat shields withstood 1,200°C during Mars landing.
(2) Healthcare: The Precision of Personalization
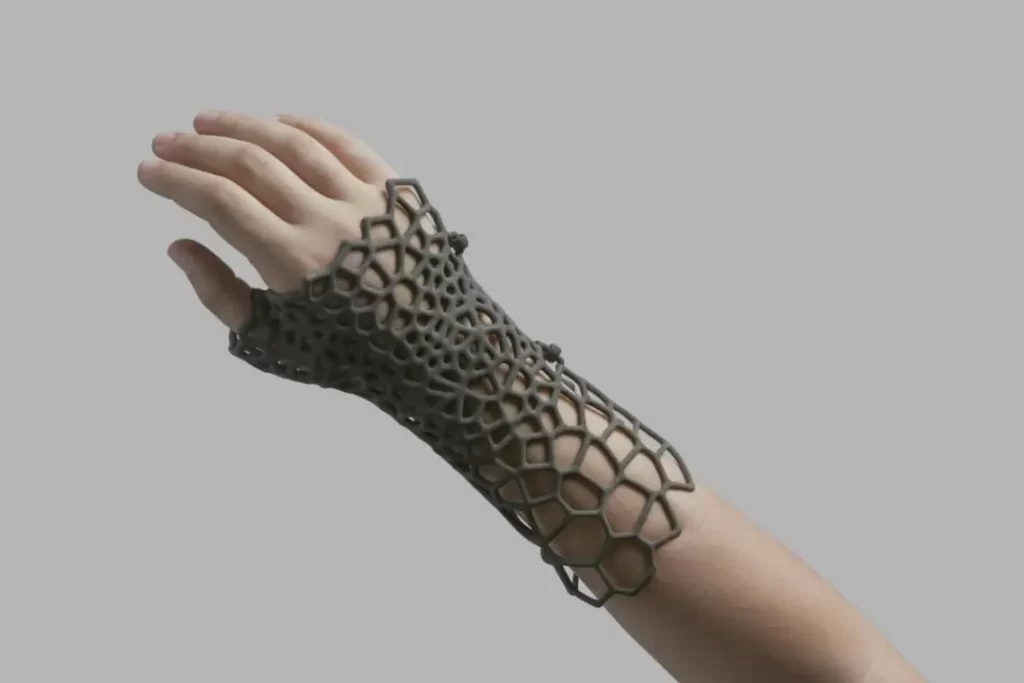
At the University Medical Center Utrecht in the Netherlands, doctors use CT data to directly 3D print scoliosis orthotics via SLS. These aramid fiber-reinforced flexible composite braces improve fit by 60% compared to traditional handcrafted ones and reduce skin complications by 82% thanks to complex breathable designs. “This is 3D printing’s gift of personalization to healthcare,” says Prof. Van der Meer.
(3) Tooling Innovation: The “Swiss Army Knife” of Manufacturing
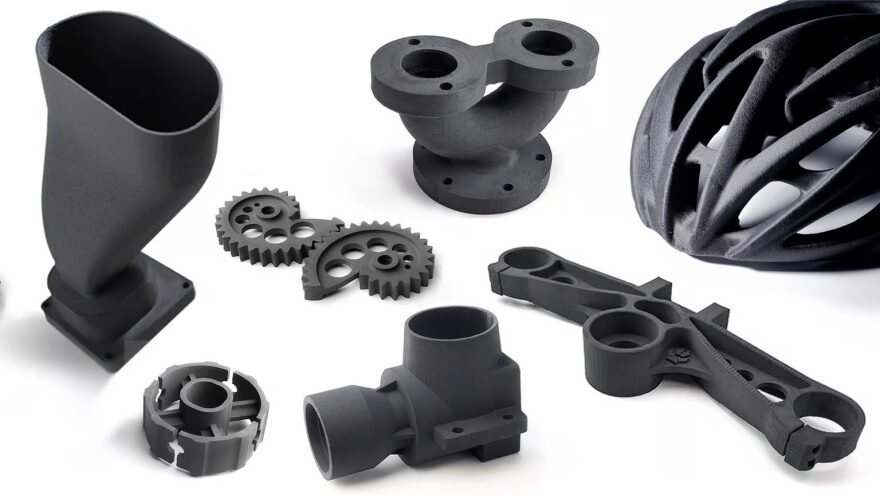
In Tesla’s Berlin factory, SLS-made glass fiber-reinforced nylon injection mold inserts are disrupting traditional tooling. These rapid-prototyped molds go from design to testing in 48 hours – 90% faster and 70% cheaper than steel molds. “No more paying premium prices for low-volume production,” marvels Production Manager Markus.
4. Technical Challenges: The Path to Tomorrow
Despite its promise, SLS composites face real-world hurdles:
- Material Cost Barrier: Carbon fiber-reinforced nylon powders cost 3-5x more than standard nylon, limiting mass adoption;
- Narrow Process Window: Minute fluctuations in laser power, scan speed, or powder temperature can cause performance variations, requiring AI-driven real-time adjustments;
- Recycling Conundrum: Composite matrices and reinforcements are hard to separate, with only ~50% of unsintered powder currently recyclable.
But innovation is overcoming these: Germany’s EOS launched the M 400-4 with quad-laser systems, quadrupling print speeds; 3D Systems’ bio-based nylon composites cut carbon footprints by 30%; and MIT researchers use magnetic field orientation to align short fibers during sintering, boosting part strength by 200%.
5. The Future is Now: Five Trends Shaping Tomorrow
- Material Diversification: From PEEK high-temperature composites to graphene-enhanced conductive materials, more functional formulations are on the horizon;
- Intelligent Processes: AI-driven real-time monitoring will achieve “first-time-right” production with zero defects;
- Sustainability Drive: Bio-based polymers and recyclable reinforcements will make green manufacturing the norm;
- Multi-Material Integration: Printing parts with rigid supports and flexible joints in one go is being tested in labs;
- Industry Standardization: Standards like ASTM F3303 will pave the way for composite parts in highly regulated sectors like aerospace.
Conclusion: Reimagining the Philosophy of Manufacturing
When SLS lasers first fused composite powders, they didn’t just create a part – they ignited a new manufacturing mindset: Complexity is no longer an enemy of cost but a catalyst for innovation; weight is no longer a limit on performance but a variable in design. From car chassis to Mars rovers, medical braces to industrial tools, this revolution proves: Future manufacturing isn’t about mimicking the past – it’s about redefining what’s possible.