Imagine creating intricate, durable plastic parts with complex internal channels or interlocking features, straight from a digital file, without the headache of support structures. Picture producing small batches of functional, end-use components with properties rivaling injection molding, faster and more flexibly than ever before. This isn’t science fiction; it’s the reality enabled by Selective Laser Sintering (SLS) 3D printing, a technology rapidly reshaping prototyping, manufacturing, and product design as we head further into 2025.
So, what exactly is SLS? At its core, SLS is a powder bed fusion additive manufacturing process. It works by using a high-power laser to selectively fuse, or sinter, powdered polymer material (like nylon) together, layer by meticulous layer, based on a 3D model. One of its most significant advantages is that the surrounding unsintered powder acts as a natural support structure for the part during printing. This unlocks incredible design freedom, allowing for complex geometries that are difficult or impossible to achieve with other methods, and enables the efficient batch production of multiple parts nested within the build volume. The resulting components are known for their good mechanical properties and durability, making them suitable for demanding functional applications.
Why is SLS grabbing the spotlight in 2025? While the technology isn’t brand new, several factors are converging to make it more relevant and accessible than ever:
- Increased Accessibility: The emergence of more compact and cost-effective SLS systems is breaking down previous barriers to entry.
- Material Innovation: The range of available SLS materials continues to expand beyond standard nylons, incorporating flexible TPUs and reinforced composites (like carbon-fiber or glass-filled variants), opening doors to new applications.
- Speed & Efficiency Gains: Newer machines boast faster scanning systems and optimized thermal management, reducing overall print times.
- Proven Track Record: SLS is increasingly trusted across demanding industries like aerospace, automotive, medical device manufacturing, consumer goods, and industrial tooling for producing reliable, high-quality parts.
Whether you’re an engineer needing robust functional prototypes, a manufacturer exploring low-volume production, a designer pushing geometric boundaries, or a service bureau looking to expand capabilities, understanding the current SLS landscape is crucial.
In this comprehensive guide, we’ll navigate the world of SLS 3D printing in 2025. We will:
- Dive into the top SLS printers available on the market today.
- Provide detailed reviews and analysis of leading models, including a look at offerings from Zongheng3D.
- Equip you with a thorough buying guide, outlining the critical factors to consider before investing.
- Explore essential material considerations and demystify post-processing workflows.
Get ready to explore the printers, processes, and considerations that define state-of-the-art SLS 3D printing and discover how this powerful technology can benefit your projects and business.
Unlocking SLS: Your Guide to the Core Concepts and Lingo of Powder Bed Fusion
So, you’re intrigued by the potential of Selective Laser Sintering (SLS) 3D printing? Maybe you’ve seen the incredible parts it can produce – complex, durable, and often support-free. But before diving into specific machines or debating which model is “best,” it’s crucial to get comfortable with the underlying concepts and terminology. Think of it like learning the basics of cooking before trying to master a complex recipe; understanding these fundamentals empowers you to ask the right questions and make informed decisions.
Let’s break down the essential SLS jargon you’ll encounter:
- Build Volume: How Big Can You Go (and How Many)?
Quite simply, the build volume (or build envelope) is the maximum physical size of a part, or a batch of parts, that an SLS printer can create in a single print run. It’s typically expressed in three dimensions: Length x Width x Height (e.g., 300mm x 300mm x 400mm or 11.8″ x 11.8″ x 15.7″).
- Why it matters:
- Maximum Part Size: Directly limits the dimensions of a single object you can print.
- Batch Capacity: Because SLS doesn’t need support structures, you can nest multiple parts within the entire 3D volume. A larger build volume allows for higher throughput by printing more parts simultaneously. Think of it like oven space – a bigger oven lets you bake more cookies at once!
- Orientation Flexibility: More space provides options for orienting parts to optimize strength or surface finish.
- Laser Type & Power: The Heart of the Sintering Process
The laser is what fuses the powder particles together. Understanding its characteristics is key:
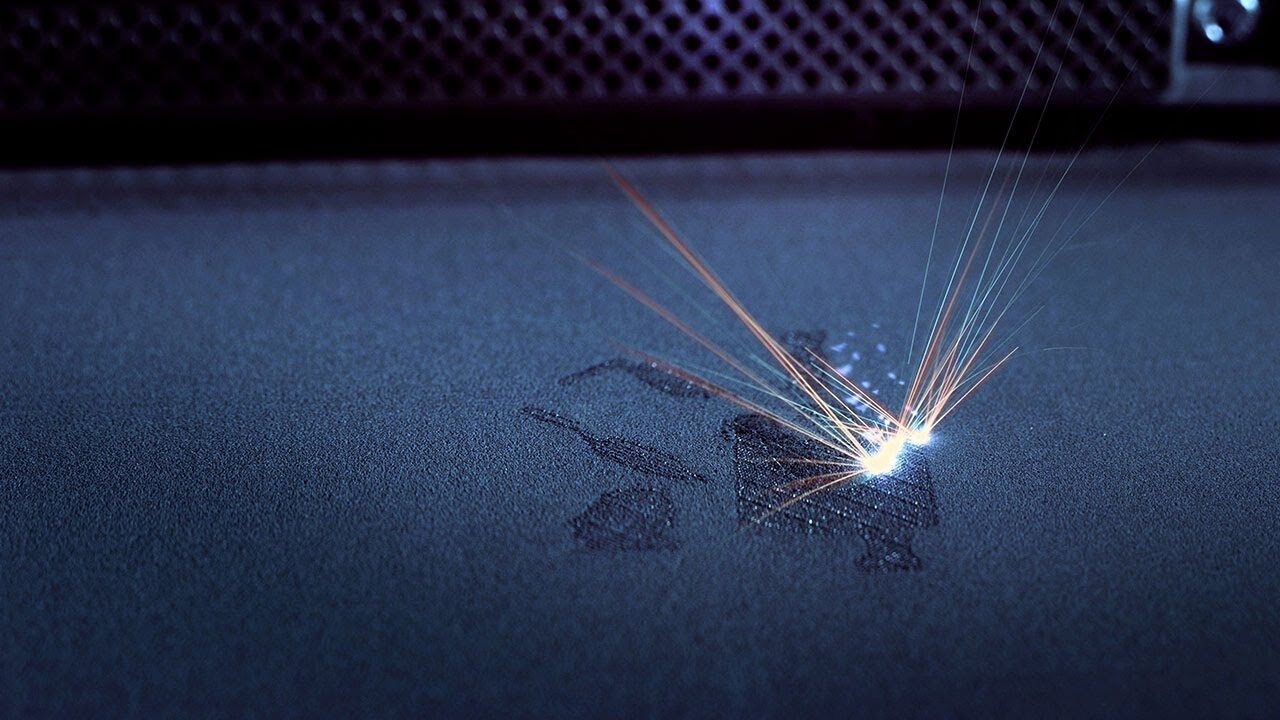
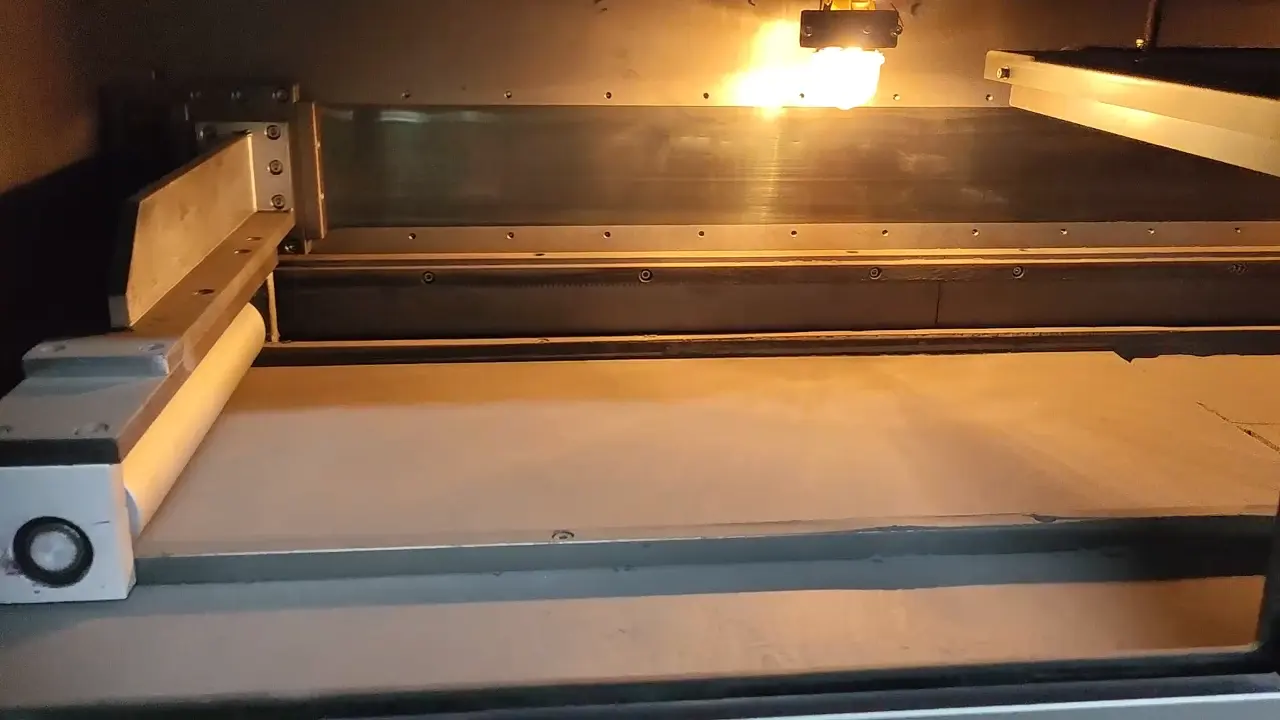
- Laser Type:
- CO2 Lasers: The traditional workhorse for many SLS systems, particularly effective with standard nylon materials (like PA12). They generally offer a good balance of cost and performance.
- Fiber Lasers: Often found in newer or higher-end systems. They can offer different absorption characteristics, potentially enabling work with a broader range of materials (including some composites or higher-temperature polymers) and sometimes allowing for finer spot sizes or faster scanning.
- Laser Power (Watts – W): Higher power generally translates to:
- Faster Sintering: More energy delivered means the powder can be fused more quickly, potentially speeding up the print.
- Material Capability: Some advanced materials require higher energy density to melt and fuse properly.
- Important Note: It’s not just about raw power; how the power is controlled and delivered (including the laser’s spot size, which influences resolution) is equally critical.
- Layer Thickness & Resolution: Defining Detail and Finish
This refers to the height of each individual layer of powder that the printer spreads and sinters.
- Layer Thickness: Measured in microns (µm) or millimeters (mm), typical values range from around 80µm to 150µm.
- Impact:
- Vertical Resolution: Thinner layers mean finer detail on vertical surfaces and less noticeable “stair-stepping” on curved or angled geometries, resulting in a smoother surface finish out of the printer.
- Print Time: Thinner layers mean more layers are needed to build the same part, significantly increasing the total print time.
- Trade-off: You often choose between higher speed (thicker layers) and finer detail/smoother finish (thinner layers).
- XY Resolution: While layer thickness defines vertical detail, the laser spot size and beam control system largely determine the resolution in the horizontal (X and Y) plane – the minimum feature size the laser can accurately create.
- Scan Speed: How Fast Does the Laser Dance?
This is the speed at which the laser beam moves across the powder bed while sintering. It’s usually measured in millimeters per second (mm/s) or meters per second (m/s).
- Direct Impact: Faster scan speeds directly contribute to shorter layer times and thus, a faster overall build time.
- Potential Considerations: Extremely high speeds need sophisticated control systems (galvanometers) to maintain accuracy. There can be a trade-off between maximum speed and the ability to precisely sinter fine features or sharp corners.
- Thermal Control & Heating: The Unsung Hero of Quality
This might be the most critical, yet often overlooked, aspect of SLS. Unlike some other 3D printing processes, SLS requires precise temperature management throughout the build chamber.
- Why it’s Crucial: The powder bed is heated to a temperature just below the material’s melting point. The laser then only needs to add a small amount of extra energy to cause sintering.
- Prevents Warping: Uniform heating minimizes thermal stress and prevents parts from warping or curling as they build.
- Ensures Good Fusion: Consistent temperature leads to better layer-to-layer bonding and more isotropic (uniform in all directions) part properties.
- Accuracy: Stable thermal conditions contribute significantly to dimensional accuracy.
- Key Components: Systems employ multiple heaters (e.g., radiant heaters above the bed, heating elements around the chamber) and sensors to maintain a stable and uniform thermal environment.
- Powder Refresh Rate: Balancing Cost, Quality, and Sustainability
You don’t just throw away all the unsintered powder after a build! However, the powder that was heated in the build chamber (even if not sintered) undergoes some thermal stress. To ensure consistent part quality in subsequent builds, this used powder is typically mixed with virgin (new) powder.
- Refresh Rate: This is the ratio or percentage of new powder that needs to be added to the recycled powder for the next print job (e.g., a 50% refresh rate means a 50/50 mix of used and virgin powder).
- Why it Matters:
- Cost: Lower refresh rates (meaning you recycle more powder) significantly reduce material costs per part.
- Part Properties: Using powder that’s been thermally cycled too many times can affect the mechanical properties and consistency of printed parts. Manufacturers specify recommended refresh rates to maintain quality.
- Sustainability: Higher recyclability means less waste.
- Open vs. Closed Material Systems: Freedom vs. Guaranteed Performance
This refers to the printer manufacturer’s policy on which materials you can use:
Feature | Closed Material System | Open Material System |
Definition | Only manufacturer-validated materials allowed | Can use materials from third-party suppliers |
Pros | Guaranteed performance, optimized parameters, easier workflow, often simpler support | Material flexibility, potential cost savings, ability to experiment/develop new materials |
Cons | Limited material choice, materials often more expensive, vendor lock-in | Requires user validation, parameter tuning needed, potentially more complex support, results not guaranteed by printer OEM |
Best Suited For | Production environments prioritizing reliability & ease-of-use | R&D, cost-sensitive users willing to invest time in validation, specific material needs not met by OEM |
Why does all this matter? Because understanding these core concepts moves you from simply looking at brochures to critically evaluating specifications. When a salesperson mentions the “build volume,” “refresh rate,” or “laser type,” you’ll know precisely what they mean and, more importantly, why it’s relevant to your specific needs. This foundational knowledge is your first step towards choosing the SLS technology that will truly empower your projects.
Your Essential SLS Buying Guide: Navigating the Maze to Find Your Perfect Match
Buying an SLS 3D printer isn’t like picking up a new office gadget; it’s a significant capital investment with long-term implications for your workflow, costs, and capabilities. Jumping in without a clear strategy can lead to buyer’s remorse – owning a machine that’s oversized, undersized, too complex, too simple, or simply incompatible with your real-world needs.
Think of this guide as your roadmap. We’ll walk through the crucial questions you need to ask and the factors you absolutely must evaluate before signing that purchase order. Let’s ensure your chosen SLS printer becomes a powerful asset, not an expensive paperweight.
A. Start with Why: Define Your Application (The MOST Critical Step!)
Before you even glance at a printer brochure, get crystal clear on what you intend to do with the SLS printer. Everything else flows from this. Ask yourself and your team:
- Primary Use Case?
- Visual Prototypes: Just need to check form and fit? Lower accuracy might be acceptable.
- Functional Prototypes: Need parts that withstand testing and mimic end-use properties? Material properties and accuracy are key.
- End-Use Parts / Low-Volume Production: Are you making parts for sale or final assembly? Reliability, repeatability, specific material certifications, and throughput are paramount.
- Jigs, Fixtures, Tooling: Need durable, potentially customized tools for your manufacturing line?
- What Materials Will You Actually Use?
- Do you primarily need standard PA12 (Nylon 12)?
- Do you require the flexibility of TPU?
- Need the specific properties of PA11 (bio-based, high ductility)?
- Do you anticipate needing reinforced materials like Glass-Filled (GF) or Carbon-Filled (CF) Nylon for extra strength or stiffness? Be specific!
- What Level of Detail and Accuracy is Required?
- What are the typical tolerances for your parts? (+/- mm or inches?)
- Do your designs involve very fine features, thin walls, or intricate details?
- What is Your Expected Volume and Throughput?
- How many parts do you expect to print per week or month?
- What is the typical size of your parts? (This influences how many fit in a build).
- How quickly do you need parts? (Consider the entire cycle: print time + cooling time + post-processing time).
Be honest and realistic here. Don’t buy a production-scale machine if you only need occasional prototypes, and don’t expect a benchtop model to handle high-volume manufacturing demands.
B. Decode the Spec Sheet: Key Technical Specifications to Evaluate
Once you know your ‘why,’ you can start comparing machines based on relevant technical specs:
- Build Volume: We covered this in the fundamentals, but now relate it to your application. Is it large enough for your biggest anticipated single part? Crucially, is it sized appropriately to nest enough of your typical parts for efficient batch production? Don’t just look at the max dimensions; consider the usable volume and how your common parts will fit.
- Material Compatibility: Does the printer officially support the specific materials you identified in Step A? Check beyond just “Nylon” – does it support PA12, PA11, specific TPU grades, or filled composites if you need them? Also, consider the open vs. closed material system question (more on this below).
- Resolution & Accuracy: Look at the specified layer thickness options (e.g., 0.1mm, 0.12mm) and understand the trade-off between detail and speed. Ask the manufacturer for documented dimensional accuracy specifications (e.g., +/- 0.3mm or a percentage of the dimension). Crucially, request benchmark parts printed from your own files to verify real-world results.
- Print Speed & Throughput: This is more complex than just looking at the laser’s scan speed. Consider the entire cycle:
- Build Rate: Often measured in vertical height per hour (e.g., cm/hour).
- Cooling Time: This can be significant in SLS (hours, sometimes even a day or two for large builds) and is often not included in advertised “print speeds.” Faster cooling cycles can dramatically improve overall throughput.
- Total Cycle Time: Calculate the realistic time from starting a print to having usable parts (Print + Cool + Post-Process).
C. Material World: Deeper Dive into Powder Considerations
Materials are the lifeblood of your SLS operation. Think about:
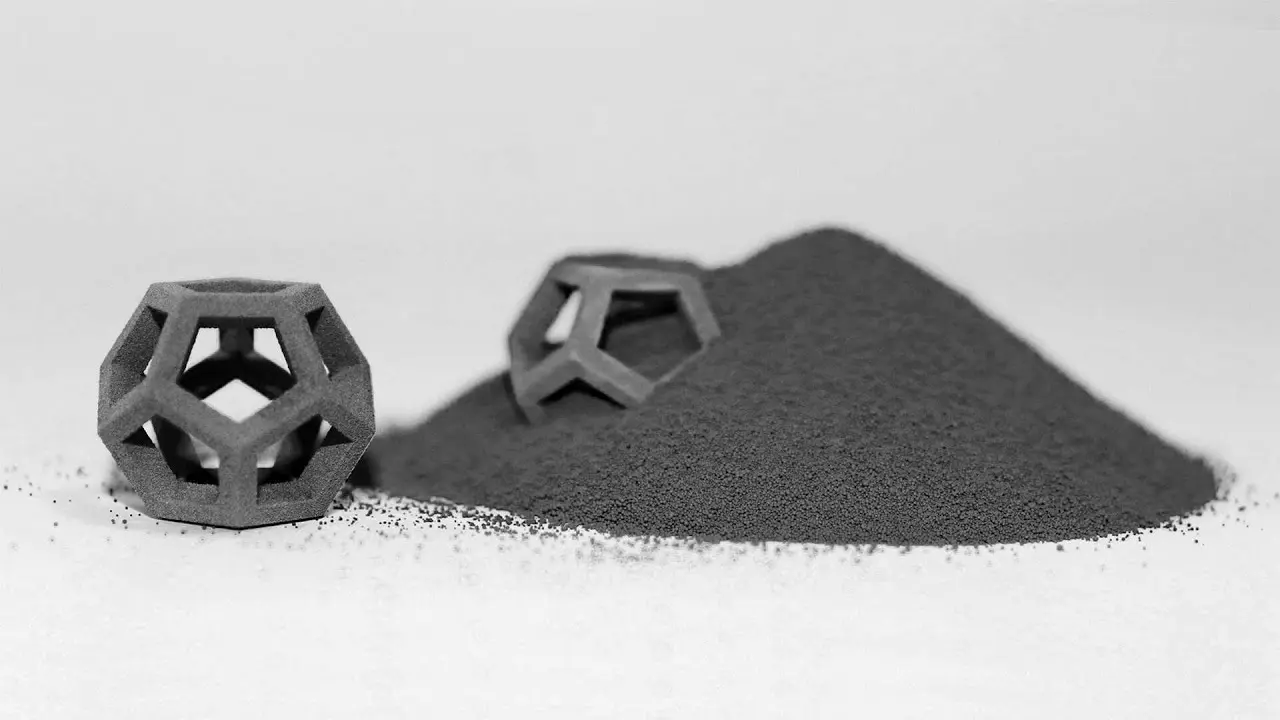
- Availability & Cost: What are the per-kilogram costs of the primary materials you’ll use? Are they readily available from the manufacturer or third parties (if an open system)? Factor in shipping and storage.
- Powder Handling & Safety: SLS powders are fine and require careful handling to avoid inhalation and potential dust explosion risks (especially in large quantities). What are the manufacturer’s recommendations for storage, handling, and Personal Protective Equipment (PPE)? Is specialized ventilation needed?
- Refresh Rate Impact: Remember the refresh rate (mix of used and new powder)? A lower refresh rate is generally better for costs, but follow manufacturer guidelines to ensure part quality. Factor the cost of virgin powder needed for refreshing into your material cost calculations!
- Open vs. Closed Systems:
- Closed: Simpler, validated parameters, guaranteed results with OEM materials, but higher material costs and limited choice.
- Open: Potential for lower material costs, wider material variety (including R&D), but requires you to validate parameters and assumes more process risk.
D. Don’t Forget the Digital: Software & Workflow Integration
The physical printer is only part of the equation. How easy is it to use?
- Preparation Software (Slicing): Is the software intuitive for orienting parts, nesting them efficiently for batch builds, and applying print parameters?
- Machine Control Software: How easy is it to start, monitor, and manage print jobs? Are there remote monitoring capabilities? Error reporting?
- CAD/CAM Integration: Does the workflow integrate smoothly with your existing design software? What file types are supported (.STL, .3MF, etc.)?
- User Interface (UI): Is the interface on the machine itself clear and user-friendly?
A clunky or complex software workflow can become a major bottleneck and source of frustration. Look for demos!
E. The Elephant in the Room: Hardware & Facility Requirements
This is where buyers often get caught out. An SLS printer needs a suitable home:
- Footprint & Weight: These machines can be large and heavy. Do you have the physical floor space? Can your floor support the weight? Consider space around the machine for access and maintenance.
- Power Requirements: Check the voltage (e.g., 208V, 400V), phase (e.g., 3-phase), and amperage requirements. Do you need dedicated circuits? Factor in the cost of electrical upgrades if needed.
- Ancillary Systems:
- Compressed Air: Often required for cleaning or machine operation. Do you have a suitable supply?
- Inert Gas: Some systems or materials benefit from or require a Nitrogen (N2) atmosphere to prevent oxidation and improve part quality. This requires N2 supply (generator or bottles) and associated plumbing/safety measures.
- Mandatory Ancillary Equipment: You will need more than just the printer:
- Breakout Station: For safely removing parts from the cool powder cake.
- Powder Sieving/Mixing Station: To recycle unused powder and mix it according to the refresh rate.
- Blasting Cabinet: For cleaning powder off parts (e.g., bead blasting, sand blasting).
- Environmental Controls: SLS requires a reasonably stable environment. Consider:
- HVAC: Temperature and humidity control are important for machine performance and powder handling.
- Powder Containment: How will you manage airborne powder during loading, unloading, and post-processing?
F. It’s Not Over ‘Til It’s Finished: Post-Processing Needs
Printing is just the first step. What happens after the build is complete and cooled?
- Cooling Time: As mentioned, this can be lengthy. Factor it into your lead times.
- Breakout & Depowdering: How easy is it to remove parts from the cake? How much manual labor is involved in cleaning off residual powder? Does the manufacturer offer integrated or efficient breakout solutions?
- Cleaning/Surface Finishing: Most SLS parts require bead blasting or similar to achieve a finished surface. Do you need further finishing like dyeing, smoothing (vibro-polishing, chemical smoothing), or painting?
- Labor & Equipment Costs: Account for the time, personnel, and equipment (blasting cabinets, polishing machines, dye stations) needed for these post-processing steps.
G. Show Me the Money: Total Cost of Ownership (TCO) & ROI
The sticker price is just the beginning. Calculate the Total Cost of Ownership:
- Initial Purchase Price: Printer + mandatory ancillary equipment (breakout, sieving, blasting).
- Installation & Training: Often separate costs.
- Material Costs: Include the cost of virgin powder and the ongoing cost associated with the refresh rate. This is a major recurring expense!
- Maintenance & Service Contracts: Highly recommended for industrial equipment. What are the annual costs? What do they cover?
- Consumables: Filters, potentially laser lifetime/replacement costs down the line.
- Operational Costs: Electricity (these machines draw significant power), compressed air/nitrogen, labor for operation and post-processing.
Once you have a realistic TCO, you can start calculating the potential Return on Investment (ROI). How will the printer save you money (e.g., reduced prototyping costs, less outsourcing) or make you money (e.g., faster time-to-market, new service offerings)?
H. Who You Gonna Call? Manufacturer Support & Reliability
You’re entering a long-term relationship with the vendor. Assess their support infrastructure:
- Warranty: What are the standard warranty terms? What’s covered?
- Service Contracts: What are the options for ongoing support and preventative maintenance? What are the guaranteed response times? Is local support available?
- Manufacturer Reputation: Research the manufacturer’s track record. Talk to existing users if possible. Read reviews and case studies. Are they known for reliability?
- Training Resources: Do they offer comprehensive initial training? Are ongoing resources (online documentation, webinars, support portals) available?
Making the Choice:
Phew! That’s a lot to consider, right? But taking a structured approach through these points is essential. There’s rarely a single “best” SLS printer – only the best SLS printer for your specific application and circumstances. By carefully evaluating your needs against these technical, operational, and financial factors, you’ll be well-equipped to make a confident, informed decision that propels your capabilities forward. Don’t rush it, do your homework, and ask vendors tough questions based on this framework.
Disclaimer: The SLS market evolves rapidly! New models emerge, and specifications change. The printers reviewed here represent key categories and notable players as of early 2025. Inclusion doesn’t constitute an exhaustive list or direct endorsement. Always conduct thorough research and request benchmark parts based on the latest available information directly from manufacturers.
Meet the Contenders: 2025’s Top SLS 3D Printers Under the Microscope
You understand the tech, you know what factors to weigh – now, let’s look at some specific machines grabbing attention in the 2025 Selective Laser Sintering landscape. Choosing the “best” is impossible without knowing your specific needs, budget, and application (remember Section III?), but exploring these representative models will give you a solid feel for what’s out there across different market segments.
We’ll examine each printer through a consistent lens, focusing on:
- Overview: What’s the machine’s general positioning and reputation?
- Key Specifications: Highlighting critical performance metrics.
- Pros: What are its main advantages?
- Cons: What are the potential drawbacks or limitations?
- Ideal Use Cases: Who is this printer really designed for?
- Price Category: A relative indication ($ = Most Accessible, = Highest Investment).
The Industrial Powerhouse: EOS P 396 (Conceptual Successor)
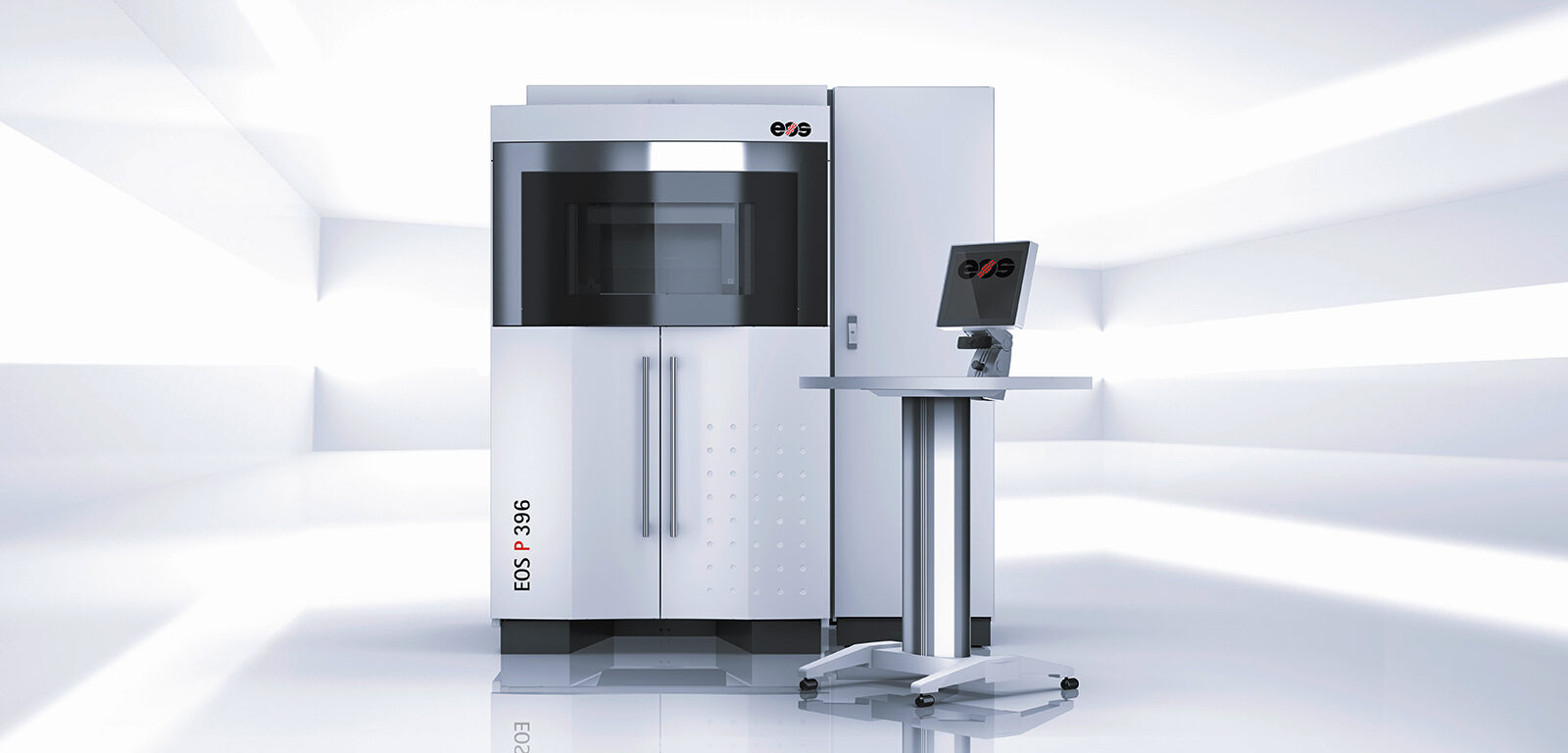
- Overview: Building on the legendary reliability of its predecessors, EOS continues to set a benchmark for industrial-grade SLS production. Machines in this class are known for their robustness, exceptional part quality, repeatability, and extensive material portfolio validated for demanding applications. Think high-volume, high-stakes manufacturing.
Key Specifications
Feature | Details |
Build Volume | 340 × 340 × 600 mm (13.4 × 13.4 × 23.6 in) |
Layer Resolution | 60–120 microns |
Laser System | 70W CO₂ laser with F-theta lens and high-speed scanner |
Scan Speed | Up to 6.0 m/s (19.7 ft/s) |
Materials | Nylon (PA11, PA12), elastomers, polypropylene, flame-retardant polyamides |
Power Supply | 400V / 32A, max. 10 kW consumption |
Dimensions | 1,840 × 1,175 × 2,100 mm (72.4 × 46.3 × 82.7 in) |
Weight | 1,060 kg (2,337 lbs) |
Software | EOS System Suite, Smart Scaling, IIoT integration via EOSCONNECT Core |
- Pros:
- Proven Reliability & Uptime: Built for continuous industrial operation.
- Excellent Part Quality & Consistency: Precise thermal control leads to highly accurate and repeatable parts.
- Wide Range of Validated Materials: Suitable for aerospace, medical, automotive standards.
- Strong Global Support Network: Established service and application support.
- Cons:
- Significant Initial Investment: Top-tier pricing for printer and ecosystem.
- Large Footprint & Facility Requirements: Needs dedicated industrial space and infrastructure.
- Often Closed Material System: Limits flexibility and can mean higher material costs.
- Ideal Use Cases: Serial production of end-use parts, applications requiring strict material certifications (medical/aerospace), large service bureaus, demanding functional prototypes.
The Versatile Workhorse: 3D Systems SLS 380 (Conceptual Model)
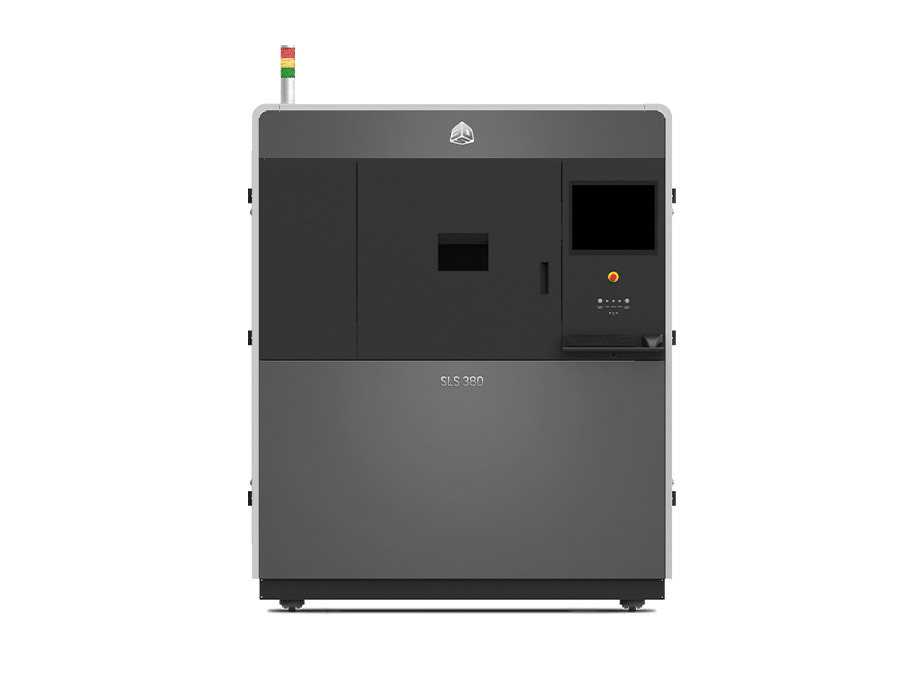
- Overview: 3D Systems offers compelling alternatives often focused on balancing productivity, material flexibility, and ease of use within an industrial framework. Models like this hypothetical SLS 380 aim to provide high-quality results with potentially faster throughput features and integrated powder handling solutions.
Key Specifications
Feature | Details |
Build Volume | 381 × 330 × 460 mm (15 × 13 × 18 in) |
Layer Resolution | 0.08–0.12 mm (Z-axis) |
Technology | Selective Laser Sintering (SLS) with closed-loop thermal controls |
Laser System | Water-cooled laser with proprietary thermal management |
Materials | Polyamides, elastomers, thermoplastics (DuraForm® series) |
Dimensions | 1,740 × 1,230 × 2,300 mm |
Weight | 1,360 kg |
Software | 3D Sprint® (unified workflow) + 3D Connect for IIoT integration |
Key Innovation | 100,000 thermal data samples/sec via IR camera for real-time adjustments |
- Pros:
- Strong Performance & Throughput: Designed for efficient production workflows.
- Integrated Ecosystem: Often features well-integrated powder management solutions.
- Established Manufacturer Support: Backed by a major player in the additive manufacturing space.
- Good Material Range: Covers common industrial needs effectively.
- Cons:
- Substantial Investment: Still a high-cost industrial system.
- Ecosystem Lock-in: While powerful, integrated systems can lean towards proprietary consumables/workflows.
- Ideal Use Cases: Functional prototyping, bridge manufacturing, direct production of nylon/composite parts, users valuing integrated material handling.
The Accessible Innovator: Formlabs Fuse 1+ 30W (Conceptual Evolution)
- Overview: Formlabs disrupted the market by making SLS significantly more accessible and affordable with their Fuse series. This conceptual evolution represents continued refinement – perhaps adding a bit more laser power for speed and material options, while retaining the focus on ease-of-use and a smaller footprint suitable for workshops and design labs rather than massive factory floors.
Key Specifications
Feature | Details |
Build Volume | 165 × 165 × 300 mm (6.5 × 6.5 × 11.8 in) |
Layer Resolution | 110 microns (0.004 in) |
Laser System | 30W Ytterbium Fiber (247 μm spot size, 1070 nm wavelength) |
Materials | Nylon 12, Nylon 11, Nylon 12 GF, Nylon 11 CF, TPU 90A, Polypropylene |
Build Speed | 10 mm/hour (up to 2× faster than original Fuse 1) |
Material Refresh Rate | 20%-50% (30%-50% with nitrogen purge) |
Dimensions | 64.5 × 68.5 × 107 cm (with stand: 165.5 cm height) |
Weight | 114 kg (without powder) |
Software | PreForm (free), compatible with Windows/macOS |
Key Innovation | Nitrogen purge for enhanced material performance |
- Pros:
- Lower Entry Cost: Significantly more affordable initial investment compared to industrial giants.
- Smaller Footprint & Reduced Facility Needs: Fits more easily into workshops or labs.
- Ease of Use: Designed with a user-friendly workflow from print setup to powder recovery.
- Excellent for Prototyping: Produces functional nylon parts ideal for iterative design.
- Cons:
- Smaller Build Volume: Limits part size and batch throughput.
- Slower Overall Throughput: Compared to larger industrial systems.
- More Limited Material Portfolio: Typically focused on core materials initially.
- Ideal Use Cases: Product design studios, engineering departments needing in-house functional prototypes, educational institutions, small businesses entering SLS.
The Open Speedster: Farsoon Flight HT403P (Based on existing tech)
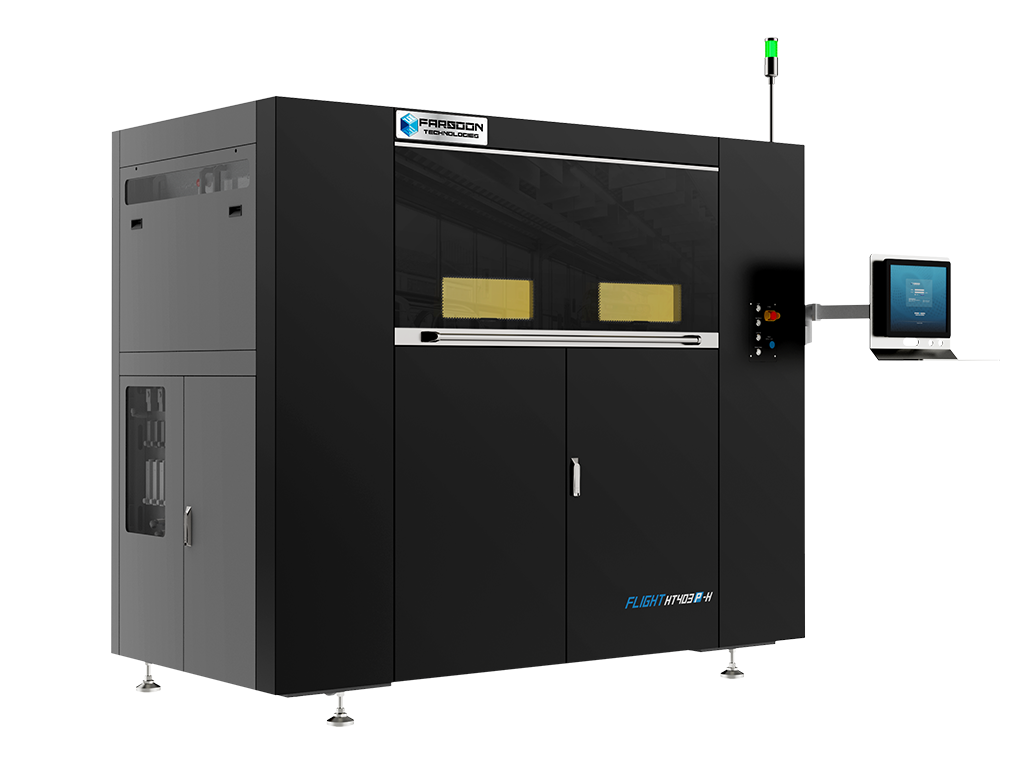
- Overview: Farsoon is known for pushing boundaries, particularly with their fiber laser-powered “Flight” technology and commitment to open material platforms. This offers users flexibility and potentially faster sintering speeds compared to traditional CO2 systems, appealing to those needing high productivity or wanting to experiment with materials.
Key Specifications
Feature | Details |
Build Volume | 400 × 400 × 450 mm (standard) / 400 × 400 × 540 mm (optional) |
Layer Thickness | 60–300 microns |
Laser System | Fiber laser (500W per KLIX3D; 300W per Farsoon; 100W CO₂ per Top3D) |
Scanning Speed | 15.2 m/s (CO₂ models) / 20 m/s (Flight fiber laser models) |
Max Chamber Temp | 220°C |
Materials | PA6, PA11, PA12, TPU, glass/carbon-filled polymers |
Dimensions | 2470 × 1500 × 2145 mm (KLIX3D)1 / 2540 × 1320 × 2220 mm (Farsoon) |
Weight | 3000–3100 kg |
Software | Open parameter system with real-time thermal monitoring |
- Pros:
- Potential for High Speed/Throughput: Fiber lasers can enable very fast scanning.
- Open Material Platform: Freedom to choose material suppliers, potential cost savings, R&D possibilities.
- Competitive Pricing: Often positioned aggressively compared to established giants.
- High-Temperature Capabilities (on specific models): Enables use of materials like PA6.
- Cons:
- Requires Process Expertise: Open systems mean the user takes more responsibility for parameter tuning and validation.
- Support Network: May be less extensive globally compared to EOS/3D Systems (highly region-dependent).
- Ideal Use Cases: Service bureaus needing high throughput, cost-conscious production environments, R&D departments, users needing specific non-standard materials or high-temp polymers.
The Cost-Effective Contender: Zongheng3D Supermaker SLS 2030 (Conceptual Model)
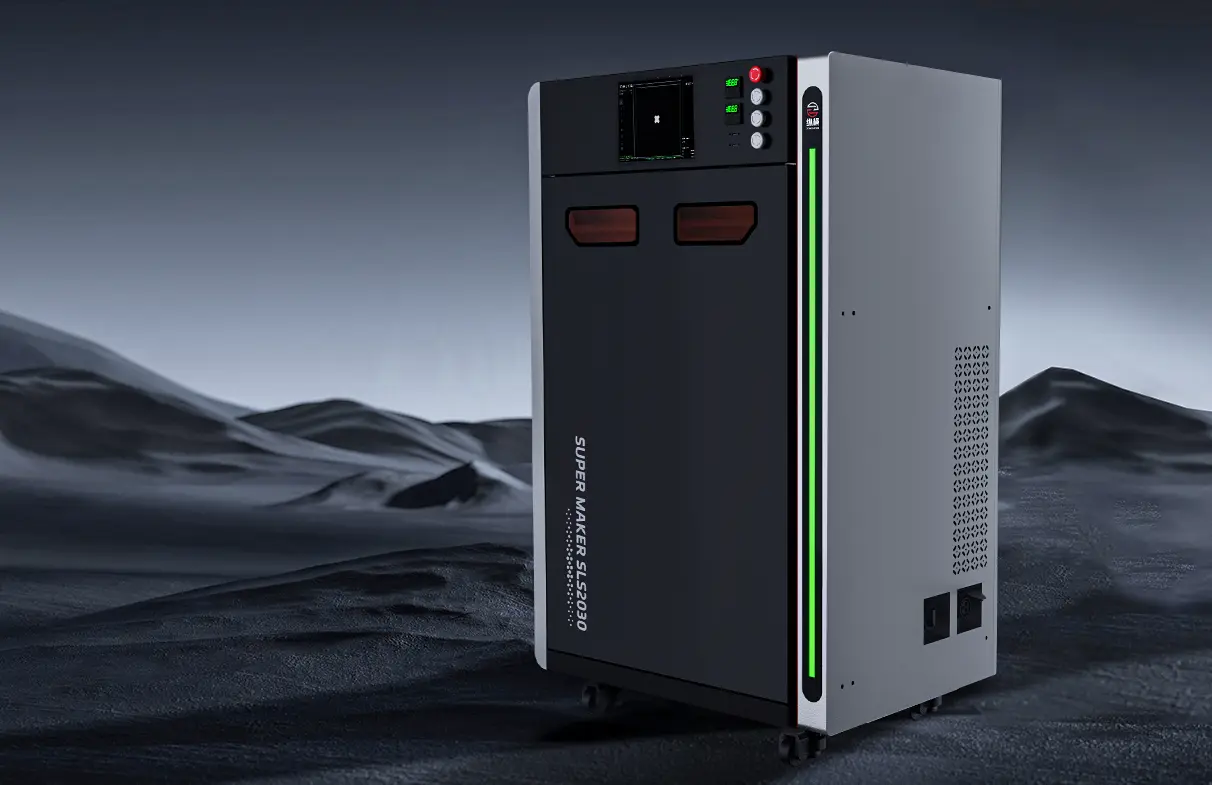
- Overview: Zongheng3D emerges as a significant player often focused on providing cost-effective, comprehensive SLS solutions, particularly appealing to small-to-medium enterprises (SMEs) or markets seeking value without sacrificing core functionality. Their approach often bundles necessary peripherals and emphasizes reliable performance with standard materials. The hypothetical Supermaker SLS 2030 represents a mid-sized offering from their lineup.
Key Specifications
Feature | Details |
Build Volume | 200 × 200 × 300 mm (7.9 × 7.9 × 11.8 in) |
Laser System | 40W fiber laser (247 μm spot size) |
Layer Thickness | 0.1–0.3 mm (100–300 microns) |
Scan Speed | 8–15 m/s |
Materials | PA11, PA12, TPU, glass-filled nylon |
Max Chamber Temp | 190°C |
Inert Gas | Nitrogen-purged environment |
Software | Proprietary slicer with real-time parameter adjustment and diagnostics |
Dimensions | 1000 × 800 × 1700 mm (39.4 × 31.5 × 66.9 in) |
Weight | 500 kg (without powder) |
Power Supply | 220V/50Hz |
Tank Capacity | 8 kg powder |
Post-Processing | Compatible with automated powder cleaning/sieving systems |
- Pros
- Cost Efficiency: 50% reduction in nitrogen/power use vs competitors7
- Material Flexibility: Open parameters for PA, TPU, and composites46
- Speed: 3000 cm³/h max build rate; full tank in 9–12 hours97 -Precision: 0.3 mm feature details with high-precision galvo system7
- Sustainability: Closed-loop powder recycling via post-process machines
- Cons
- Limited Build Volume: Smaller than industrial peers (e.g., Farsoon HT403P)
- Post-Processing Needs: Manual depowdering without optional systems
- Material Constraints: No high-temp polymers like PA6/PEKK
- Entry-Level Laser: 40W fiber laser vs 100W+ in premium models
- Ideal Use Cases:
- Rapid Prototyping: Functional nylon parts for automotive/aerospace
- Medical Devices: Biocompatible PA12 surgical guides/implants
- Custom Manufacturing: Small-batch end-use parts (24h turnaround)
- Mold Making: Low-volume injection molds with heat-resistant nylon
- Education/Research: Affordable industrial SLS for material testing
This overview provides a snapshot of the diverse SLS printer landscape in 2025. From high-throughput industrial beasts to accessible benchtop units and value-focused contenders, the options are broader than ever. Remember, the key is to match the machine’s capabilities, ecosystem, and cost to your specific requirements. Up next, we’ll put these printers head-to-head in a comparison table to make cross-referencing key specs even easier!
At a Glance: Comparing the Top SLS Printers of 2025
Feature | EOS P 396 | 3D Systems SLS 380 | Formlabs Fuse 1+ 30W | Farsoon Flight HT403P | Zongheng3D SLS2030 |
Build Volume | 340×340×600 mm | 381×330×460 mm | 165×165×300 mm | 400×400×540 mm | 200×200×300 mm |
Laser Power | 70W CO₂ | Water-cooled laser (unspec. W) | 30W Ytterbium Fiber | 100-500W Fiber/CO₂ (varies) | 40W Fiber |
Scan Speed | 6.0 m/s | – | – | 15-20 m/s | 8-15 m/s |
Key Materials | PA11/12, TPU, flame-retardant PA | DuraForm® PA/TPU/elastomers | Nylon 12, TPU 90A, PP | PA6, carbon-filled polymers | PA11/12, GF nylon, TPU |
Max Chamber Temp | – | Closed-loop thermal controls | Nitrogen-purged (ambient) | 220°C | 190°C |
Automation | EOSCONNECT IIoT integration | Fully automated powder handling | Optional Fuse Sift depowdering | Removable powder cartridges | Manual depowdering (auto optional) |
Price | $300k+ (estimated) | “Upon request” | $29,499 (starter) | “Upon request” | $50k-$100k (estimated) |
Ideal Use | Aerospace tooling, serial production | Factory-floor batch production | Dental models, functional prototypes | Automotive PA6 components | SME prototyping, education |
Throughput | 30% cost/part reduction | 2.7 L/hour [prev. response] | 10 mm/hour layer speed | High-temp industrial runs | 3000 cm³/hour max rate |
Software | EOS System Suite, Smart Scaling | 3D Sprint®, 3D Connect | PreForm | Open parameter system | Proprietary slicer with diagnostics |
Weight | 1,060 kg | 1,360 kg | 114 kg | 3,000-3,100 kg | 500 kg |
Post-Processing | Integrated quality reports | Automated recycling | Media blasting station | Advanced thermal controls | Sieving systems compatible |
Key Trends:
- Industrial Focus: EOS/Farsoon dominate large-format production, while Zongheng3D bridges the SME gap
- Material Innovation: PA6 (Farsoon) and flame-retardant grades (EOS) lead in aerospace/automotive
- Automation: 3D Systems’ closed-loop powder handling vs EOS’ IIoT integration for Industry 4.0 readiness
- Cost Scaling: Formlabs targets dental labs ($/part <$10), while Zongheng3D enables <$50k system entry
Selective Laser Sintering (SLS) systems vary significantly in material versatility, post-processing workflows, and powder-handling efficiency. Below, we analyze five industrial-grade printers—EOS P 396, 3D Systems SLS 380, Formlabs Fuse 1+ 30W, Farsoon Flight HT403P, and Zongheng3D SLS2030—focusing on their core capabilities in these critical areas.
1. EOS P 396
- Materials:
- Engineering Polymers: PA11, PA12, flame-retardant polyamides, TPU
- Industrial Focus: Aerospace tooling, automotive functional prototypes
- Post-Processing:
- Tumbling: Airbrushing + vibratory finishing for smooth surfaces
- Quality Reports: Integrated diagnostics for traceability
- Powder Management:
- Recycling: Proprietary algorithms for virgin/recycled powder ratios
- IIoT: EOSCONNECT Core for real-time powder health monitoring
2. 3D Systems SLS 380
- Materials:
- DuraForm® Series: PA, elastomers, glass-filled nylon
- High-Throughput: Optimized for 2.7L/hour production rates
- Post-Processing:
- Automated Depowdering: Closed-loop system with IR thermal imaging
- Surface Finish: Vibro-polishing compatibility for Ra <5μm
- Powder Management:
- Smart Recycling: 95% reuse rate with moisture-controlled hoppers
- Batch Control: 3D Connect software for multi-machine synchronization
3. Formlabs Fuse 1+ 30W
- Materials:
- Nylon-Based: PA12, PA11 CF, TPU 90A, polypropylene
- Biocompatibility: ISO 10993-5 certified options
- Post-Processing:
- Fuse Blast: Automated media blasting for intricate geometries
- Dyeing: CMYK immersion baths for color customization
- Powder Management:
- Fuse Sift: 20-50% refresh rate with nitrogen-assisted sieving
- Compact Workflow: Benchtop-compatible recycling for small labs
4. Farsoon Flight HT403P
- Materials:
- High-Temp Polymers: PA6, carbon-filled composites, PEKK
- Open Parameters: Custom material development (e.g., TIGITAL 3D-Set 371)
- Post-Processing:
- Farsoon PMS: Automated powder mixing/sieving with 20% refresh rate
- EC Station: Inert-gas cooling for 50% faster cycle times
- Powder Management:
- Bulk Handling: 50L+ capacity with RFID-tagged cartridges
- Multi-Printer Sync: PMS serves 3+ systems simultaneously
5. Zongheng3D SLS2030
- Materials:
- Cost-Optimized: PA11, PA12, TPU, glass-filled nylon
- Open Parameters: Adjustable laser power for experimental blends
- Post-Processing:
- Sieving Stations: Compatible with automated powder recovery
- Manual Depowdering: Standard workflow (auto systems optional)
- Powder Management:
- 8kg Capacity: Nitrogen-purged build chamber
- Smart Recycling: 30-50% refresh rate with real-time diagnostics
Comparative Summary
Printer | Material Edge | Post-Processing | Powder Management |
EOS P 396 | Flame-retardant PA for aerospace | Tumbling + quality reports | IIoT-driven recycling |
3D Systems SLS 380 | DuraForm® elastomers | Fully automated depowdering | Closed-loop, high-volume reuse |
Formlabs Fuse 1+ | Dental-grade biocompatibility | Media blasting + dyeing | Compact nitrogen integration |
Farsoon HT403P | PA6/PEKK for automotive | PMS/EC industrial workflow | RFID-tracked bulk handling |
Zongheng3D SLS2030 | Low-cost PA/TPU blends | Manual + optional automation | SME-friendly 8kg capacity |
Key Takeaway: EOS and Farsoon dominate high-temp industrial applications, while Formlabs and Zongheng3D cater to cost-sensitive labs. 3D Systems leads in factory-floor automation for serial production.
Beyond 2025: Peeking into the Future of SLS Technology
Selective Laser Sintering has already cemented its place as a powerful tool for prototyping and production. But the exciting part? It’s still evolving! The SLS technology you see today is a stepping stone to even more capable, efficient, and accessible systems tomorrow. While predicting the exact timeline is tricky, several key trends are shaping the future trajectory of SLS:
Here’s a glimpse of what’s likely on the horizon:
- Need for Speed: Faster Print Times
- Manufacturers are in a constant race to reduce overall cycle times. This isn’t just about the laser scanning faster (though that’s part of it, with more powerful lasers and advanced galvanometer controls).
- Expect improvements in thermal management systems allowing for quicker, yet still controlled, heating and cooling phases. Cooling time is a major bottleneck, and reducing it significantly boosts overall throughput.
- Optimized software algorithms will also play a role, refining scan strategies to sinter powder more efficiently without sacrificing quality.
- Material Marvels: Expanding the Palette
- While Nylon (PA12, PA11) and TPU are staples, the demand for a wider range of materials is pushing innovation.
- Look for more high-temperature polymers capable of withstanding demanding thermal environments (beyond even current PA6 capabilities).
- Expect continued development in reinforced composites (more advanced Carbon Fiber, Glass Fiber, or even ceramic-filled materials) offering tailored mechanical properties like extreme stiffness or impact resistance.
- More flexible materials with varying durometers and enhanced durability are also likely.
- Crucially, work continues on improving powder recyclability and lowering refresh rates across all material types to enhance sustainability and reduce costs.
- The Rise of Automation: Streamlining the Workflow
- The manual steps involved in SLS (powder loading, breakout, sieving, mixing) are ripe for automation.
- Expect more integrated and automated powder handling systems. Imagine closed-loop systems that manage powder from storage, through the printer, to recovery and refreshment with minimal operator intervention.
- Advances in automated depowdering and basic post-processing (like initial blasting or smoothing) integrated directly into the workflow or offered as modular robotic cells will reduce manual labor and improve consistency.
- Democratization Continues: Cost Reduction & Accessibility
- While high-end industrial systems will always represent a significant investment, the trend towards more affordable and accessible SLS printers (like the benchtop models) will likely continue.
- Increased competition and maturing technology should exert downward pressure on hardware costs.
- Efforts to lower material costs, particularly through improved refresh rates and potentially more open-source material development, will further reduce the barrier to entry and cost-per-part.
- Smarter Systems: Software and AI Integration
- Software is becoming increasingly sophisticated. Expect more AI-driven tools for:
- Optimized nesting: Automatically arranging parts in the build volume for maximum density and print success.
- Predictive maintenance: Using sensor data to anticipate potential machine issues before they cause downtime.
- Process simulation: Better predicting part properties and potential warping before printing.
- Automated parameter tuning: Simplifying the process of optimizing print settings for specific materials and geometries.
- Enhanced in-process monitoring using sensors and cameras will provide more real-time feedback on build quality.
- Software is becoming increasingly sophisticated. Expect more AI-driven tools for:
What This Means for Users:
The future of SLS points towards systems that are:
- Faster: Delivering parts more quickly.
- More Versatile: Capable of printing a wider array of functional materials.
- More Automated: Requiring less manual intervention and improving consistency.
- More Accessible: Lowering the barriers to adoption through reduced costs.
- Smarter: Easier to use and more reliable thanks to intelligent software.
While we’ve focused on the state-of-the-art in 2025, it’s clear that SLS is a dynamic field with significant innovation still ahead. Staying informed about these trends will be crucial for anyone leveraging this powerful additive manufacturing technology in the years to come.